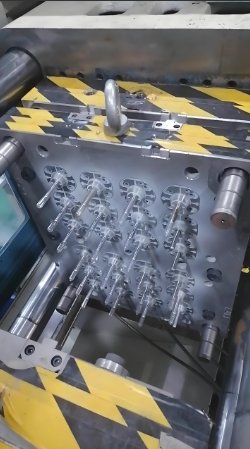
Medical devices require high standards. Medical injection molding plays a crucial role. The choice of material matters a lot. Medical-grade plastics ensure safety and durability. A skilled mold maker chooses the best plastics for each device.
1. What is Medical-Grade Plastic?
Understanding Medical-Grade Plastics
Medical-grade plastics are specially designed for healthcare applications. They meet strict safety and quality standards. These plastics are non-toxic, durable, and resistant to damage.
Types of Medical-Grade Plastics
- Polycarbonate (PC)
- Polypropylene (PP)
- Polyethylene (PE)
- Acrylonitrile Butadiene Styrene (ABS)
- Polyether Ether Ketone (PEEK)
- Silicone
2. Why Quality Matters in Medical Injection Molding
Ensuring Patient Safety
The primary concern in medical devices is safety. Medical injection molding uses high-quality plastics that do not leach harmful substances into the body.
Regulatory Compliance
Medical plastics must meet strict regulations. The FDA and ISO standards are crucial. Compliance guarantees the safety and effectiveness of medical devices.
3. The Role of a Mold Maker in Material Selection
Precision in Mold Design
A skilled mold maker ensures the right material choice. They ensure precision in creating molds for medical parts. This precision affects the performance of the final device.
Customizing for Functionality
Different medical devices require different plastic properties. A mold maker customizes the material based on the device’s function.
4. Advantages of Medical-Grade Plastics in Injection Molding
Biocompatibility
Medical-grade plastics are safe for human contact. They do not cause reactions or toxicity.
Durability
Medical plastics are resistant to wear and tear. They last longer, even under stress and repeated use.
Sterilization Compatibility
Plastics used in medical devices must withstand sterilization. High-quality plastics resist heat, chemicals, and radiation during sterilization.
Chemical Resistance
Medical-grade plastics can endure exposure to harsh chemicals. This is essential for devices used in laboratories or hospitals.
Flexibility and Strength
Some medical devices need both strength and flexibility. Medical-grade plastics are designed to balance these properties.
5. Examples of Medical Devices Using Medical-Grade Plastics
Syringes and Needles
Syringes use polypropylene or polyethylene. These plastics are lightweight and chemical-resistant.
Implants
PEEK is commonly used for implants. It is biocompatible and durable, making it perfect for long-term use.
Catheters
Silicone is flexible, making it ideal for catheters. It is biocompatible and can be sterilized without degrading.
Injection Molds for Diagnostic Devices
Devices like test tubes and petri dishes use medical-grade plastics. These materials ensure reliability and resistance to chemicals.
6. Medical Injection Molding Process
Injection Molding Overview
Medical injection molding uses high-quality plastics to create precise parts. The material is heated, injected into molds, and then cooled to form the part.
Steps in the Process
- Material Selection – A mold maker chooses the best plastic for the device.
- Mold Design – The mold is precisely designed for the medical device.
- Injection – The material is injected into the mold.
- Cooling – The part cools and hardens.
- Finishing – The part is cleaned, inspected, and prepared for use.
7. The Role of Sterilization in Medical Plastics
Sterilization Methods
Medical devices often undergo sterilization. Plastics must endure various methods, such as:
- Autoclaving – High-pressure steam.
- Gamma Radiation – Used for devices that cannot tolerate heat.
- Ethylene Oxide (EtO) – Chemical sterilization.
Choosing Sterilization-Compatible Plastics
The right plastic ensures the device remains intact during sterilization. For instance, polycarbonate and polypropylene are good choices for heat and chemical resistance.
8. Challenges in Medical-Grade Plastics for Injection Molding
Strict Regulatory Requirements
Meeting the regulatory standards can be challenging. A mold maker must ensure that the material used complies with industry standards.
Ensuring Consistency
Medical devices need to be precise. A slight variation in the molding process can lead to defects. Ensuring consistency in injection molding is vital for the device’s safety and performance.
Material Availability and Cost
Some medical-grade plastics can be expensive or hard to source. A mold maker must balance cost and availability with the quality required for medical devices.
9. Future of Medical-Grade Plastics in Injection Molding
Innovative Plastics
New medical-grade plastics are emerging. These materials offer improved properties, such as enhanced biocompatibility and better resistance to sterilization.
Sustainability in Materials
There is a growing trend towards using sustainable, eco-friendly plastics in medical devices. This includes biodegradable materials and recyclable plastics.
Smart Materials
The future of medical injection molding may include smart materials. These materials change properties based on temperature or pressure. They can be used in devices that respond to body conditions.
Medical injection molding is a crucial process in producing high-quality medical devices. Medical-grade plastics ensure safety, performance, and durability. A skilled mold maker ensures that the right material is selected for each device. From biocompatibility to durability and sterilization compatibility, the right plastic makes all the difference in healthcare.