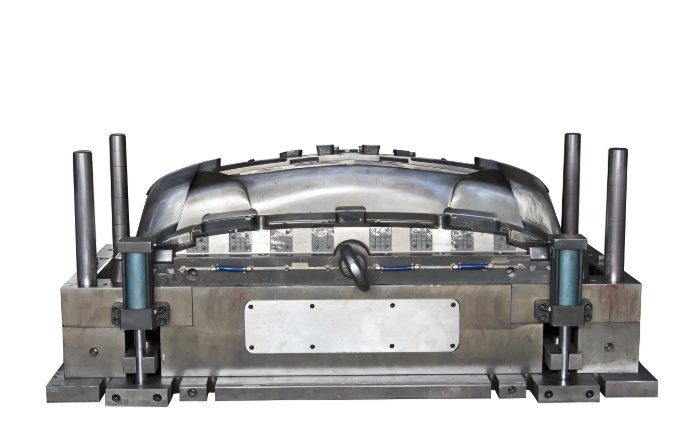
Automotive injection molds are essential for creating high-quality brake system components. Mold makers use advanced techniques to produce durable parts. These parts are crucial for vehicle safety. Each part must meet strict standards. Precision and performance are key to the success of automotive brake systems.
The Role of Injection Molding in Brake Systems
1. Importance of Brake System Components
The brake system is one of the most critical parts of any vehicle. It ensures safety by allowing drivers to stop or slow down the vehicle. Automotive injection molds are used to make several key components of the brake system. These parts must be strong, durable, and heat-resistant.
2. The Precision of Injection Molding
Mold makers create intricate parts using injection molding. These parts include brake pedal housings, master cylinders, and brake fluid reservoirs. The injection molding process ensures that every component is produced with high precision. Parts must fit together perfectly to ensure the brake system functions properly.
3. Materials Used for Brake System Components
The materials used in automotive brake system components must meet strict safety standards. Common materials include high-strength plastics and composites. These materials must withstand high temperatures and stress during braking. Mold makers select materials that balance strength, durability, and weight.
Key Applications of Injection Molds in Brake Systems
1. Brake Pedal Housings
Brake pedal housings are critical components of the brake system. These parts must be strong enough to handle the force exerted by the driver’s foot. Injection molding allows mold makers to create precise and durable pedal housings. The process ensures that the housing can withstand repeated pressure and wear.
2. Master Cylinders
The master cylinder is responsible for generating hydraulic pressure in the brake system. Automotive injection molds are used to create the housing for the master cylinder. The material used in the housing must be resistant to high pressures and temperatures. Mold makers carefully design these components to ensure safety and functionality.
3. Brake Fluid Reservoirs
Brake fluid reservoirs hold the hydraulic fluid needed for the brake system to function. These reservoirs must be leak-proof and capable of withstanding high temperatures. Mold makers use injection molding to create precise, reliable reservoirs that meet safety standards. The process ensures that the reservoir is both durable and functional.
4. ABS (Anti-lock Braking System) Components
ABS is an important safety feature in modern vehicles. It prevents the wheels from locking up during braking. Several components of the ABS system, such as sensors and control units, are made using automotive injection molds. These parts must be highly reliable and resistant to vibration, heat, and moisture. Mold makers create these components with the highest standards of quality.
5. Brake Calipers
Brake calipers are responsible for clamping down on the brake discs to slow or stop the vehicle. Injection molding is used to produce parts of the brake caliper. These parts must be made from materials that can handle high temperatures and stress. Mold makers ensure that the components are made with precision to guarantee effective braking.
6. Brake Rotor Components
Brake rotors are another crucial part of the braking system. Mold makers create brake rotor components using injection molding techniques. The precision and strength of these components ensure that the brake system performs well under high temperatures and pressure.
7. Brake Shoes
Brake shoes are used in drum brakes, a type of braking system. These parts are made using high-strength plastic materials. Mold makers use injection molding to ensure that the brake shoes have the correct shape and strength to perform effectively.
Benefits of Using Injection Molding in Brake Systems
1. High Precision and Accuracy
Injection molding provides high precision, which is essential for brake system components. Each part must be made with tight tolerances to ensure it functions properly. Mold makers use advanced technology to ensure that every part fits together perfectly.
2. Improved Durability
Brake components must be able to withstand high pressures, heat, and stress. Automotive injection molds are made from materials that can handle these extreme conditions. Mold makers select materials that offer durability, ensuring that the brake system performs reliably over time.
3. Cost-Effectiveness
Injection molding is a cost-effective method for producing brake system components. The process reduces waste and allows for efficient production. Once the mold is designed, it can be used to create large quantities of parts at a lower cost. Mold makers can produce high-quality parts without driving up the cost.
4. Design Flexibility
Injection molding allows for the creation of complex parts with intricate designs. Mold makers can design brake system components with features that would be difficult to achieve using other manufacturing methods. This design flexibility helps improve the functionality and performance of the brake system.
5. Faster Production Times
Once the mold is created, injection molding can produce parts quickly. This is important in the automotive industry, where speed is critical. Mold makers can create multiple components in a short period, helping manufacturers meet production deadlines.
6. Reduced Waste
Injection molding is a highly efficient process that minimizes waste. Materials are injected into the mold, and any excess material can be recycled for future use. This makes the process environmentally friendly and helps reduce costs.
Challenges of Using Injection Molding for Brake Systems
1. High Initial Costs
The cost of creating molds for brake system components can be high. However, the investment is worthwhile in the long run, as injection molding allows for the efficient production of high-quality parts.
2. Material Compatibility
Brake components must be made from materials that can handle extreme conditions. Mold makers must carefully select materials that meet the required performance standards for each brake system component. In some cases, finding the right material can be challenging.
3. Complexity in Design
Brake system components often have complex designs. Mold makers must ensure that the design is feasible and can be produced using injection molding. This requires a deep understanding of both the molding process and the functional requirements of the parts.
Injection molding is a vital technology in the production of automotive brake system components. Automotive injection molds are used to create a variety of parts, from brake pedal housings to ABS components. Mold makers play a crucial role in ensuring the precision, durability, and performance of these parts. With the benefits of high precision, cost-effectiveness, and design flexibility, injection molding continues to be an essential method in automotive manufacturing. As vehicle safety standards evolve, the role of mold makers will become even more important in shaping the future of brake system production.