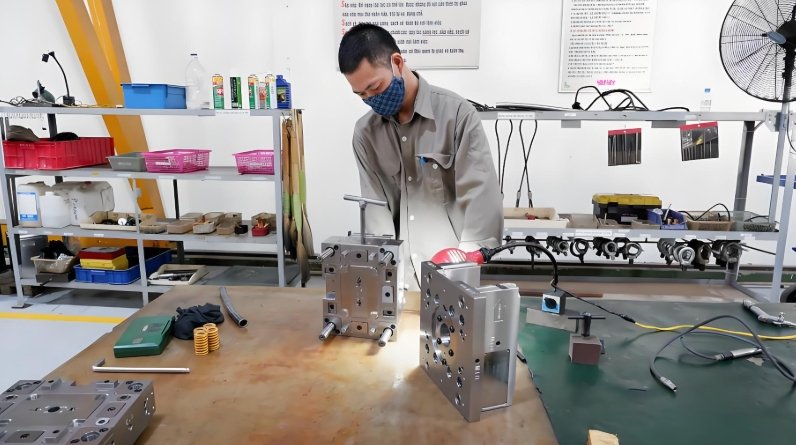
Electronics require precision. Every part must fit perfectly. This makes selecting an injection mould company critical.
The right company ensures accuracy. They deliver high-quality injection molds. They also meet strict deadlines.
Why Electronics Need Specialized Injection Molding
Electronic components are intricate. They often have tiny details. These require advanced injection molding.
Mistakes can lead to malfunctions. Poor parts can harm device performance. Only skilled mold makers can achieve such precision.
They craft molds for housings, connectors, and casings. This ensures parts meet tight tolerances.
Factors to Consider in an Injection Mould Company
- Experience
Choose a company with electronics experience. They understand the industry’s needs. - Capabilities
Ensure they can handle complex designs. Advanced machinery is crucial. - Material Knowledge
Electronics often need specialized plastics. The company must know materials like ABS, polycarbonate, and LCP. - Certifications
Look for ISO and RoHS certifications. This ensures compliance with regulations. - Quality Control
Their quality system should be robust. They must catch errors early.
The Role of Mold Makers
Skilled mold makers are vital. They design molds for precise results.
They use CAD software for accuracy. This ensures designs meet specifications.
Mold makers also ensure durability. Electronics need molds that last. Repeated use should not degrade them.
Injection Molds for Electronics
Injection molds shape parts. For electronics, they must be flawless.
- Housings
They protect internal components. - Connectors
These join different parts of the device. - Switches
They require precise dimensions to function. - Casings
They provide structure and aesthetics.
Each mold must meet exact standards. This ensures parts fit and perform well.
Material Selection
Electronics require specific plastics. The injection mould company must offer options.
- ABS
It provides strength and flexibility. - Polycarbonate
This offers impact resistance. - Liquid Crystal Polymer (LCP)
This resists high temperatures. - Conductive Plastics
These manage static electricity.
The right material depends on the part’s function.
Precision in Injection Molding
Precision ensures part reliability. Electronics need tight tolerances.
Advanced machines achieve this. They maintain consistency across production.
Skilled staff monitor the process. They ensure every part meets specifications.
Quality Assurance
Quality is non-negotiable. The injection mould company must guarantee it.
- Inspection
Every part is checked for defects. - Testing
Parts are tested for strength and function. - Documentation
Processes are recorded for traceability. - Compliance
Parts must meet industry standards.
This ensures reliable parts for electronics.
Fast Turnaround Times
Electronics markets move quickly. Companies must deliver on time.
An experienced injection mould company meets deadlines. They optimize production for speed.
This prevents delays in product launches.
Cost Considerations
Cost matters in manufacturing. The right company balances quality and cost.
Efficient production reduces waste. This lowers overall costs.
Durable injection molds reduce maintenance expenses.
The Importance of Prototypes
Prototyping ensures designs work. The injection mould company must offer this service.
Prototypes test part functionality. They identify design flaws early.
This saves time and money in the long run.
Choosing the Right Partner
Not all companies fit electronics needs. Select one with proven expertise.
Check their portfolio. Look for past electronics projects.
Read reviews and client testimonials. They reveal the company’s reliability.
Case Studies in Electronics Manufacturing
- Smartphone Housings
These require precise molds for sleek designs. - Wearable Devices
Parts must be lightweight and durable. - Automotive Electronics
Connectors need high heat resistance. - Consumer Gadgets
Casings must combine aesthetics and functionality.
These examples show the role of a good injection mould company.
The Future of Electronics Injection Molding
Technology is advancing. Electronics are getting smaller and smarter.
Injection molding is adapting too. Companies now use automation and AI.
This improves precision and speed. It also reduces errors.
Electronics demand perfection. The right injection mould company ensures this.
They combine skilled mold makers, advanced machines, and strict quality checks.
Choose a partner with proven expertise. They deliver reliable injection molds on time.
Trust the experts for your next electronics project.