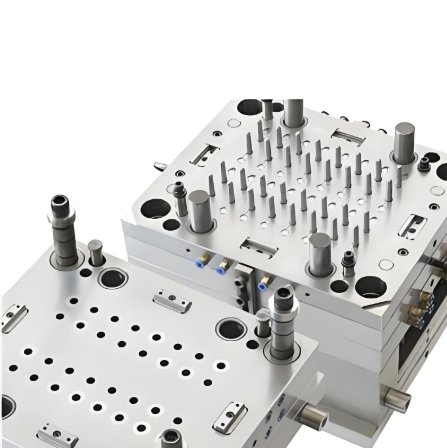
Material selection is a crucial step in medical injection molding. The right material ensures safety, durability, and compliance with regulations. A skilled mold maker plays a key role in selecting the best material for each application. This decision impacts the performance and reliability of medical devices.
1. The Role of Materials in Medical Devices
Materials determine the device’s function. They affect how it performs in the body. The right material can improve device longevity and safety. The wrong material can cause failure or complications.
2. Factors That Influence Material Selection
1. Biocompatibility
Medical devices often come into contact with human tissues. Materials must be biocompatible to avoid reactions. Biocompatibility ensures the device does not cause harm. It is a critical factor in medical injection molding.
2. Durability
Medical devices need to last. Materials must be strong and resistant to wear and tear. They must withstand repeated sterilization and use. A mold maker ensures the right material is selected for durability.
3. Chemical Resistance
Medical devices come into contact with drugs, chemicals, and disinfectants. The material must resist these chemicals. If a material breaks down under chemical exposure, it can affect the device’s performance.
4. Sterilization Compatibility
Medical devices are sterilized before use. The material must withstand sterilization methods, such as autoclaving or gamma radiation. Some materials degrade under heat or radiation. A mold maker carefully selects materials based on their sterilization compatibility.
5. Mechanical Properties
Medical devices often undergo stress and strain. The material must have the right balance of strength, flexibility, and impact resistance. Strong materials ensure the device remains functional over time.
6. Regulatory Compliance
Medical devices must meet strict standards. Materials need to comply with FDA, ISO, and other regulatory requirements. Compliance ensures safety and effectiveness.
3. Common Materials Used in Medical Injection Molding
1. Polypropylene (PP)
Polypropylene is commonly used for medical applications. It is lightweight, durable, and resistant to chemicals. It is often used in medical containers, syringes, and packaging.
2. Polyethylene (PE)
Polyethylene is another popular material for medical devices. It is flexible and resistant to chemicals. It is often used for medical tubing and packaging.
3. Polycarbonate (PC)
Polycarbonate is strong and impact-resistant. It is used in devices that require transparency, like diagnostic equipment and surgical instruments.
4. Polyetheretherketone (PEEK)
PEEK is a high-performance polymer. It is used in implants and surgical instruments. It is biocompatible, strong, and resistant to high temperatures.
5. Medical-Grade Silicone
Silicone is flexible and biocompatible. It is commonly used in implants, seals, and gaskets. It can also withstand extreme temperatures.
6. Polylactic Acid (PLA)
PLA is a biodegradable plastic. It is used in medical devices that need to break down over time. It is environmentally friendly and is often used in tissue scaffolding and drug delivery systems.
4. How Material Selection Affects the Molding Process
1. Flowability
Some materials flow more easily than others during molding. Flowability affects the ease of molding and the quality of the final product. A mold maker must select materials that flow smoothly and evenly in the mold.
2. Shrinkage
Different materials shrink at different rates when they cool. Shrinkage can affect the size and shape of the molded part. A skilled mold maker accounts for shrinkage when designing the mold.
3. Temperature Resistance
Some materials can withstand higher temperatures than others. If the material melts or deforms at high temperatures, it can cause defects in the final product. The mold maker selects materials that match the required temperature tolerance.
4. Cycle Time
The cycle time is the time it takes to complete one molding process. Materials that set quickly help reduce cycle time. Materials that take longer to cool may increase cycle time. A mold maker selects materials that optimize the molding process for efficiency.
5. The Impact of Material Selection on Device Performance
1. Safety
Safety is the top priority in medical devices. The wrong material can lead to device failure or harm to the patient. Materials must meet rigorous safety standards and be thoroughly tested.
2. Functionality
The material affects how well the device works. A material with the right properties ensures the device functions as intended.
3. Cost
Material choice also impacts cost. High-performance materials may be more expensive. However, they can reduce the need for repairs and replacements, ultimately saving costs in the long run. A mold maker helps balance cost and performance.
6. Common Challenges in Material Selection
1. Cost Constraints
High-quality medical materials can be expensive. However, cutting costs by selecting lower-quality materials can jeopardize the safety and effectiveness of the device.
2. Supply Chain Issues
Some materials are hard to source or have long lead times. A mold maker must plan ahead to avoid delays in production.
3. Regulatory Hurdles
Materials must meet stringent regulatory standards. Gaining approval for new materials can be time-consuming and costly.
4. Compatibility with Existing Equipment
Some materials require specific injection molding equipment. A mold maker must ensure that the chosen material is compatible with the available equipment.
7. Future Trends in Medical Injection Molding Materials
1. Biodegradable Materials
There is growing interest in biodegradable materials for medical devices. These materials can reduce medical waste and improve sustainability.
2. Smart Polymers
Smart polymers are materials that change their properties in response to external stimuli. These materials have great potential in medical devices.
3. Advanced Coatings
Some materials can be coated to improve properties like biocompatibility, wear resistance, or antimicrobial activity.
Material selection is a critical factor in medical injection molding. It affects the device’s performance, safety, and compliance with regulations. A skilled mold maker carefully selects the right materials for each device, ensuring that it functions as intended. Choosing the best material is key to producing high-quality, reliable medical devices.