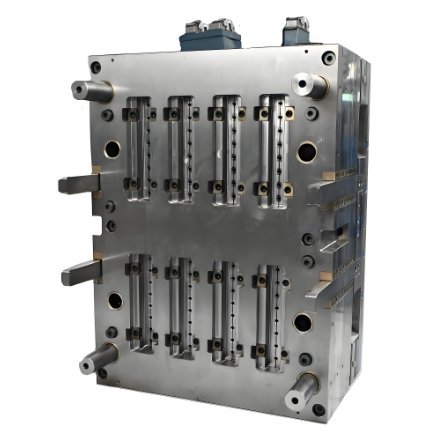
ISO 13485 is a crucial standard for medical device manufacturing. It ensures that manufacturers meet strict quality requirements. For medical injection molding, it is essential for producing reliable, high-quality products. Mold makers play a key role in this process. This article explains how ISO 13485 affects medical injection molding and what mold makers need to do to comply.
What is ISO 13485?
1. Overview of ISO 13485
ISO 13485 is an international standard. It sets the requirements for a quality management system (QMS) specific to the medical device industry. It helps ensure that medical devices and related services are consistently safe and effective.
2. Importance for Medical Injection Molding
Medical injection molding involves creating critical components for devices like syringes, implants, and diagnostic equipment. To guarantee these parts meet safety standards, manufacturers must comply with ISO 13485.
3. Relationship to Compliance
ISO 13485 certification proves that a company follows regulations and delivers products that meet medical standards. This standard is mandatory in many markets, including Europe and the U.S., for manufacturers of medical devices.
ISO 13485 Requirements for Medical Injection Molding
1. Risk Management
ISO 13485 requires that manufacturers identify, assess, and manage risks throughout the production process. For medical injection molding, this includes identifying potential risks like material contamination or mold defects that could affect product quality.
2. Documentation Control
Proper documentation is crucial. Mold makers must keep detailed records of each batch produced. These records help track material sources, production processes, and testing results. This ensures traceability and accountability.
3. Design Controls
Mold makers must ensure that the designs used in injection molding are properly controlled. This includes reviewing designs for manufacturability and verifying that they meet medical requirements. The molding process itself must be designed to prevent defects and ensure the finished product performs as intended.
4. Supplier Management
ISO 13485 also emphasizes the importance of managing suppliers. Mold makers must ensure that the materials they use meet strict standards. This involves selecting suppliers who can provide certified medical-grade materials and components that are free from defects.
5. Calibration and Maintenance of Equipment
Injection molding equipment must be regularly calibrated and maintained. This is to ensure that it operates within specified parameters. Proper equipment maintenance prevents defects and ensures consistency in part production.
Benefits of ISO 13485 Certification for Mold Makers
1. Improved Quality Assurance
By adhering to ISO 13485, mold makers can ensure that every product meets the highest standards of quality. This leads to fewer defects, better product performance, and increased customer satisfaction.
2. Enhanced Market Access
ISO 13485 certification is required for selling medical devices in many global markets. Being certified allows mold makers to access new markets and work with a broader range of clients in the medical industry.
3. Risk Mitigation
By following ISO 13485 guidelines, mold makers can better manage risks. They can identify potential issues before they occur and take corrective action, which reduces the chance of costly recalls or product failures.
4. Streamlined Processes
Implementing ISO 13485 helps mold makers establish efficient processes. With clear procedures and documentation, the workflow becomes more organized and consistent. This leads to faster production times and fewer errors.
5. Competitive Advantage
Companies with ISO 13485 certification are often seen as more trustworthy and reliable. This provides a competitive edge in the medical device market. Mold makers can differentiate themselves by showcasing their ability to produce high-quality, compliant products.
How Mold Makers Can Ensure ISO 13485 Compliance
1. Develop a Quality Management System (QMS)
To meet ISO 13485, mold makers must establish a QMS that aligns with the standard. This system includes defining processes, responsibilities, and procedures for product development, testing, and production.
2. Implement Thorough Testing Procedures
Testing is a critical aspect of ISO 13485 compliance. Mold makers must perform various tests to ensure that the injection-molded components meet safety, durability, and performance standards. These tests may include material testing, dimensional checks, and stress testing.
3. Document Everything
ISO 13485 places a heavy emphasis on documentation. Mold makers must keep accurate and up-to-date records for every production run. These records include design reviews, material certifications, quality control tests, and any corrective actions taken.
4. Conduct Regular Internal Audits
Regular internal audits are necessary to ensure ongoing compliance with ISO 13485. Mold makers should periodically assess their processes and identify areas for improvement. Audits help detect any gaps in the system that could lead to non-compliance.
5. Train Employees on Compliance
Employee training is essential for ISO 13485 compliance. All staff involved in the injection molding process, from design to production, must understand the requirements of the standard. This ensures that everyone is following the right procedures and maintaining quality.
6. Work with Certified Suppliers
To meet ISO 13485, mold makers must work with certified suppliers. All raw materials, components, and subassemblies must meet the standard’s requirements. Mold makers should carefully vet suppliers to ensure they provide high-quality, compliant materials.
Challenges of ISO 13485 Compliance for Mold Makers
1. Cost of Certification
The process of obtaining ISO 13485 certification can be expensive. It involves training, audits, and process changes, which can be costly for smaller mold makers. However, the long-term benefits, such as access to new markets and improved quality, outweigh the initial costs.
2. Ongoing Maintenance
ISO 13485 is not a one-time process. Mold makers must continually maintain their QMS to remain compliant. This involves regular audits, updates to documentation, and ongoing training for employees.
3. Complex Documentation Requirements
ISO 13485 requires extensive documentation, which can be difficult to manage. Mold makers must ensure that all records are complete, accurate, and easily accessible. This can be time-consuming but is essential for demonstrating compliance.
The Future of ISO 13485 and Medical Injection Molding
1. Advancements in Technology
As technology continues to evolve, ISO 13485 will adapt. New technologies, such as automation and AI, will help mold makers improve production efficiency and product quality. These technologies will also help with documentation and record-keeping, making compliance easier.
2. Increased Focus on Sustainability
Sustainability is becoming more important in the medical device industry. ISO 13485 may eventually incorporate more environmental standards. Mold makers will need to adopt sustainable practices, such as reducing waste and using eco-friendly materials, to remain compliant.
3. Global Standardization
ISO 13485 is already recognized worldwide, but as global markets continue to grow, standardization will become even more critical. Mold makers who are ISO 13485 certified will have a significant advantage in accessing international markets and working with global clients.
ISO 13485 plays a vital role in the medical device manufacturing process, particularly in medical injection molding. Mold makers must understand the standard’s requirements and implement practices to ensure compliance. By doing so, they can improve product quality, reduce risks, and gain a competitive edge in the medical device industry.