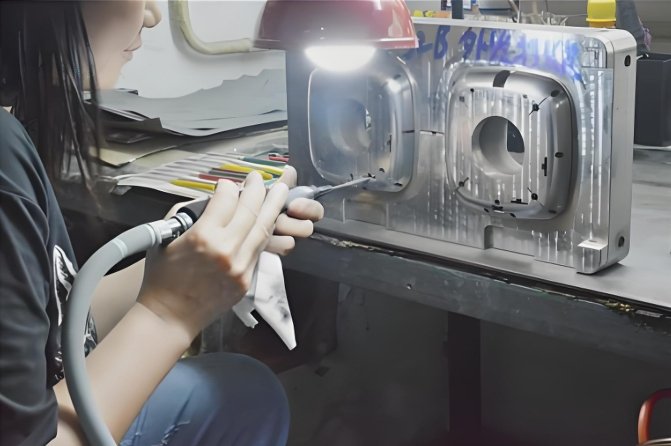
A top-notch injection mould company follows precise processes. These ensure efficient and accurate production. The steps involve design, tooling, molding, and quality checks. Each stage impacts the final product.
Step 1: Design Analysis
Every project begins with a design. Engineers study client requirements. They use advanced software to assess feasibility.
The design must suit injection molding. It must also align with the mold maker’s capabilities. Proper design saves time and cost.
Engineers refine the design to avoid flaws. They consider part thickness, material, and flow patterns. These factors ensure smooth production.
Step 2: Material Selection
Material choice is vital. The right material enhances durability and performance. An experienced injection mould company helps clients choose wisely.
Common materials include ABS, nylon, and polypropylene. The decision depends on the product’s purpose. Engineers evaluate temperature, strength, and flexibility.
Material selection also impacts costs. High-quality materials increase lifespan. This minimizes replacements.
Step 3: Mold Making
A skilled mold maker creates the tools for molding. This process demands precision. Molds must fit the product design perfectly.
Injection molds are made from steel or aluminum. Steel molds are durable and ideal for high-volume production. Aluminum molds are lightweight and faster to create.
The mold maker tests each mold thoroughly. They ensure it can handle repeated cycles. Poor molds lead to defects.
Step 4: Injection Molding
The core process is injection molding. This involves injecting molten plastic into the mold.
The machine applies pressure and heat. The plastic fills every cavity. After cooling, the part solidifies.
Cycle times vary based on part complexity. Advanced machines improve speed and accuracy.
Step 5: Quality Control
Quality checks are crucial. A reliable injection mould company inspects every part. This prevents defects from reaching clients.
Measurements confirm dimensional accuracy. Surface finishes are inspected for flaws. Functionality tests verify performance.
Defects like warping, sink marks, or short shots are identified. These issues are corrected immediately.
Step 6: Secondary Processes
Some parts need extra steps. This may include trimming, painting, or assembly.
Trimming removes excess material. Painting enhances aesthetics. Assembly ensures parts fit together.
Secondary processes add value to the product. They prepare it for the end user.
Advanced Technology in Injection Molding
Modern injection mould companies use advanced tools. CAD and CAM software streamline design. Automation boosts productivity.
Robotic systems reduce human error. They handle repetitive tasks with precision. AI improves quality checks by detecting minute flaws.
Technology reduces waste and speeds up production. It ensures clients get high-quality parts faster.
Sustainability in Injection Molding
Eco-friendly practices are growing. A good injection mould company reduces its carbon footprint.
Recycled materials are common. These lower waste and costs. Energy-efficient machines cut power usage.
Sustainable injection molds last longer. They reduce the need for replacements.
Applications of Injection Molding
Injection molding suits many industries. Automotive, medical, and electronics sectors rely on it.
- Automotive Parts
Car dashboards, bumpers, and trims are molded. These parts must be strong and lightweight. - Medical Devices
Syringes, implants, and enclosures use injection molds. Precision is vital for safety. - Electronics
Casings, connectors, and housings are common. They protect sensitive components. - Consumer Goods
Everyday items like toys, containers, and chairs are molded. This method ensures affordability.
Benefits of Working with a Quality Injection Mould Company
- Consistency
Parts are identical. This ensures reliability. - Speed
Efficient processes deliver products quickly. - Cost Savings
Defect reduction minimizes expenses. - Flexibility
Molds suit various designs and materials. - Durability
High-quality injection molds last long. They handle thousands of cycles.
Challenges in Injection Molding
- Material Waste
Poor planning leads to excess scrap. A good injection mould company minimizes waste. - Defects
Warping or bubbles ruin parts. Skilled mold makers prevent these issues. - High Initial Costs
Mold making is expensive. Long-term production justifies this cost.
How to Choose a Reliable Injection Mould Company
- Experience
Look for years in the industry. Experienced companies handle complex projects. - Technology
Ensure they use advanced machines. Modern tools enhance efficiency. - Customer Reviews
Read client feedback. It reveals the company’s reliability. - Custom Solutions
Every project is unique. The company should offer tailored services. - Certifications
Quality certifications prove expertise.
A quality injection mould company follows precise steps. Each process ensures high-quality parts.
Expert mold makers craft durable injection molds. Advanced injection molding produces consistent results.
Clients benefit from fast, cost-effective solutions. For reliable manufacturing, choose an experienced injection mould company.