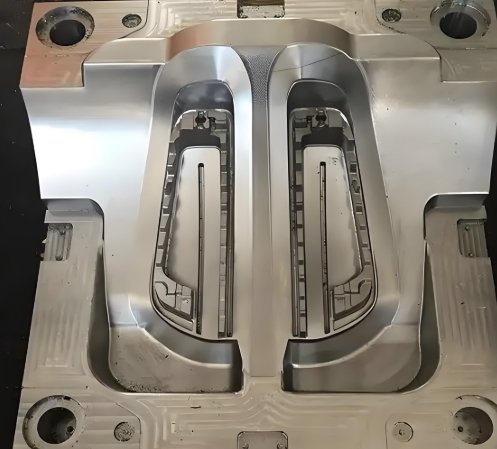
Vehicle aerodynamics is vital for performance. Smooth airflow reduces drag and improves efficiency. Automotive Injection Molds make aerodynamic designs possible. Skilled Mold Makers create precise molds for complex shapes. This ensures efficiency, speed, and sustainability.
The Role of Aerodynamics in Modern Vehicles
1. Fuel Efficiency
Aerodynamic designs reduce air resistance. This lowers fuel consumption.
2. Enhanced Performance
Better airflow improves speed and stability.
3. Environmental Impact
Efficient designs cut emissions.
How Automotive Injection Molds Shape Aerodynamics
1. Precision Components
Molds create parts with exact dimensions. This ensures a seamless design.
2. Lightweight Solutions
Plastic parts reduce overall weight. This complements aerodynamic designs.
3. Complex Shapes
Advanced molds handle intricate designs. This includes grilles, spoilers, and underbody panels.
Key Components Improved with Automotive Injection Molds
1. Bumpers
Molded bumpers streamline airflow around the vehicle.
2. Grilles
Precision molds create grilles that balance airflow and cooling.
3. Side Mirrors
Molded mirrors reduce drag while maintaining visibility.
4. Spoilers
Injection-molded spoilers enhance stability at high speeds.
5. Underbody Panels
These panels manage airflow beneath the car.
The Mold Maker‘s Role in Aerodynamics
1. Custom Designs
Every vehicle has unique needs. Mold Makers design molds to fit specific aerodynamic goals.
2. Material Selection
Choosing the right plastic is crucial. Materials must be durable and lightweight.
3. High Precision
Accurate molds ensure aerodynamic performance.
4. Problem Solving
Mold Makers address design challenges effectively.
Materials for Aerodynamic Parts
1. ABS Plastic
Strong and durable. Ideal for exterior components.
2. Polycarbonate
Lightweight and impact-resistant. Used for grilles and spoilers.
3. Nylon
Heat-resistant and strong. Great for underbody panels.
4. Polypropylene
Flexible and lightweight. Perfect for bumpers.
Steps in the Injection Molding Process
1. Design Phase
Engineers create detailed designs.
2. Material Selection
Plastics are chosen based on the part’s function.
3. Mold Fabrication
Skilled Mold Makers craft precise molds.
4. Injection Process
Molten plastic is injected into the mold.
5. Cooling and Finishing
The plastic solidifies, and finishing touches are applied.
Benefits of Injection Molding for Aerodynamics
1. Cost Efficiency
Mass production reduces manufacturing costs.
2. Design Flexibility
Molds allow for complex and innovative shapes.
3. High Strength-to-Weight Ratio
Parts are lightweight but durable.
4. Consistency
Molds produce identical parts every time.
Challenges in Aerodynamic Molding
1. Complex Designs
Aerodynamic parts require intricate shapes.
2. Material Limitations
Not all plastics meet aerodynamic needs.
3. Precision Demands
Even small errors can impact performance.
Innovations in Aerodynamic Molding
1. 3D Printing for Prototypes
Speeds up the design and testing phase.
2. Smart Molds
Incorporates sensors for real-time monitoring.
3. Eco-Friendly Practices
Focus on recycled and bio-based materials.
Applications Beyond Aerodynamics
1. Interior Components
Injection molds create dashboards and panels.
2. Structural Parts
Lightweight parts improve overall vehicle performance.
3. Lighting Systems
Headlight and taillight housings benefit from precision molds.
Sustainability in Injection Molding
1. Energy Efficiency
Modern machines use less energy.
2. Waste Reduction
Injection molding generates minimal waste.
3. Recycled Plastics
More manufacturers use eco-friendly materials.
Future Trends
1. Advanced Materials
New plastics improve strength and sustainability.
2. Automation
Streamlines production and reduces errors.
3. Data Integration
Real-time monitoring enhances precision.
Aerodynamics is key to modern vehicles. Automotive Injection Molds make it possible. Skilled Mold Makers design and craft molds for precise, efficient parts. These molds shape the future of automotive innovation. With advancements in materials and techniques, the possibilities are endless. For aerodynamic excellence, injection molds are indispensable.