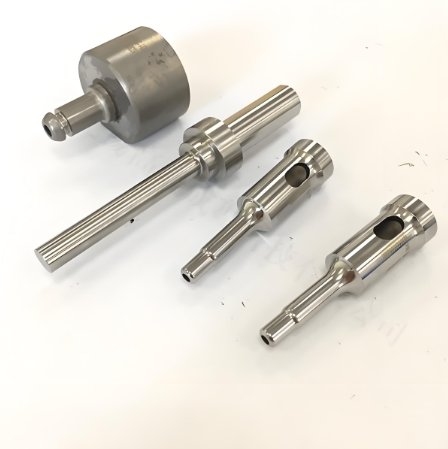
Automation is transforming medical injection molding. Advanced robotics improve precision, efficiency, and compliance. Mold makers are using robotic systems to reduce defects, cut costs, and enhance production speed. This technology ensures high-quality medical components with minimal waste.
Why Robotics Matter in Medical Injection Molding
1. Improving Precision
Robotic systems ensure consistency in every molded part. They eliminate human error and maintain strict tolerances.
2. Enhancing Speed and Efficiency
Robots work continuously without breaks. This increases production output while reducing cycle times.
3. Ensuring Sterility and Cleanroom Compliance
Automated systems minimize human contact with medical components. This reduces contamination risks in ISO 14644 cleanrooms.
4. Lowering Production Costs
Robotic automation reduces labor costs and material waste. Smart systems optimize energy use.
5. Meeting Regulatory Standards
AI-driven robots ensure compliance with FDA and ISO guidelines. They track every step of the molding process.
Types of Robotics Used in Medical Injection Molding
1. Robotic Part Handling
- Picks and places molded components with high accuracy.
- Reduces damage and contamination.
- Works at high speeds to improve efficiency.
2. Automated Quality Inspection
- Uses cameras and AI to detect defects.
- Ensures each part meets medical standards.
- Eliminates defective components before packaging.
3. Insert Molding Robots
- Precisely places metal or plastic inserts into molds.
- Improves bond strength in overmolded medical parts.
4. High-Speed Robotic Sprue Removal
- Cuts excess material from molded parts.
- Ensures clean and smooth component edges.
5. Collaborative Robots (Cobots)
- Work alongside human operators safely.
- Improve productivity in hybrid automated systems.
How Robotics Improve Efficiency in Medical Injection Molding
1. Faster Cycle Times
- Robots reduce mold opening and closing times.
- Speeds up part cooling and ejection.
2. Improved Material Handling
- Automated feeders precisely measure raw materials.
- Reduces waste and ensures uniform mixing.
3. Reduced Defects and Rework
- AI-powered robots detect defects instantly.
- Automated adjustments correct errors in real time.
4. 24/7 Continuous Production
- Robots operate around the clock without fatigue.
- Increases medical device output without extra labor costs.
5. Better Traceability and Compliance
- Robots log data for every molded component.
- Ensures full traceability for FDA and ISO audits.
The Role of Mold Makers in Robotic Integration
1. Designing Robot-Compatible Molds
- Mold makers create molds optimized for robotic handling.
- Ensures precise material flow and ejection.
2. Implementing Smart Mold Sensors
- Embedded IoT sensors track mold performance.
- Prevents defects by adjusting conditions in real time.
3. Developing Automated Tooling Systems
- Robotic end-effectors adjust for different mold designs.
- Improves flexibility in multi-product production lines.
4. Enhancing Cooling and Ejection Systems
- Mold makers design molds with efficient cooling channels.
- Robotic systems optimize part release and handling.
Challenges in Adopting Robotics for Medical Injection Molding
1. High Initial Investment
- Robotic systems require capital for setup.
- Long-term cost savings outweigh upfront expenses.
2. Workforce Training Requirements
- Employees need specialized training to manage robots.
- Hybrid workforces must adapt to automation.
3. System Integration Complexity
- Legacy equipment may not support automation.
- IoT connectivity is required for real-time monitoring.
4. Maintenance and Downtime Risks
- Robots need periodic maintenance for peak performance.
- Unplanned downtime can disrupt production schedules.
Latest Innovations in Robotic Medical Injection Molding
1. AI-Driven Robotic Inspection
- Uses deep learning to improve defect detection.
- Eliminates faulty parts before packaging.
2. Autonomous Injection Molding Cells
- Fully robotic workstations handle material loading to final packaging.
- Reduces human intervention for sterile medical production.
3. Soft Robotics for Delicate Medical Parts
- Gentle robotic grips prevent damage to fragile components.
- Ideal for micro-molded and flexible medical devices.
4. Smart Vision Systems for Real-Time Adjustments
- AI-powered cameras track molding consistency.
- Adjusts pressure, temperature, and cycle times automatically.
5. Blockchain for Secure Production Tracking
- Robotic systems log every step of the molding process.
- Ensures full transparency in medical device manufacturing.
Future Trends in Robotics for Medical Injection Molding
1. Fully Automated Smart Factories
- AI-powered robots will manage entire production plants.
- Medical injection molding will become fully autonomous.
2. 3D Printing and Robotics Integration
- Robots will assemble 3D-printed medical components.
- Hybrid manufacturing will improve customization.
3. AI-Powered Robotic Decision Making
- Machines will self-optimize based on real-time data.
- Human oversight will shift to strategic monitoring.
4. Green Robotics for Sustainable Manufacturing
- Energy-efficient robots will cut power consumption.
- Smart systems will reduce plastic waste.
5. Personalized Medical Device Production
- AI and robotics will enable patient-specific implants.
- Smart molding cells will adjust parameters for unique designs.
Advanced robotics are transforming medical injection molding. They improve precision, reduce waste, and increase efficiency. Mold makers play a vital role in designing robot-friendly molds and optimizing production. As automation evolves, robotic systems will drive the future of medical manufacturing, ensuring faster, safer, and higher-quality medical devices.