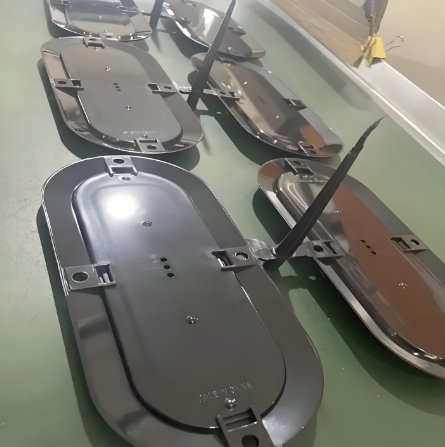
Electronic injection molding has transformed the production of electronic components. It is a key process that allows for precise and cost-effective manufacturing. Mold makers are crucial in ensuring the accuracy and quality of each part. This article discusses the role of injection molding in electronic component production.
1. What Is Electronic Injection Molding?
1.1 Understanding Injection Molding
Injection molding is a process where plastic or other materials are injected into a mold under pressure. The material takes the shape of the mold and solidifies. It is used to create a wide variety of parts. Mold makers design the molds that shape these parts.
1.2 How It Works in Electronics
In electronics, electronic injection molding is used to produce components such as connectors, casings, and housings. These parts must be durable, lightweight, and precise. Molding allows manufacturers to create these parts quickly and efficiently.
2. Why Is Injection Molding Important for Electronics?
2.1 High Precision for Small Components
Electronics often require tiny, precise parts. Electronic injection molding is ideal for creating these small components. It ensures tight tolerances and consistent quality across large volumes.
2.2 Cost-Effective Production
The cost of producing electronic components can be high. However, injection molding reduces production costs by using material efficiently and speeding up manufacturing. High-volume production also lowers unit costs.
2.3 Strength and Durability
Many electronic components need to withstand harsh environments. Electronic injection molding produces strong and durable parts that can resist heat, chemicals, and mechanical stress. This is important for electronic devices used in various industries, including automotive and healthcare.
3. The Role of Mold Makers in Electronic Injection Molding
3.1 Designing Precision Molds
Mold makers play a critical role in designing the molds used in the injection molding process. They ensure that the molds are designed to meet the specific needs of the electronic component being produced. Precision is essential, as even a small error can lead to defects in the final product.
3.2 Material Selection
The selection of materials is another important role of mold makers. Electronics often require specialized plastics that are heat-resistant or have specific electrical properties. Mold makers must choose the right material to meet these requirements.
3.3 Creating Prototypes and Testing
Before large-scale production, mold makers create prototypes to test the design and material choices. This helps ensure that the mold will produce the desired results. Prototyping is an essential step in the injection molding process, especially for complex electronic components.
4. Types of Electronic Components Produced with Injection Molding
4.1 Casings and Housings
One of the most common applications for electronic injection molding is the production of casings and housings. These protect the internal components of electronic devices. The parts must be lightweight, durable, and able to withstand external stress.
4.2 Connectors and Terminals
Connectors and terminals are essential for electrical devices to function properly. Injection molding is used to create these parts with precise dimensions. They must fit perfectly to ensure a reliable electrical connection.
4.3 Switches and Buttons
Injection molding also produces switches and buttons used in electronics. These small components need to be reliable and easy to use. The molding process allows for the production of parts with a smooth surface and accurate fit.
4.4 Insulating Parts
Many electronic devices require insulating parts to prevent electrical shorts and overheating. Mold makers create molds for parts made from insulating materials, ensuring they meet the necessary safety standards.
5. Benefits of Electronic Injection Molding in Component Production
5.1 High Production Speed
Electronic injection molding can produce components quickly, allowing for fast production. This is important in industries where time-to-market is crucial. The process also reduces the need for additional labor and manual work.
5.2 Consistency and Reproducibility
Once a mold is created, it can be used to produce thousands of identical parts. This ensures consistency across all components. Each part meets the same high standards, reducing the chances of defects.
5.3 Flexibility in Design
Injection molding offers flexibility in the design of electronic components. Complex geometries and intricate shapes can be molded, allowing for more creative and functional designs. This flexibility is essential for electronics companies that are constantly innovating.
5.4 Reduced Material Waste
The injection molding process is highly efficient in terms of material usage. Only the amount of material needed to fill the mold is used, minimizing waste. This is especially important in industries that require expensive or specialized materials.
6. Challenges in Electronic Injection Molding
6.1 Complex Component Designs
As electronic devices become smaller and more complex, the design of parts also becomes more intricate. Mold makers face challenges in creating molds that can produce these complex components without defects.
6.2 Material Selection
Choosing the right material is always a challenge in electronic injection molding. The material must meet strict electrical and mechanical requirements while also being compatible with the molding process.
6.3 Tight Tolerances
Electronics often require parts with tight tolerances. Achieving these tolerances can be challenging, especially when parts are small or have complex shapes. Mold makers must use advanced techniques and technology to ensure accuracy.
7. Innovations in Electronic Injection Molding
7.1 Micro Injection Molding
As electronic devices shrink, the demand for smaller components increases. Micro injection molding allows for the production of extremely small parts with high precision. This technology is crucial for the development of wearable devices and small consumer electronics.
7.2 Overmolding and Insert Molding
Overmolding and insert molding are techniques used to create multi-material parts. For example, a part may be molded with both plastic and metal for added strength. These techniques are often used for connectors and housings in electronic devices.
7.3 3D Printing for Prototyping
While injection molding is used for mass production, 3D printing is used for prototyping molds. This allows mold makers to test designs quickly and make adjustments before starting large-scale production.
8. The Future of Electronic Injection Molding
8.1 Increased Demand for Smaller Components
As the demand for smaller and more powerful electronics increases, electronic injection molding will continue to evolve. The ability to create tiny, precise components will be essential for the next generation of devices.
8.2 Smart Manufacturing and Automation
The future of electronic injection molding will likely involve more automation. Smart manufacturing systems will allow for real-time monitoring and quality control, ensuring that every part meets the highest standards.
8.3 Sustainable Manufacturing Practices
Sustainability is becoming more important in manufacturing. Electronic injection molding is expected to adopt more eco-friendly practices, such as using recyclable materials and reducing energy consumption during production.
Electronic injection molding plays a crucial role in the production of electronic components. It offers high precision, cost-efficiency, and fast production times. Mold makers are essential in ensuring the success of this process, as they design molds that meet the exact requirements of each component. As the electronics industry continues to evolve, so will the role of electronic injection molding, making it an essential technology in the future of electronics manufacturing.