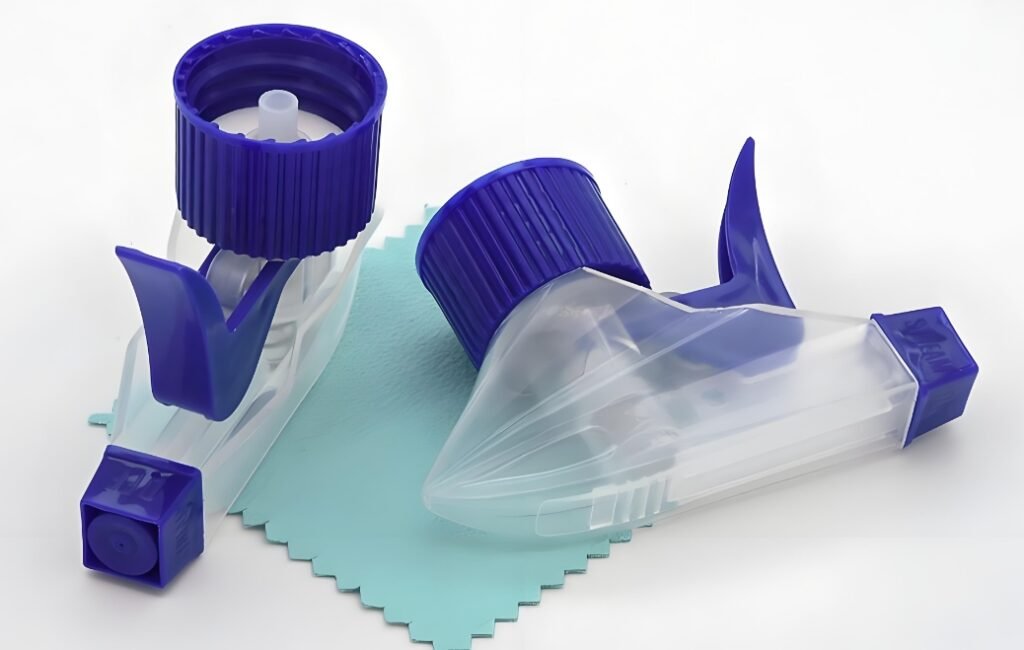
At Popper Mold-Tech, we received a call from a pharmaceutical company. They needed help with a project. The project was serious and required precision. They wanted us to make a medical injection mold. This wasn’t just any mold; it was for a critical medical device. This is where pharma mold making becomes very important.
We accepted the challenge. Medical molds need to be flawless. There is no room for error when people’s lives depend on it. As a mold maker, we knew the risks and the precautions we needed to take. There are three fatal precautions that every mold maker must follow in pharma mold making.
1. Material Safety
The first precaution is material safety. Medical products require special materials. These materials must be biocompatible. This means the plastic used won’t harm the body. It must be approved for medical use.
Our engineers selected the right material for this project. It had to be safe and durable. If the wrong material is chosen, it could cause serious problems. The device could break, or worse, harm the patient. The stakes were high. We could not afford mistakes.
We worked closely with the client to ensure the material met their requirements. This was one of the most important steps in the process. Every decision had to be carefully checked. Safety was our number one priority.
2. Precision and Tolerance
The second precaution is precision and tolerance. In pharma mold making, even the smallest error can lead to failure. The medical device had tiny, complex parts. The mold had to be perfect. There was no room for deviation.
Our team used advanced technology to create the mold. We worked with extreme care to ensure every part fit together. Even a fraction of a millimeter could cause problems. Precision was everything. We used the latest software to measure and adjust every detail.
The client trusted us to deliver a mold with perfect dimensions. If the mold failed, the device wouldn’t work. And if the device didn’t work, it could endanger lives. That’s why precision is so critical for a mold maker in this industry.
3. Sterility and Cleanroom Standards
The third fatal precaution is sterility. Medical devices must be made in clean conditions. Any contamination can ruin the device. It could lead to infections or complications when used in surgery or treatment.
At Popper Mold-Tech, we have a cleanroom where we produce medical molds. The environment is tightly controlled. We follow strict hygiene protocols. This ensures that no dust, germs, or other contaminants get into the mold.
We cleaned every piece of equipment before starting. Our workers followed all safety procedures. Each step was carefully monitored to maintain the sterile environment. If even the smallest particle got into the mold, it could ruin the entire batch. In pharma mold making, sterility is non-negotiable.
Facing the Challenge
As we worked through the project, we faced challenges. Pharma mold making is never easy. But as an experienced mold maker, we were prepared. We knew the risks, and we took every precaution seriously. We communicated with the client at every step. Transparency was important.
Our team was focused on delivering a mold that would meet the client’s high standards. The pressure was on, but we remained calm. Each precaution was followed carefully. We didn’t rush the process. We knew that speed could lead to mistakes, and mistakes in pharma mold making can be fatal.
Testing the Mold
Once the mold was complete, we tested it. We ran a series of tests to ensure that everything was perfect. The medical device parts were produced and inspected. Every piece was measured and checked for flaws.
The client was impressed with the results. Every part met their specifications. The material was safe. The precision was flawless. And the environment was sterile. The mold was a success.
Delivering Quality
At Popper Mold-Tech, we take pharma mold making very seriously. We understand the importance of safety, precision, and sterility. These three fatal precautions must never be ignored. As a mold maker, it’s our responsibility to ensure that the molds we produce are perfect.
The client was relieved. They knew that their project was in good hands. The medical device would now move forward, and lives would be saved. They thanked us for our hard work and dedication