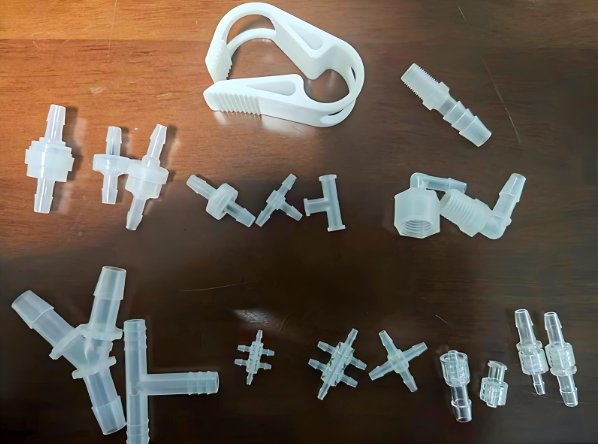
Digital twins are changing medical injection molding. These virtual models replicate physical processes, improving efficiency and precision. Mold makers use digital twins to optimize mold design, reduce defects, and predict failures. This technology enhances quality, speeds up production, and ensures compliance with strict medical regulations.
What is a Digital Twin?
1. Definition
A digital twin is a virtual replica of a physical system. It simulates real-time performance, providing insights for better decision-making.
2. How It Works
- IoT sensors collect real-time data from molding machines.
- AI analyzes performance and detects issues.
- Engineers adjust parameters to optimize production.
3. Why It’s Important
- Reduces production errors.
- Improves efficiency in medical injection molding.
- Lowers material waste and energy use.
How Digital Twins Improve Medical Injection Molding
1. Optimizing Mold Design
- Simulates how molten plastic flows inside molds.
- Detects potential defects before production.
- Ensures uniform filling and cooling.
2. Enhancing Production Efficiency
- AI adjusts molding parameters for better performance.
- Reduces cycle time without sacrificing quality.
- Ensures every batch meets strict medical standards.
3. Predicting and Preventing Mold Failures
- Monitors mold wear and tear in real time.
- Alerts mold makers before breakdowns occur.
- Extends mold lifespan, reducing downtime.
4. Improving Quality Control
- Detects tiny defects invisible to human inspectors.
- Ensures consistent part dimensions and material properties.
- Meets FDA and ISO medical manufacturing regulations.
5. Reducing Material Waste
- Predicts the exact amount of plastic needed per part.
- Minimizes scrap and rework.
- Supports sustainable manufacturing efforts.
The Role of Mold Makers in Digital Twin Implementation
1. Designing Smarter Molds
- Mold makers use digital twins to refine mold structures.
- AI-generated designs improve accuracy and durability.
2. Integrating IoT Sensors
- Sensors track mold pressure, temperature, and cycle time.
- Provides real-time feedback for process optimization.
3. Ensuring Predictive Maintenance
- AI forecasts maintenance schedules.
- Prevents unexpected failures and extends mold life.
4. Testing and Validation Before Production
- Digital twins simulate thousands of molding cycles.
- Ensures the mold performs correctly before manufacturing begins.
Challenges of Implementing Digital Twins in Medical Injection Molding
1. High Initial Costs
- Advanced software and sensors require investment.
- Long-term benefits outweigh setup expenses.
2. Integration with Existing Systems
- Older machines may not support IoT connectivity.
- Upgrading infrastructure takes time and resources.
3. Data Security Risks
- Digital twins rely on cloud-based data storage.
- Cybersecurity measures are needed to protect sensitive information.
4. Skilled Workforce Requirement
- Employees need training in AI and data analytics.
- Companies must invest in digital expertise.
Latest Innovations in Digital Twin Technology for Medical Molding
1. AI-Driven Simulation Models
- Uses deep learning to predict material behavior.
- Adjusts mold designs based on real-world performance.
2. Real-Time IoT Monitoring Systems
- Provides instant feedback on machine conditions.
- Automatically corrects process deviations.
3. Augmented Reality (AR) Integration
- Engineers can interact with digital twins using AR.
- Speeds up troubleshooting and maintenance.
4. Blockchain for Secure Data Management
- Ensures transparent record-keeping.
- Tracks every step of the medical injection molding process.
5. Cloud-Based Digital Twin Platforms
- Enables remote monitoring of production sites.
- Enhances collaboration between teams.
Future Trends in Digital Twins for Medical Injection Molding
1. Fully Autonomous Manufacturing
- AI-controlled factories will self-optimize production.
- Human intervention will be minimal.
2. Digital Twins for Personalized Medical Devices
- Simulates custom implants before production.
- Ensures precision in patient-specific molding.
3. Sustainable Digital Twin Integration
- Optimizes energy use to reduce carbon footprint.
- Supports eco-friendly materials and processes.
4. 3D Printing Combined with Digital Twins
- Enables rapid mold prototyping.
- Speeds up new medical device development.
5. Advanced Predictive Analytics
- AI will improve defect prediction.
- Enhances efficiency in high-volume production.
Digital twins are revolutionizing medical injection molding. They improve mold design, optimize production, and ensure compliance. Mold makers play a key role in integrating this technology. As digital twins evolve, they will create smarter, more efficient, and sustainable manufacturing processes.