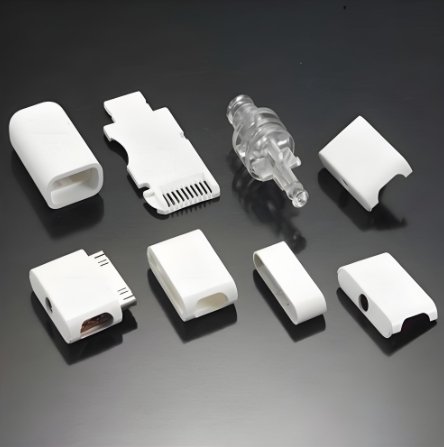
Balancing cost and quality in medical injection molding is challenging. Manufacturers must meet strict medical standards while controlling expenses. Mold makers play a crucial role in optimizing materials, automation, and process efficiency. This article explores strategies to reduce costs without compromising quality.
Why Balancing Cost and Quality is Critical
1. Strict Medical Regulations
Medical components must meet FDA and ISO standards. Compliance adds costs but ensures patient safety.
2. High Material Expenses
Medical-grade plastics are costly. Efficient use of materials reduces waste and lowers costs.
3. Need for Precision and Consistency
Medical devices require tight tolerances. Any defects can lead to failures or recalls.
4. Energy and Labor Costs
Manufacturing requires high energy consumption and skilled labor. Smart automation helps reduce expenses.
5. Market Competition
Manufacturers must keep prices low while delivering high-quality products.
Cost-Effective Material Selection in Medical Injection Molding
1. Using FDA-Approved Recycled Plastics
- Reduces raw material costs.
- Maintains compliance with medical safety standards.
2. Choosing High-Performance Polymers
- Some lightweight materials require less plastic per part.
- Stronger plastics improve durability, reducing failure rates.
3. Optimizing Resin Usage
- Thin-wall molding lowers material consumption.
- AI-driven monitoring prevents overuse and waste.
4. Working with Reliable Suppliers
- Bulk purchasing lowers material costs.
- Ensures a stable supply chain without price fluctuations.
Optimizing Mold Design to Lower Costs
1. Multi-Cavity Molds
- Produces more parts per cycle.
- Reduces overall production time and costs.
2. Hot Runner Systems
- Reduces plastic waste by eliminating sprues.
- Improves material flow and consistency.
3. Modular Mold Systems
- Uses interchangeable mold inserts for multiple products.
- Saves on tooling and setup costs.
4. Conformal Cooling Channels
- Improves heat dissipation.
- Reduces cycle time and energy use.
Automation for Cost and Quality Control
1. AI-Powered Defect Detection
- Identifies quality issues in real time.
- Reduces scrap rates and rework costs.
2. Robotic Handling Systems
- Automates part removal and packaging.
- Increases efficiency while reducing labor costs.
3. IoT-Enabled Process Monitoring
- Tracks temperature, pressure, and material flow.
- Prevents process variations that lead to defects.
4. Smart Predictive Maintenance
- Sensors detect mold wear and machine issues before failures occur.
- Reduces downtime and costly repairs.
Reducing Energy Consumption Without Sacrificing Quality
1. Switching to Energy-Efficient Machines
- Electric injection molding machines use 30% less energy than hydraulic models.
- Hybrid machines offer a balance between power and efficiency.
2. Optimizing Cooling and Heating Systems
- Smart cooling reduces energy waste.
- AI adjusts temperature settings for better efficiency.
3. Implementing Smart Scheduling
- AI schedules production during off-peak energy hours.
- Reduces electricity costs without affecting output.
Ensuring High Quality While Lowering Costs
1. Strict Quality Control Measures
- Vision inspection systems catch microscopic defects.
- Reduces defective parts and improves yield.
2. Standardized Manufacturing Processes
- Using scientific molding techniques ensures repeatability.
- Maintains quality across high-volume production.
3. Employee Training Programs
- Skilled workers prevent costly mistakes.
- Training improves efficiency and machine operation skills.
4. Data-Driven Decision Making
- AI analyzes production trends for process improvements.
- Predicts potential quality issues before they occur.
The Role of Mold Makers in Cost and Quality Balance
1. Designing Long-Lasting Molds
- Durable molds reduce replacement costs.
- Proper coatings prevent wear and corrosion.
2. Developing Multi-Use Mold Systems
- One mold design can produce multiple medical components.
- Saves costs on tooling and design.
3. Collaborating with Manufacturers on Material Selection
- Recommends cost-effective resins that maintain strength.
- Tests new materials for biocompatibility and durability.
4. Implementing Digital Twin Technology
- Simulates molding processes before production starts.
- Prevents costly errors and reduces trial runs.
Challenges in Balancing Cost and Quality
1. Rising Raw Material Prices
- Market fluctuations make long-term cost control difficult.
- Advanced planning and bulk purchases can mitigate risks.
2. Maintaining Compliance While Reducing Costs
- Medical regulations add testing and documentation costs.
- Digital tracking systems streamline compliance processes.
3. Adopting New Technologies
- Upgrading to AI-driven molding machines requires investment.
- Long-term savings offset initial costs.
4. Managing Labor Costs
- Skilled labor is expensive but necessary for high-quality production.
- Automation reduces reliance on manual labor.
Latest Innovations in Cost-Effective Medical Injection Molding
1. AI-Optimized Process Control
- AI adjusts molding parameters automatically.
- Reduces material waste and energy consumption.
2. 3D Printing for Mold Prototyping
- Lowers costs by reducing trial-and-error testing.
- Speeds up the development of new medical devices.
3. Blockchain for Supply Chain Efficiency
- Ensures transparent pricing for raw materials.
- Reduces procurement fraud and delays.
4. Nano-Enhanced Plastics for Durability
- Stronger materials reduce component failure rates.
- Lowers the need for expensive material replacements.
5. Digital Twins for Process Simulation
- Virtual modeling detects design flaws before production.
- Reduces material and time wastage.
Future Trends in Cost and Quality Optimization
1. Fully Automated Medical Molding Facilities
- AI-powered factories will run with minimal human intervention.
- Maximizes efficiency while maintaining strict quality control.
2. Sustainable Material Innovations
- Biodegradable medical plastics will reduce long-term costs.
- Eco-friendly alternatives will meet compliance standards.
3. Smart Manufacturing with IoT Integration
- Sensors will track efficiency in real time.
- AI will suggest cost-saving adjustments automatically.
4. AI-Driven Supply Chain Management
- Smart procurement will ensure optimal material pricing.
- Reduces shortages and overstocking.
5. Customizable Molding Solutions
- Modular molds will allow quick product adjustments.
- Reduces costs for manufacturers producing multiple medical devices.
Balancing cost and quality in medical injection molding requires innovation. Mold makers play a key role in optimizing materials, automation, and process control. AI, IoT, and predictive maintenance further enhance efficiency. By adopting these methods, manufacturers can produce high-quality medical components at a lower cost, ensuring long-term success in the industry.