Mold Maker: Design Review and Verification
Design review and verification are vital for a mold maker in injection molding. These steps ensure that an injection mold design will function properly, produce quality parts, and be cost-effective. Here’s a detailed breakdown:
Preliminary Design Review
Tips from The Mold Maker
Product Requirements: Check if the design meets specifications. Confirm dimensions, tolerances, and functionality are correct.
Part Geometry:Ensure the part shape is suitable for injection molding. Review draft angles and wall thickness. Make sure there are no problematic undercuts, unless side actions are planned.
Material Selection: Verify the material is appropriate for the part. Consider shrinkage, strength, and thermal properties.
Gate Location: Assess the gate position. It should ensure good flow and reduce warpage. Ensure it does not affect the part’s appearance or function.
Ejection System: Review the ejection system design. It must eject parts without causing damage.
Tips from The Mold Maker
Detailed Design Review
Mold Base: Ensure the mold base fits the injection molding machine. It should handle the production load.
Cooling System: Ensure that the cooling channels are adequately designed to provide uniform cooling and minimize cycle time while avoiding hotspots.
Venting: Confirm that adequate venting is provided to avoid air traps, which could lead to defects like burn marks or short shots.
Runner System: Review the runner and gating design to ensure balanced flow and minimize material wastage.
Parting Line: Evaluate the placement of the parting line to minimize flash and avoid complex parting surfaces that could complicate the mold machining process.
Detailed Design Review
Mold Flow Analysis: Conduct a mold flow analysis to simulate the filling process and identify potential issues like weld lines, air traps, and imbalanced flow.
Thermal Analysis: Perform a thermal analysis to evaluate the cooling efficiency and identify areas where cycle time can be reduced.
Structural Analysis: Analyze the mold structure to ensure it can withstand the pressures and forces during the injection process without deforming.
Insights from The Mold Maker
Final Design Verification
Tolerance Stack-Up Analysis: Verify that all tolerances, including those related to shrinkage and thermal expansion, are accounted for and that the final part will meet dimensional specifications.
Mold Assembly Check: Ensure that all components, including inserts, lifters, and slides, are properly integrated into the mold design and that assembly and disassembly are feasible.
Manufacturability Review: Confirm that the mold design is manufacturable within the capabilities of your tooling department, considering factors like machining complexity and surface finish requirements.
Tips from The Mold Maker
Prototype Testing
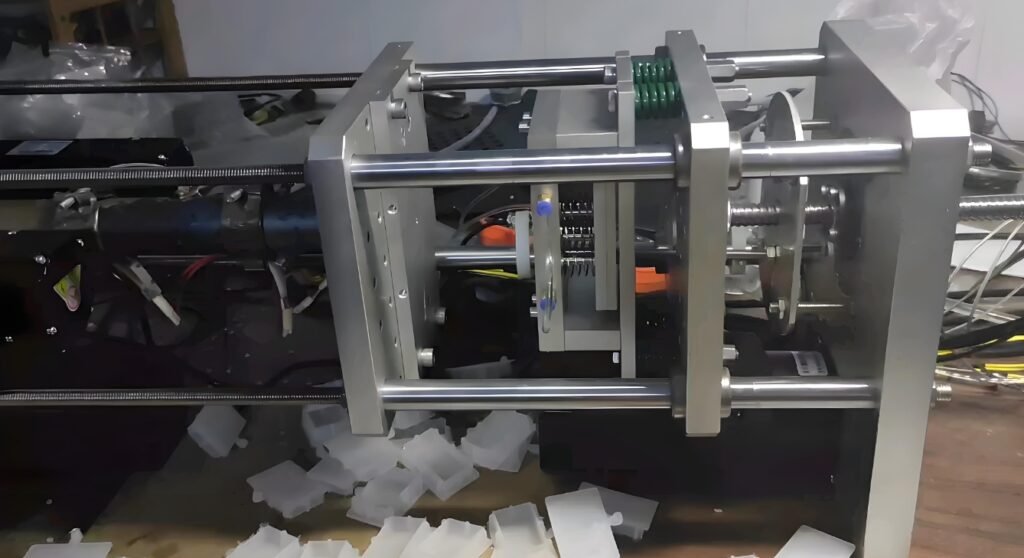
Prototype Mold: If necessary, create a prototype mold to test the design before committing to full-scale production. This allows for identifying and correcting issues in a less expensive, lower-risk environment.
Sample Runs: Conduct initial sample runs with the prototype or production mold to verify that it produces parts that meet all specifications.
Dimensional Inspection: Perform a dimensional inspection of the first articles to ensure they conform to the design tolerances.
Design Sign-Off
Final Approval: Once all reviews and tests are completed, obtain final approval from all relevant stakeholders, including design engineers, production engineers, and quality assurance teams.
Documentation: Ensure all design documentation, including CAD models, drawings, and simulation reports, are complete and stored for future reference.
Post-Production Monitoring
Process Monitoring: During the initial production runs, closely monitor the molding process to ensure consistent part quality and identify any potential issues early.
Feedback Loop: Establish a feedback loop with production teams to capture any issues that arise during production and implement continuous improvements to the mold design.