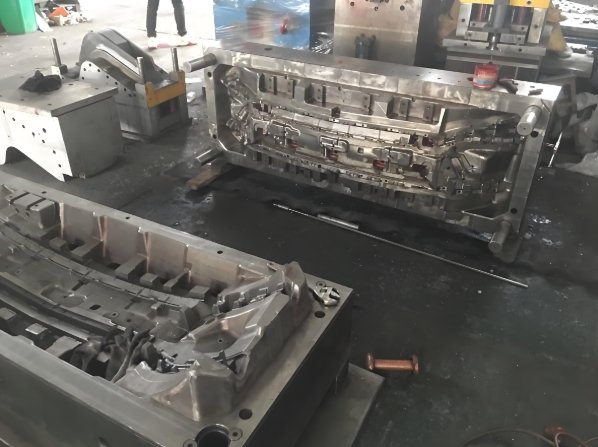
The automotive industry relies on precision. High-quality Automotive Injection Molds ensure that every part fits perfectly. From concept to production, the process involves detailed planning. A skilled Mold Maker plays a key role in this journey.
What Is Automotive Injection Molding?
Injection molding is a manufacturing process. It uses molds to shape plastic parts. Automotive Injection Molds create dashboards, panels, and other components. A Mold Maker designs molds to match exact specifications.
The Concept Phase
1. Understanding Requirements
Every project starts with requirements. Designers analyze the needed part. They consider size, material, and purpose.
2. Collaborating with Experts
Designers and engineers work together. A Mold Maker provides insights. Their input ensures the mold will work effectively.
3. Using CAD Software
Designers create digital models. These show every detail of the part. Advanced CAD tools help achieve precision.
Prototyping
1. 3D Printing
Prototypes are created using 3D printers. This step tests the design before production.
2. Refining the Design
Prototypes reveal design flaws. Engineers make improvements.
3. Collaboration with the Mold Maker
The Mold Maker ensures the mold can handle production. They check for material compatibility and strength.
Mold Making
1. Material Selection
Mold materials must be durable. Steel and aluminum are common choices.
2. Machining the Mold
CNC machines create the mold. They follow the digital design precisely.
3. Polishing and Testing
Molds are polished for a smooth finish. Tests ensure the mold works perfectly.
Production
1. Injection Process
Plastic is melted and injected into the mold. The material takes the mold’s shape.
2. Cooling and Ejecting
The part cools inside the mold. Once hardened, it is ejected.
3. Quality Checks
Every part undergoes strict quality control. This ensures no defects.
The Role of a Skilled Mold Maker
1. Expertise in Design
The Mold Maker creates molds that meet exact specifications.
2. Problem Solving
They address challenges like material compatibility.
3. Ensuring Longevity
High-quality molds last for years. The Mold Maker ensures durability.
Common Automotive Parts Made with Injection Molds
1. Bumpers
Large, durable bumpers are created using molds.
2. Dashboards
Complex dashboards require precise mold designs.
3. Door Panels
Door panels must fit perfectly. Injection molds achieve this.
4. Engine Covers
These parts need strength and precision.
Benefits of Automotive Injection Molding
1. High Precision
Molds create parts with exact dimensions.
2. Cost Efficiency
Once created, molds produce thousands of parts.
3. Speed
The injection process is fast. This reduces production time.
4. Consistency
Every part is identical.
5. Versatility
Molds can handle complex designs.
Challenges in Automotive Injection Molding
1. Design Complexity
Some parts have intricate details. Creating molds for these is difficult.
2. Material Selection
Molds must work with various plastics.
3. Initial Costs
Creating molds is expensive. However, they save money in the long run.
Innovations in Automotive Injection Molding
1. Sustainable Materials
Recyclable plastics are gaining popularity.
2. Smart Molds
Sensors in molds monitor the injection process.
3. 3D Printed Molds
These offer faster production for small runs.
How to Choose the Right Mold Maker
1. Experience
Look for a Mold Maker with industry experience.
2. Technology
They should use advanced tools for precision.
3. Support
Good customer support ensures smooth collaboration.
The journey from concept to production is complex. High-quality Automotive Injection Molds are essential for precision and efficiency. A skilled Mold Maker ensures the process is seamless.
Investing in the right molds and experts leads to success. With constant innovation, injection molding continues to transform the automotive industry.