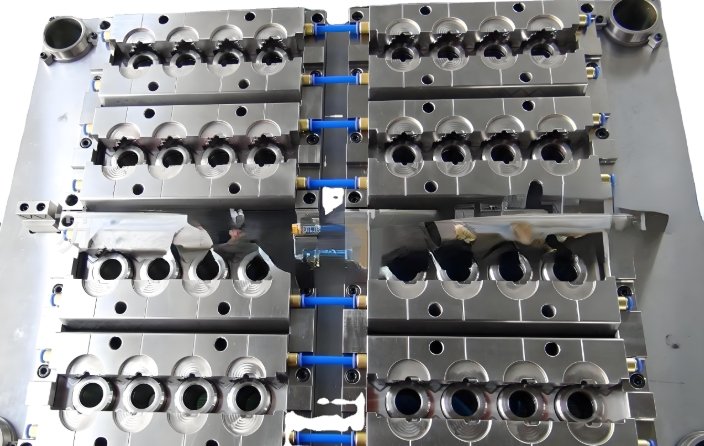
Medical devices need precision. Medical injection molding ensures accuracy, quality, and efficiency. A skilled mold maker creates high-precision molds. The process moves from design to production smoothly. This article explains the journey.
1. Understanding Medical Injection Molding
What is Medical Injection Molding?
It is a manufacturing process for medical components. Plastic is melted and injected into a mold. The part solidifies and is ejected.
Why It Matters
Healthcare demands precision. Even small errors can cause failure. Injection molding ensures consistency.
Common Medical Parts Made
- Surgical tools
- IV components
- Syringes
- Implantable devices
- Drug delivery systems
2. The Role of a Mold Maker in Medical Injection Molding
Designing High-Precision Molds
A mold maker creates detailed molds. The design must be perfect.
Material Selection
Medical-grade plastics must be safe. Biocompatibility is crucial.
Ensuring Tight Tolerances
Every part must be identical. High precision reduces errors.
Long Mold Life
A durable mold lasts through many cycles. It ensures cost efficiency.
3. Steps from Concept to Production
Step 1: Product Design
Medical engineers create the design. It must meet regulations.
Step 2: Prototype Development
A test mold is made. The first parts are checked.
Step 3: Mold Fabrication
A mold maker creates the production mold. It is built for high-volume use.
Step 4: Injection Molding Process
Plastic is heated and injected. It fills the mold cavity. The part cools and solidifies.
Step 5: Quality Inspection
Every part is checked. Accuracy is verified.
Step 6: Mass Production
Once approved, large-scale manufacturing begins.
4. Key Materials in Medical Injection Molding
Biocompatible Plastics
- Polycarbonate (PC) – Strong and impact-resistant
- Polypropylene (PP) – Lightweight and durable
- PEEK – High heat resistance
Silicone Rubber
Used in flexible medical devices. Soft and biocompatible.
Resorbable Polymers
Used in implants that dissolve in the body.
5. Cleanroom Manufacturing for Medical Parts
Why Cleanrooms Matter
Medical parts must be sterile. Contamination risks patient safety.
Types of Cleanrooms
- ISO Class 7 – Used for most medical devices
- ISO Class 8 – Used for less sensitive parts
Strict Manufacturing Protocols
Workers wear protective gear. Machines are sanitized regularly.
6. Quality Control in Medical Injection Molding
Inspection Techniques
- Visual Inspection – Checks surface defects
- Automated Scanning – Detects tiny errors
- Dimensional Testing – Measures accuracy
Regulatory Compliance
- FDA Regulations – Ensures patient safety
- ISO 13485 Certification – Guarantees quality standards
- Good Manufacturing Practices (GMP) – Maintains consistency
7. Specialized Injection Molding Techniques
Micro-Molding
Used for extremely small parts. Essential for minimally invasive surgery.
Overmolding
Combines multiple materials in one part. Improves grip and durability.
Insert Molding
Encapsulates metal parts in plastic. Used for medical device components.
8. Scaling from Prototype to Mass Production
Challenges in Scaling Up
- Ensuring product consistency
- Meeting high production demands
- Maintaining regulatory compliance
How a Skilled Mold Maker Helps
A mold maker designs efficient molds. The process runs smoothly at high volumes.
9. Reducing Errors in Medical Injection Molding
Strict Quality Checks
Every batch is tested. Any defect is eliminated.
Advanced Sensor Technology
Machines detect small defects. This reduces waste.
Regular Mold Maintenance
A well-maintained mold lasts longer. It prevents production delays.
10. Future Innovations in Medical Injection Molding
Smart Medical Devices
Wearable technology requires micro-molding. Improves patient monitoring.
Sustainable Medical Plastics
Eco-friendly materials reduce waste. More biodegradable options emerge.
AI in Quality Control
Automated defect detection improves efficiency. Reduces errors to near zero.
11. Choosing the Right Medical Injection Molding Partner
Experience in Medical Molding
Look for proven expertise. Years of experience matter.
Regulatory Compliance
Certified manufacturers follow strict guidelines.
Production Capacity
A strong partner handles high-volume orders.
Prototyping Services
Early testing ensures better final products.
Transparent Communication
Clear updates prevent production delays.
Medical injection molding is essential in healthcare. A skilled mold maker ensures accuracy and safety. The process moves from concept to mass production seamlessly. Quality control guarantees precision. Choosing the right manufacturing partner ensures success.