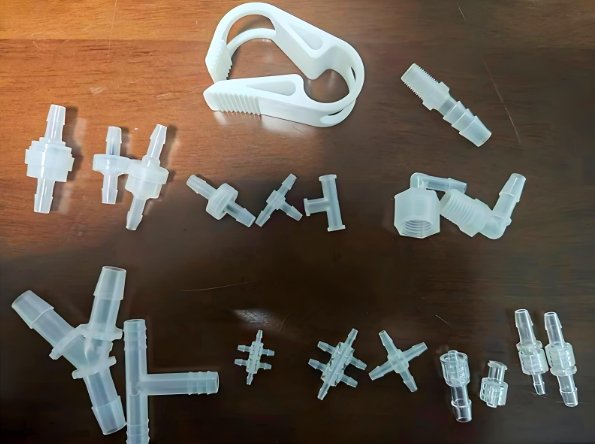
Precision healthcare is the future of medicine. It focuses on customized treatments and advanced medical devices. Medical injection molding plays a key role in this transformation. It enables the production of high-quality, precise components. Mold makers help develop devices that improve patient care. This article explores how injection molding advances precision healthcare.
1. The Role of Medical Injection Molding in Precision Healthcare
1.1 Custom Medical Devices
Injection molding allows the mass production of custom medical devices. These include surgical tools, implants, and diagnostic equipment.
1.2 High Precision and Consistency
Medical devices require extreme accuracy. Medical injection molding ensures uniformity in every part.
1.3 Biocompatible Materials
Modern plastics used in injection molding are safe for medical use. Mold makers choose FDA-approved materials to prevent reactions.
2. Innovations in Medical Injection Molding
2.1 Micro Injection Molding
Tiny components are essential for precision healthcare. Micro-molding creates parts for pacemakers, hearing aids, and sensors.
2.2 Multi-Shot Injection Molding
This process combines multiple materials in one part. It improves functionality and reduces assembly time.
2.3 3D-Printed Molds for Faster Prototyping
3D printing speeds up mold development. Mold makers can test designs quickly before mass production.
3. Advanced Materials for Medical Injection Molding
3.1 High-Performance Thermoplastics
Materials like PEEK and PC offer strength and flexibility. They are ideal for implants and surgical tools.
3.2 Antimicrobial Plastics
These materials help reduce infections. They are used in catheters and hospital equipment.
3.3 Biodegradable Polymers
Eco-friendly materials reduce medical waste. They are perfect for single-use medical products.
4. The Impact of Automation on Medical Injection Molding
4.1 AI-Driven Quality Control
Artificial intelligence detects defects early. This ensures every part meets high medical standards.
4.2 Robotics in Manufacturing
Robots handle molding, assembly, and packaging. This improves efficiency and reduces contamination risks.
4.3 Smart Factories
Connected machines optimize production. They adjust in real time to maintain precision.
5. Applications of Medical Injection Molding in Healthcare
5.1 Implantable Medical Devices
Precision-molded implants, such as bone screws and joint replacements, enhance patient recovery.
5.2 Drug Delivery Systems
Molded plastic syringes and inhalers ensure accurate medication dosing.
5.3 Wearable Health Monitors
Injection-molded casings protect sensitive electronics in fitness trackers and glucose monitors.
6. The Role of Mold Makers in Advancing Healthcare
6.1 Designing High-Precision Molds
Mold makers create detailed molds that ensure exact specifications.
6.2 Ensuring Regulatory Compliance
They follow strict FDA and ISO standards to guarantee patient safety.
6.3 Continuous Innovation
Mold makers develop new techniques to improve efficiency and reduce costs.
7. Challenges in Medical Injection Molding
7.1 Strict Regulatory Requirements
Meeting medical industry standards requires advanced quality control.
7.2 High Development Costs
Investing in precision molds and materials can be expensive.
7.3 Sustainability Issues
Finding biodegradable and recyclable materials remains a challenge.
8. The Future of Medical Injection Molding in Healthcare
8.1 Personalized Medical Devices
3D scanning and injection molding will create patient-specific implants.
8.2 Smart Medical Devices
Injection-molded casings will house AI-powered healthcare tools.
8.3 Increased Use of Sustainable Materials
Future medical products will use eco-friendly plastics to reduce waste.
Medical injection molding is transforming precision healthcare. Mold makers play a crucial role in developing life-saving devices. As technology advances, injection molding will continue improving patient care. The future of precision healthcare depends on innovation in medical manufacturing.