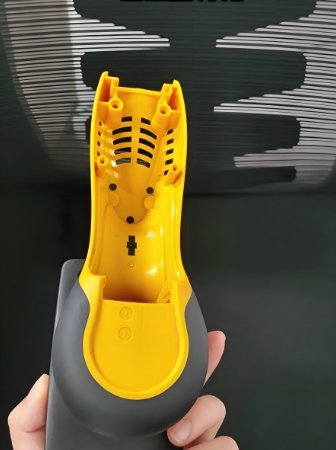
Electronic products must work every time. But sometimes, they fail. These failures are often linked to poor design or bad molding. In many cases, the root cause is bad Electronic Injection Molding. When parts are not molded well, they do not last. A skilled Mold Maker can fix this problem.
Let’s explore why parts fail. And how better molding prevents these issues.
1. Poor Fit and Misalignment
Many electronic parts must fit tightly. But bad molding creates poor fits. When parts don’t align, they stop working. Connectors and sockets fail. Internal circuits don’t match.
This happens when Electronic Injection Molding is done with loose tolerances. Or when shrinkage is not considered. A good Mold Maker knows how to fix that. They design molds that account for shrinkage and tolerance.
2. Warping During Cooling
Plastic shrinks as it cools. If cooling is not even, warping occurs. Warped parts don’t fit. They may break. Or they may not hold the electronic components well.
Better cooling in the mold helps. That’s where the Mold Maker plays a role. They design cooling systems to avoid warping. In Electronic Injection Molding, even cooling is key to strong parts.
3. Weak Points and Cracks
Sometimes, molded parts crack under stress. This happens due to bad design or poor material flow. Cracks form in thin areas. Or near corners and gates.
To fix this, the Mold Maker uses better gate positions. They adjust wall thickness in design. They also select the right material. These steps prevent cracks and weak spots in Electronic Injection Molding.
4. Short Shots and Incomplete Parts
A short shot means the mold didn’t fill completely. This causes missing details or holes. These parts cannot be used. It’s a common problem in Electronic Injection Molding.
Why does this happen? Low pressure, bad flow, or narrow gates. A smart Mold Maker fixes all these. They optimize gate size, pressure, and material speed.
5. Burrs and Flash
Sometimes, excess plastic leaks from the mold. This forms sharp edges called burrs or flash. These make parts unsafe. They may also interfere with fit.
Flash happens when molds don’t close tightly. It may also result from high injection pressure. A skilled Mold Maker ensures mold surfaces match perfectly. This prevents leaks in Electronic Injection Molding.
6. Inconsistent Dimensions
Electronic parts must be accurate. If one part is too big or too small, it won’t fit. This leads to assembly problems.
Inconsistent molding often results from tool wear. Or from changing temperatures and pressures. A good Mold Maker maintains the mold well. They check wear and adjust process settings.
7. Defects from Contaminated Material
Dust and dirt cause defects in molded parts. Contaminated plastic leads to weak areas. Sometimes it causes black spots or bubbles.
To avoid this, Electronic Injection Molding must be clean. The material must be stored and handled well. Mold Makers clean the molds and machines often. They also use filters during the molding process.
8. Parts That Don’t Last
Some parts fail after weeks of use. They may break or lose shape. This is due to poor materials or bad mold design.
The Mold Maker selects strong materials. They test them under heat and pressure. Good design and molding help parts last longer. That’s the power of proper Electronic Injection Molding.
9. Poor Surface Finish
Electronic parts must look good. Poor molding causes dull, rough, or marked surfaces. This hurts the product’s value.
Surface problems come from worn molds or dirty tools. A quality Mold Maker polishes the mold carefully. They also use good venting to avoid air traps. In Electronic Injection Molding, small details matter.
10. Assembly Line Rejection
Poorly molded parts fail during assembly. They don’t fit or break when pressed. This slows down the production line.
Rejects cost money. They also waste material. A good Mold Maker reduces rejects. They ensure every part is the same. High-precision molds mean high-quality parts.
11. Electric Failures from Poor Molded Housings
Some failures happen because the housing doesn’t protect the inside. Moisture gets in. Wires come loose. Or the circuit shorts.
This is an Electronic Injection Molding design issue. The Mold Maker must create tight seals. They must also use heat-resistant and insulated materials.
12. Lack of Testing and Validation
Bad parts sometimes reach the market. Why? Because no one tested them well. Molds and parts must go through checks.
Better Mold Makers test each mold. They run samples. They check size, strength, and function. This step is crucial in Electronic Injection Molding.
13. Poor Mold Maintenance
Even the best mold fails if not maintained. Dirt builds up. Edges wear out. Then, parts start failing.
Good Mold Makers follow strict cleaning schedules. They repair worn areas quickly. This keeps every shot consistent and clean.
14. The Role of the Mold Maker
Behind every quality part is a great Mold Maker. They design, build, and maintain the mold. Their skills ensure accuracy, strength, and speed.
In Electronic Injection Molding, the mold is the heart of the process. A poor mold leads to poor parts. But a great Mold Maker guarantees success.
Conclusion: Prevent Failure with Better Molding
Electronic parts fail for many reasons. Most of them link back to bad molding. Weak materials, bad flow, warping, and more can cause breakdowns.
But every issue can be solved. And every defect can be prevented. The key is better Electronic Injection Molding. And the secret behind that? A skilled and experienced Mold Maker.
Better molding means better parts. It means longer life, better fits, and higher quality. In the end, it saves time and money.
Choose the right Mold Maker. Trust in expert Electronic Injection Molding. And watch failure rates drop.