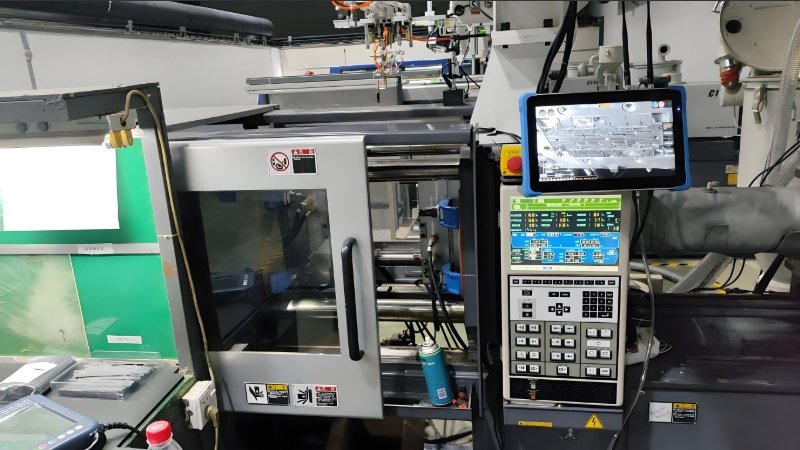
Electronics require extreme precision. Dust and particles can damage circuits. Electronic injection molding ensures high-quality parts. A skilled mold maker uses cleanroom molding to prevent contamination. This article explores cleanroom techniques, benefits, and challenges.
1. What is Cleanroom Molding?
1.1 Definition
Cleanroom molding takes place in a controlled environment. Electronic injection molding requires a dust-free area.
1.2 How It Works
A mold maker operates machines in a sealed space. Air filters remove tiny particles.
1.3 Why Electronics Need It
Even small dust particles can cause failures. Electronic injection molding needs precision.
2. Cleanroom Classifications
2.1 ISO Standards
Cleanrooms follow strict ISO standards. A mold maker ensures compliance.
2.2 Common Cleanroom Classes
- ISO 7 (10,000 particles per cubic foot)
- ISO 6 (1,000 particles per cubic foot)
- ISO 5 (100 particles per cubic foot)
2.3 Choosing the Right Cleanroom
High-end electronics need higher standards. Electronic injection molding adapts to needs.
3. Equipment Used in Cleanroom Molding
3.1 HEPA and ULPA Filters
These remove 99.99% of particles. A mold maker ensures proper filtration.
3.2 Airflow Systems
Laminar airflow keeps the environment clean. Electronic injection molding benefits from stable conditions.
3.3 Sealed Molding Machines
Special machines prevent outside contamination. A mold maker operates them under strict guidelines.
4. Materials for Cleanroom Molding
4.1 Low-Particulate Resins
Clean resins reduce contamination risk. Electronic injection molding uses medical-grade plastics.
4.2 Anti-Static Additives
Electronics attract dust. A mold maker uses anti-static materials.
4.3 UV-Resistant Polymers
Sensitive parts need protection. Electronic injection molding prevents degradation.
5. Molding Techniques for Cleanroom Environments
5.1 Overmolding
Combines two materials. A mold maker ensures a tight bond.
5.2 Micro-Molding
Creates tiny, precise parts. Electronic injection molding enables miniaturization.
5.3 Insert Molding
Encapsulates metal inserts in plastic. A mold maker enhances durability.
6. Benefits of Cleanroom Molding for Electronics
6.1 Eliminates Contamination Risks
No dust, no defects. Electronic injection molding ensures purity.
6.2 Increases Product Lifespan
Cleaner parts last longer. A mold maker prevents premature failure.
6.3 Improves Conductivity
No debris means better electrical flow. Electronic injection molding enhances performance.
7. Applications of Cleanroom Molding in Electronics
7.1 Medical Devices
Pacemakers and sensors need precision. A mold maker follows strict medical standards.
7.2 Semiconductor Components
Chips require ultra-clean parts. ensures defect-free manufacturing.
7.3 Wearable Tech
Smartwatches and fitness trackers need sealed components. A mold maker ensures reliability.
8. Cleanroom Maintenance for Molding Facilities
8.1 Regular Air Quality Checks
Monitors detect contaminants. Electronic injection molding must meet air purity standards.
8.2 Strict Employee Protocols
Workers wear protective clothing. A mold maker follows hygiene rules.
8.3 Cleaning Procedures
Daily sanitization removes particles. Electronic injection molding maintains cleanliness.
9. Challenges in Cleanroom Molding
9.1 High Costs
Filtration and equipment are expensive. A mold maker finds cost-effective solutions.
9.2 Complex Setup
Setting up a cleanroom takes time. Electronic injection molding requires precise conditions.
9.3 Strict Regulations
Laws require compliance. A mold maker stays updated on cleanroom standards.
10. The Future of Cleanroom Molding in Electronics
10.1 AI and Automation
Robots reduce human contamination. Electronic injection molding becomes more efficient.
10.2 Sustainable Cleanrooms
Energy-efficient filters lower costs. A mold maker adopts green practices.
10.3 3D Printing in Clean Environments
Additive manufacturing meets electronic injection molding. Hybrid production enhances precision.
Cleanroom molding is crucial for electronic injection molding. A skilled mold maker ensures contamination-free parts. The industry will continue improving technology and efficiency.