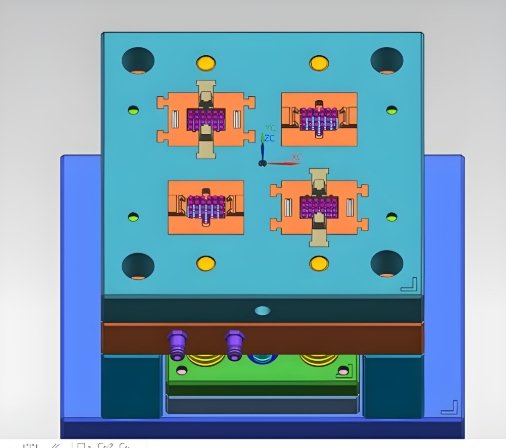
Electronic components require extreme precision. Electronic injection molding ensures accurate, high-quality parts. Tight tolerances play a critical role in maintaining product performance. Even the smallest deviation can lead to failure. Mold makers use advanced techniques to meet strict tolerance requirements.
This article explores the importance of tight tolerances, challenges, and best practices in electronic injection molding.
1. What Are Tight Tolerances?
1.1 Definition of Tight Tolerances
Tight tolerances refer to the small allowable deviations in part dimensions. In electronic injection molding, tolerances are often within microns.
1.2 Why Tight Tolerances Matter
- Ensure proper fit of electronic components
- Prevent signal loss and electrical failure
- Maintain structural integrity
- Improve overall product reliability
1.3 Typical Tolerances in Electronic Injection Molding
Most electronic parts require tolerances of ±0.05 mm or lower. Some micro-components need even tighter tolerances.
2. Challenges in Achieving Tight Tolerances
2.1 Material Selection
Different plastics shrink at different rates. High-performance materials like PBT, LCP, and PPS offer better dimensional stability.
2.2 Mold Design and Precision
Mold makers must create highly accurate molds. Small design errors can cause defects.
2.3 Process Control
Temperature, pressure, and cooling rates affect final part dimensions. Any variation impacts tolerances.
2.4 Machine Accuracy
Older machines may struggle to maintain precision. Modern injection molding machines use servo-driven controls for better accuracy.
2.5 Environmental Factors
Humidity and temperature changes can cause material expansion or contraction. Proper storage and handling are necessary.
3. Role of Mold Makers in Achieving Tight Tolerances
3.1 High-Precision Mold Manufacturing
Mold makers use CNC machining, EDM, and laser cutting to create ultra-precise molds.
3.2 Mold Cavity Inspection
Before production, molds undergo strict dimensional checks to ensure accuracy.
3.3 Use of High-Quality Steel
Premium steel grades reduce wear and maintain tight tolerances over long production runs.
3.4 Optimized Cooling Systems
Uniform cooling prevents warping and shrinkage, ensuring parts remain within tolerance.
4. Best Practices for Maintaining Tight Tolerances
4.1 Advanced Injection Molding Machines
Modern machines with closed-loop control systems adjust parameters in real time.
4.2 In-Process Quality Control
Real-time monitoring detects variations early, reducing waste and improving efficiency.
4.3 Post-Molding Inspection
Coordinate measuring machines (CMM) and optical sensors verify final part dimensions.
4.4 Automation for Consistency
Robotic handling minimizes human error, improving repeatability in high-volume production.
5. Applications Requiring Tight Tolerances
5.1 PCB Connectors
Small deviations can cause poor electrical connections and signal loss.
5.2 Micro-Switches
Precision ensures proper actuation and reliable performance.
5.3 LED Components
Uniform part dimensions improve light output and thermal management.
5.4 Smartphone Housings
Accurate molding ensures perfect fit for internal components.
5.5 Automotive Sensors
Sensors must meet strict tolerances to function correctly in harsh environments.
6. Future of Tight Tolerances in Electronic Injection Molding
6.1 AI-Driven Process Control
Artificial intelligence optimizes machine settings for maximum precision.
6.2 Nanotechnology in Mold Making
New materials and coatings reduce tool wear, improving mold longevity.
6.3 3D Printing for Prototype Validation
Rapid prototyping helps mold makers refine designs before full production.
6.4 Sustainable Manufacturing
Improved molding techniques reduce waste while maintaining tight tolerances.
Tight tolerances are essential for electronic injection molding. They ensure product reliability, performance, and longevity. Mold makers use advanced technology to maintain precision in every part. By optimizing materials, processes, and quality control, manufacturers can achieve high accuracy in electronic components.
As technology evolves, precision requirements will become even stricter. Investing in high-precision mold making and automation will be key to staying competitive in electronic injection molding.