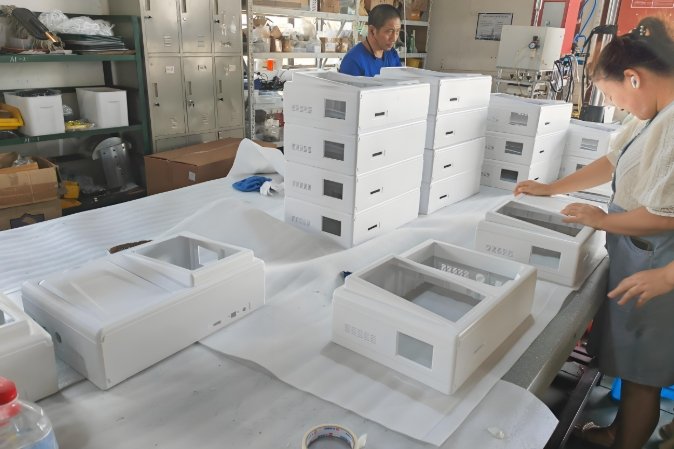
Electronic injection molding requires the use of high-performance polymers. These materials play a crucial role in creating durable, precise, and efficient electronic components. Mold makers must carefully select polymers based on specific needs like electrical insulation, heat resistance, and mechanical strength. In this article, we explore high-performance polymers, their benefits, and their role in electronic injection molding.
1. What Are High-Performance Polymers?
High-performance polymers are advanced materials with superior mechanical, thermal, and chemical properties. They are used in critical applications where standard plastics might fail. These polymers offer enhanced strength, resistance to heat, and long-term durability.
1.1 Key Characteristics of High-Performance Polymers
- High Thermal Stability
These polymers maintain their properties even at extreme temperatures. - Chemical Resistance
They resist degradation from exposure to chemicals. - Excellent Mechanical Properties
High performance under stress and load. - Electrical Insulation
Crucial for electrical and electronic components.
2. Types of High-Performance Polymers in Electronic Injection Molding
Several high-performance polymers are commonly used in electronic injection molding. These materials meet the stringent requirements of the electronics industry.
2.1 Polyphenylene Sulfide (PPS)
- High Heat Resistance: PPS can withstand high temperatures, making it ideal for electronic components exposed to heat.
- Chemical Resistance: It is resistant to most chemicals, including solvents and oils.
- Applications: Used in connectors, switches, and circuit breakers.
2.2 Polyetherimide (PEI)
- Exceptional Thermal Stability: PEI remains stable at high temperatures.
- Mechanical Strength: It offers excellent mechanical properties.
- Applications: Often used in electrical enclosures and connectors.
2.3 Liquid Crystal Polymers (LCP)
- Low Moisture Absorption: LCPs are resistant to moisture, making them ideal for electronics exposed to humid environments.
- High Precision: They allow for precise molding of thin-walled components.
- Applications: Widely used in microelectronics and connectors.
2.4 Polyamide-imide (PAI)
- High-Temperature Performance: PAI can withstand extreme temperatures, up to 260°C.
- Mechanical Strength: It provides excellent tensile strength.
- Applications: Commonly used for electrical insulation and parts that operate at high temperatures.
2.5 Polycarbonate (PC)
- Impact Resistance: Polycarbonate offers high impact resistance and toughness.
- Optical Clarity: It can be used in applications requiring transparency.
- Applications: Often used in electrical housings and protective covers.
3. Advantages of High-Performance Polymers in Electronics
3.1 Improved Durability
High-performance polymers offer better resistance to wear, chemicals, and extreme temperatures. This enhances the longevity of electronic components.
3.2 Precision in Molding
Polymers like LCP provide excellent flow properties for precise molding. This ensures the accurate production of components like connectors and housings.
3.3 Enhanced Safety
High-performance polymers are often flame-retardant. They can be used in safety-critical applications where failure could lead to significant issues.
3.4 Better Electrical Insulation
Materials like PEI and PPS provide excellent electrical insulation, preventing short circuits and damage to sensitive electronic components.
4. How Mold Makers Select High-Performance Polymers
4.1 Understanding Application Requirements
Mold makers must first understand the requirements of the end product. This includes the electrical properties, mechanical stress, and environmental conditions the part will face.
4.2 Balancing Cost and Performance
While high-performance polymers offer superior qualities, they can also be expensive. Mold makers must balance the cost of materials with the requirements of the application.
4.3 Design Considerations
The design of the mold influences material selection. The choice of polymer should align with the part’s geometry and the mold’s capabilities.
4.4 Testing and Prototyping
Mold makers often run prototypes using different polymers to assess performance. This helps determine which material performs best in real-world conditions.
5. Applications of High-Performance Polymers in Electronic Components
High-performance polymers are used in a wide range of electronic components. These polymers ensure the components are durable, reliable, and functional.
5.1 Connectors and Switches
- PPS and PEI are ideal for connectors and switches.
- They withstand high temperatures and electrical currents without degrading.
5.2 Circuit Boards
- LCP and PAI provide precision and stability for microelectronics.
- These polymers are resistant to moisture, ensuring the longevity of circuit boards.
5.3 Electrical Housings
- Polycarbonate (PC) is used for electrical housings due to its transparency and strength.
- It protects sensitive components from physical damage and environmental factors.
5.4 Power Supply Components
- PPS and PEI are used in power supply components because of their thermal stability and resistance to electrical currents.
6. Challenges in Using High-Performance Polymers
6.1 Material Costs
High-performance polymers can be expensive. This increases the overall production costs, especially for high-volume manufacturing.
6.2 Processing Complexity
Some high-performance polymers require specialized processing techniques. Mold makers must adjust the mold design and injection molding conditions to handle these materials effectively.
6.3 Availability and Supply Chain Issues
Certain high-performance polymers may not be readily available or might face supply chain disruptions. Mold makers need to ensure a reliable source for the required materials.
7. The Future of High-Performance Polymers in Electronics
7.1 Bioplastics and Sustainability
With growing demand for sustainable manufacturing, bioplastics are gaining attention. High-performance polymers derived from renewable resources may offer a more eco-friendly alternative in the future.
7.2 Nanomaterials
Nanomaterials are expected to revolutionize high-performance polymers. By integrating nanoparticles, these materials can achieve even greater strength, thermal stability, and conductivity.
7.3 Smart Polymers
Smart polymers, which change properties in response to stimuli, may also play a role in the future of electronic injection molding. These materials could allow for more flexible and adaptable electronic components.
High-performance polymers are critical for electronic injection molding. Mold makers must choose the right material based on the application’s needs. By selecting polymers that offer superior heat resistance, electrical insulation, and mechanical properties, mold makers ensure the production of high-quality, reliable electronic components. As technology advances, new polymers and innovations will continue to enhance the capabilities of electronic injection molding.