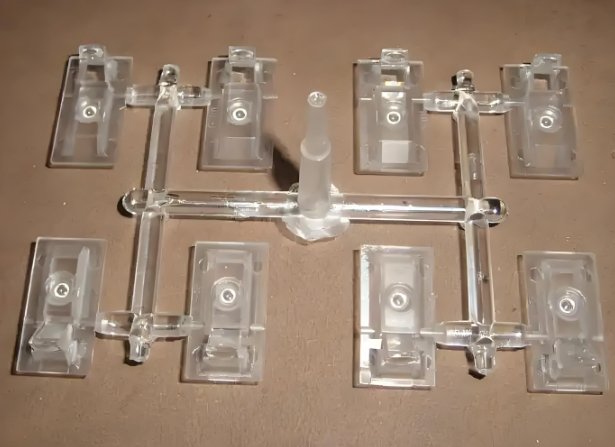
Thin-wall molding is common in electronic parts. It helps make devices smaller, lighter, and more efficient. But it brings challenges. Cracks, short shots, warping, and other issues often appear. These problems hurt quality and cause failure.
Better Electronic Injection Molding can solve this. And a skilled Mold Maker plays a big role. Let’s explore how.
1. What Is Thin-Wall Molding?
Thin-wall molding means the plastic part has very thin walls. Often less than 1mm. These parts need high precision. They must hold tight tolerances. They must also be strong enough to protect electronics.
Thin walls cool fast. They resist flow. So, Electronic Injection Molding must be fast, hot, and precise. Only a smart Mold Maker can design a mold that meets these needs.
2. Flow Problems in Thin Walls
Plastic must flow fast to fill thin sections. But thin walls resist flow. This causes short shots. Some areas may not fill at all. Or the plastic may freeze too soon.
To fix this, the Mold Maker increases gate size or uses hot runners. They also design smooth flow paths. In Electronic Injection Molding, flow control is key to success.
3. Warping After Molding
Thin walls cool fast. But uneven cooling causes warping. Parts bend or twist. This ruins the fit. It can break the part during use.
To stop this, the Mold Maker adds cooling channels in the right spots. They use balanced designs. That keeps the mold temperature even. In Electronic Injection Molding, good cooling prevents distortion.
4. Cracks and Weakness
Thin walls are fragile. If pressure is too high, they crack. If the part shrinks unevenly, stress builds. That leads to failure.
Good Mold Makers avoid sharp corners and thin ribs. They adjust material flow to reduce stress. They also use tough materials for thin walls.
5. Burn Marks and Overheating
Fast flow and high pressure create heat. If air cannot escape, the heat burns the plastic. This leaves black marks. It weakens the part.
Electronic Injection Molding must have proper venting. The Mold Maker adds air vents at the right points. They keep plastic flow smooth and clean.
6. Choosing the Right Material
Not all plastics are good for thin-wall molding. Some are too thick. Some are too brittle. Choosing the wrong one causes part failure.
A skilled Mold Maker knows the best materials. They test them under pressure and heat. Materials with fast flow, high strength, and good bonding are best for Electronic Injection Molding.
7. Mold Design Matters
Thin-wall parts need perfect molds. A small error causes big problems. Molds must be strong and precise.
The Mold Maker uses steel with high hardness. They polish the mold to smooth the flow. They also ensure perfect cavity alignment.
In Electronic Injection Molding, mold quality affects every part made.
8. High-Speed Injection Required
Slow filling doesn’t work. Thin parts freeze fast. So, injection must be quick and powerful.
Electronic Injection Molding uses high-speed machines. The Mold Maker designs the mold to handle pressure. Gates must be strong. Runners must be short.
Fast action ensures the mold fills fully and evenly.
9. Avoiding Flash
Flash happens when plastic leaks from the mold. Thin-wall parts are more at risk. They can’t handle pressure leaks.
To stop flash, the Mold Maker uses tight tolerances. They check mold alignment often. They also use strong clamping in Electronic Injection Molding.
10. Temperature Control
Temperature affects flow, strength, and cooling. Too hot, and the part burns. Too cold, and it won’t fill.
Good Mold Makers install heaters and coolers in the mold. They use sensors to track heat. That keeps every shot the same in Electronic Injection Molding.
11. Avoiding Sink Marks
Sink marks appear when thick areas cool slower. In thin-wall parts, small changes can cause these marks.
The Mold Maker keeps wall thickness even. They reduce rib size. They change gate position to balance flow. That avoids cosmetic flaws in thin walls.
12. Holding Tight Tolerances
Thin walls make tight tolerances hard. Even small changes cause part rejection.
Good Mold Makers use CNC machines for precision. They check each mold with 3D tools. In Electronic Injection Molding, this ensures every part fits right.
13. Using Simulation Tools
Before building the mold, smart teams run simulations. They test flow, shrinkage, and cooling.
Mold Makers use CAE tools to improve mold design. This cuts trial-and-error time. And it improves Electronic Injection Molding accuracy.
14. Reducing Cycle Time
Short cycle times save money. But fast molding risks defects. Warping, burns, or short shots can occur.
With proper cooling and good material flow, the Mold Maker can cut cycle time. Faster molding still keeps part quality high.
15. Repeating Results Every Time
Electronic parts need consistency. One bad part can break the whole device.
The Mold Maker checks the mold after each batch. They clean it. They fix worn areas. Electronic Injection Molding depends on repeatable results.
16. Avoiding Delamination
Some thin-wall parts show delamination. This means layers peel apart. It’s caused by moisture or poor bonding.
To stop this, the Mold Maker dries the resin well. They use proper heat settings. That keeps thin walls strong in Electronic Injection Molding.
17. Teamwork Between Maker and Molder
The Mold Maker and the molder must work as one team. Design, testing, and adjustments all require teamwork.
In Electronic Injection Molding, success means both sides talk often. That way, thin-wall molding becomes smooth and problem-free.
18. Testing Parts in Real Use
Before mass production, the molded part must be tested. Bending, heat, moisture, and pressure tests are key.
The Mold Maker may build test molds. They mold samples and check results. Only then is the mold approved for real Electronic Injection Molding.
19. Updating Old Molds
Old molds may not work well for thin walls. They may not handle high pressure. Or they may have bad cooling.
A good Mold Maker can rebuild or update the mold. They can add vents or change runners. That brings old tools up to Electronic Injection Molding standards.
Thin-wall molding is tough. It takes speed, power, and skill. Without the right mold, problems will happen. Cracks, warps, burns, and short shots are common.
But with help from an expert Mold Maker, these problems can be solved. Better molds mean better parts. In Electronic Injection Molding, thin-wall parts succeed when the mold is just right.
Choose quality. Choose precision. Work with a trusted Mold Maker. That’s how you win in thin-wall molding.