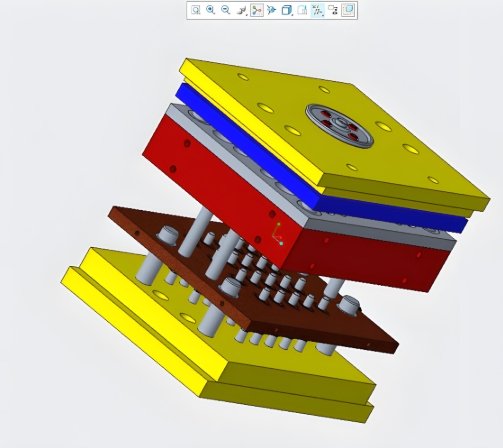
Quality is critical in medical injection molding. Medical devices must meet strict safety and performance standards. Mold makers play a vital role in ensuring precision and reliability. This article explores the key standards that govern medical injection molding and how manufacturers maintain quality.
Why Quality Matters in Medical Injection Molding
1. Patient Safety
Defective medical parts can cause serious harm. High-quality molding ensures safe and reliable devices.
2. Regulatory Compliance
Medical devices must meet FDA, ISO, and GMP standards. Failure to comply can result in recalls and legal action.
3. Consistent Performance
Medical components must function perfectly every time. Precision molding ensures consistent results.
4. Contamination Prevention
Strict hygiene controls prevent contamination in medical parts. Cleanroom manufacturing is essential for sterility.
5. Cost Efficiency
Defective parts lead to waste and high costs. High-quality production reduces defects and saves money.
Key Standards for Medical Injection Molding
1. ISO 13485: Quality Management for Medical Devices
- Ensures manufacturers follow strict quality management systems.
- Covers risk management, documentation, and process control.
- Required for medical device manufacturers worldwide.
2. FDA 21 CFR Part 820: Quality System Regulation (QSR)
- Regulates how medical devices are designed, manufactured, and tested.
- Requires proper documentation and traceability.
- Helps prevent defects and ensures safety.
3. ISO 9001: General Quality Management System
- Focuses on customer satisfaction and continuous improvement.
- Provides guidelines for process control and risk management.
4. GMP (Good Manufacturing Practices)
- Ensures that medical products are produced in a controlled environment.
- Covers personnel training, facility cleanliness, and production processes.
5. ISO 10993: Biocompatibility Testing
- Ensures materials used in medical devices are safe for human contact.
- Tests for toxicity, irritation, and long-term compatibility.
6. ISO 14644: Cleanroom Standards
- Defines air cleanliness requirements for medical manufacturing.
- Reduces contamination in sterile medical components.
How Mold Makers Ensure High-Quality Injection Molding
1. High-Precision Mold Design
- Mold makers use CAD software to design accurate molds.
- Proper mold design prevents defects and ensures consistency.
2. Material Selection
- Only medical-grade plastics are used.
- Materials must meet biocompatibility and sterilization requirements.
3. Process Validation
- Every production process is tested and validated.
- Ensures molds produce defect-free parts under real conditions.
4. Cleanroom Manufacturing
- Medical molding is performed in a controlled cleanroom environment.
- Prevents dust, bacteria, and contamination.
5. Automated Quality Inspections
- Advanced sensors detect defects during production.
- AI-driven inspections improve accuracy and reduce human errors.
Steps to Maintain Quality in Medical Injection Molding
1. Design and Prototyping
- Prototypes are tested before full production.
- Identifies potential issues early in the process.
2. Mold Fabrication and Testing
- Molds are precisely machined and tested for accuracy.
- Regular mold maintenance prevents defects.
3. Injection Molding Process Control
- Temperature, pressure, and cycle times are monitored.
- Any deviations are corrected immediately.
4. Quality Assurance and Testing
- Every batch undergoes detailed inspections.
- Functional and dimensional tests ensure compliance.
5. Documentation and Traceability
- Production data is recorded for regulatory compliance.
- Traceability helps track defects and improve processes.
Common Challenges in Ensuring Quality
1. Maintaining Tight Tolerances
- Medical parts require extreme precision.
- Minor defects can make a device unusable.
2. Material Selection Issues
- Some plastics may not meet biocompatibility requirements.
- Mold makers must carefully select FDA-approved materials.
3. Cleanroom Contamination Risks
- Even small dust particles can ruin medical components.
- Strict cleanroom protocols must be followed.
4. Regulatory Changes
- Standards and regulations evolve over time.
- Manufacturers must stay updated and adapt quickly.
5. High Production Costs
- Quality control measures add to production costs.
- Process optimization helps reduce waste and improve efficiency.
Technological Advances in Medical Injection Molding Quality Control
1. AI-Powered Defect Detection
- AI systems analyze parts in real time.
- Reduces human error and improves accuracy.
2. Advanced Material Testing
- New biocompatible plastics enhance device safety.
- Materials can now withstand harsher sterilization processes.
3. 3D Printing for Prototyping
- Allows quick testing of mold designs.
- Speeds up development and reduces costs.
4. Smart Molding Machines
- IoT-connected machines track process parameters.
- Alerts operators to potential issues before defects occur.
5. Automation in Quality Inspection
- Automated vision systems scan parts for defects.
- Ensures 100% quality control without slowing production.
Future Trends in Medical Injection Molding Quality Control
1. Greater Use of Robotics
- Robotic systems will further improve precision.
- Reduces contamination risks in cleanroom environments.
2. Smart Manufacturing Integration
- AI and data analytics will optimize production.
- Predictive maintenance will prevent mold failures.
3. Sustainable Manufacturing Practices
- More eco-friendly materials will be used.
- Recycling and waste reduction will improve efficiency.
4. Stricter Quality Regulations
- Governments will impose stricter safety standards.
- Companies will need better compliance strategies.
Ensuring quality in medical injection molding requires strict standards and advanced technologies. Mold makers play a crucial role in maintaining precision and compliance. By following ISO, FDA, and GMP guidelines, manufacturers can produce safe and reliable medical components. As technology advances, quality control will continue to improve, ensuring even better medical products in the future.