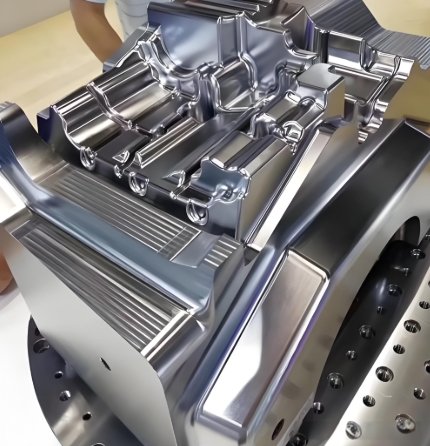
The automotive industry demands precision. Automotive Injection Molds play a critical role. These molds shape essential vehicle components. Skilled Mold Makers ensure every mold delivers quality. Innovation in mold design drives efficiency and performance.
The Importance of Automotive Injection Molds
1. Shaping the Industry
Injection molds create complex vehicle parts. They define quality and precision in production.
2. Ensuring Durability
Automotive components must withstand wear. Molds ensure strength in every part.
3. Reducing Costs
High-quality molds improve manufacturing efficiency. This reduces production expenses.
Key Features of Modern Automotive Injection Molds
1. Precision Engineering
Molds create parts with exact dimensions. Skilled Mold Makers use advanced tools.
2. Efficient Cooling Systems
Cooling channels improve cycle times. Faster cycles mean higher productivity.
3. Custom Designs
Every mold meets specific vehicle needs. This ensures compatibility and functionality.
4. Durable Materials
High-strength metals enhance mold life. They resist wear and ensure reliability.
The Role of the Mold Maker
1. Design Expertise
Mold Makers craft designs for efficiency. They combine innovation with practicality.
2. Material Selection
The right material ensures durability. Steel and aluminum are common choices.
3. Precision Manufacturing
Every detail matters in mold creation. Advanced machines ensure perfect results.
4. Continuous Improvement
Feedback helps refine mold performance. Mold Makers adapt to industry changes.
Types of Components Made with Injection Molds
1. Interior Panels
Molds create dashboards and door trims.
2. Engine Parts
Covers, housings, and mounts need precision.
3. Lighting Systems
Molds shape lenses and protective covers.
4. Exterior Features
Bumpers, grilles, and fenders require durability.
Challenges in Automotive Injection Mold Design
1. Complex Geometries
Vehicle parts have intricate designs. Molds must match every detail.
2. Material Compatibility
Molds must work with various plastics.
3. High Production Volumes
Durable molds handle repeated use.
4. Strict Standards
Automotive components must meet safety regulations.
Innovations in Mold Design
1. 3D Modeling
Digital tools improve design accuracy.
2. Advanced Materials
New alloys enhance mold strength.
3. Smart Monitoring Systems
Sensors track mold performance in real-time.
4. Sustainable Practices
Recycled materials reduce environmental impact.
Benefits of High-Quality Automotive Injection Molds
1. Consistent Quality
Precision molds ensure reliable components.
2. Cost Efficiency
Durable molds save money on replacements.
3. Faster Production
Efficient designs speed up manufacturing.
4. Reduced Waste
Better molds mean fewer rejected parts.
Steps in Creating an Injection Mold
1. Concept Development
Understand the part’s purpose and design.
2. Material Selection
Choose the best material for the mold.
3. Prototyping
Create and test a prototype mold.
4. Final Manufacturing
Use advanced machines for precision.
5. Testing and Validation
Ensure the mold meets all requirements.
Future Trends in Automotive Injection Molds
1. AI-Driven Design
Artificial intelligence enhances mold accuracy.
2. Sustainable Materials
Biodegradable plastics are gaining traction.
3. Robotic Assistance
Robots streamline mold manufacturing.
4. Smart Mold Systems
Embedded sensors monitor mold health.
Applications of Injection Molds in Automobiles
1. Safety Systems
Molds shape airbags and seatbelt components.
2. Electrical Systems
Battery housings and connectors rely on molds.
3. Fuel Systems
Molds create tanks and fuel line components.
4. Aesthetic Features
Interior trims and decorative panels use molds.
Automotive Injection Molds are vital in vehicle production. Skilled Mold Makers craft them with precision. Advanced designs improve quality and efficiency. As technology advances, molds will become even more innovative. Durable, efficient molds shape the future of automotive manufacturing. Investing in quality molds ensures long-term success.