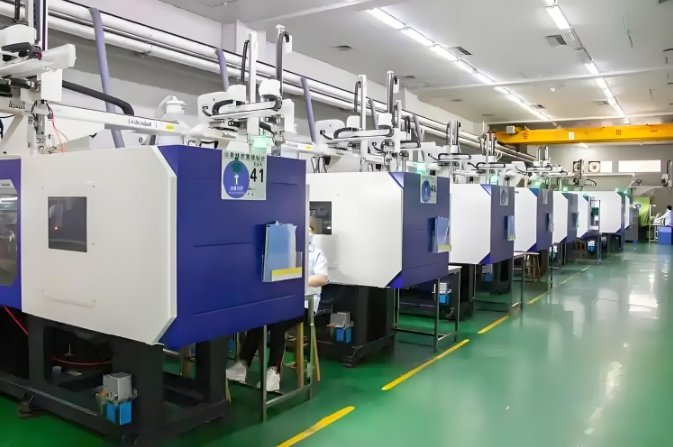
Warpage is a common issue.
It twists parts out of shape.
In electronics, that’s a big problem.
Every part must fit perfectly.
Even a small warp can ruin a product.
In Electronic Injection Molding, warpage must be stopped.
And a skilled Mold Maker plays a big role.
Let’s look at why warpage happens.
And how to prevent it.
What Is Warpage?
Warpage is a shape change.
It happens after the part cools.
The part bends or twists.
It does not match the design.
This hurts function.
And looks bad.
In Electronic Injection Molding, warped parts don’t fit.
That leads to waste.
And customer complaints.
Main Causes of Warpage
Uneven Cooling
Plastic cools fast.
But not always evenly.
Thicker spots cool slow.
Thin areas cool fast.
This causes pulling.
And bending.
Poor Mold Design
If the mold is not balanced,
plastic won’t flow evenly.
Bad flow = bad stress.
Bad stress = warpage.
Wrong Material Choice
Some plastics shrink more.
Others stay stable.
The wrong resin makes warpage worse.
Poor Gate Placement
The gate is where plastic enters.
If it’s in the wrong spot,
the plastic flows badly.
And stresses build up.
Choose the Right Mold Maker
A top Mold Maker stops warpage before it starts.
They know how to design a good mold.
They know Electronic Injection Molding inside out.
They check flow.
They adjust cooling lines.
They place gates correctly.
The best molds come from the best Mold Makers.
Proper Mold Design
Uniform Wall Thickness
Keep walls even.
Thick and thin parts cool at different speeds.
That causes bends.
Good Mold Makers design even thickness.
That means smooth cooling.
And less warpage.
Correct Cooling System
Cooling must be balanced.
Good molds have channels close to the part.
And evenly spaced.
Smart Mold Makers use simulations.
They check how the part cools.
They adjust channels as needed.
Good Venting
Trapped air causes pressure.
Pressure causes distortion.
Vents release air.
And prevent stress.
Mold Makers who focus on electronics know this well.
Material Selection Matters
Use Low-Shrink Plastics
Some materials shrink more.
ABS shrinks less than nylon.
Pick a resin that stays stable.
In Electronic Injection Molding, stability is key.
Dry the Resin Properly
Wet resin = bad parts.
Moisture leads to bubbles.
And weak spots.
Always dry the material fully.
A quality Mold Maker ensures this step is never skipped.
Control the Molding Process
Optimize Injection Speed
Too fast, and stress builds up.
Too slow, and the plastic sets early.
Find the right speed.
This needs testing.
And data.
Good Mold Makers help set these numbers.
Set Correct Packing Pressure
After filling, pressure holds the shape.
Too little, and shrink happens.
Too much, and warpage builds up.
Balance is key.
And takes experience.
Set Proper Cooling Time
Don’t eject parts too early.
Let them set fully.
A few seconds more cooling
can stop warping.
Use Mold Flow Analysis
This software simulates the flow.
It shows hot spots.
Shrink zones.
Stress areas.
Top Mold Makers use this tool.
It saves money.
And reduces trial and error.
In Electronic Injection Molding, it’s a must.
Test with Prototypes
Make a sample mold.
Run small batches.
Check for warpage early.
3D printed molds help too.
A smart Mold Maker will offer these options.
Keep the Mold Clean
Dirt blocks vents.
Grease builds up.
Both affect the shape.
Clean molds make clean parts.
This reduces warpage too.
Mold Makers must have a cleaning plan.
Use of Proper Ejection System
Ejectors push the part out.
If they push unevenly,
the part bends.
Balanced ejectors stop this.
Another detail only a good Mold Maker handles well.
Tool Maintenance
Over time, tools wear.
Cooling lines clog.
Surfaces scratch.
This affects part shape.
Preventive maintenance is key.
A strong Mold Maker offers this service.
Real-Time Process Monitoring
Some machines watch pressure.
And temperature.
They adjust settings live.
This reduces defects.
In Electronic Injection Molding, it’s a great feature.
Ask your Mold Maker if they use it.
Standardize Operating Procedures
Keep things the same.
Same speed.
Same heat.
Same material.
This keeps parts consistent.
And stops new warpage problems from starting.
Training for Operators
Machines don’t run themselves.
Skilled operators check quality.
They know what warpage looks like.
And when to stop the line.
A good Mold Maker will train your staff.
Or offer molding services with skilled teams.
Partner with the Right Team
Electronic Injection Molding is not easy.
There are many small details.
Choose a Mold Maker who knows electronics.
One who has done it before.
One who can show real samples.
A partner who listens.
And improves with you.
Warpage is a serious issue.
But it can be solved.
With smart design.
Good tools.
Right materials.
And a skilled Mold Maker.
Electronic Injection Molding needs perfect parts.
So you need the perfect partner.
Start with good molds.
Made by experts.
And watch your reject rate drop.
No more bending.
No more stress.
Just clean, straight, working parts.