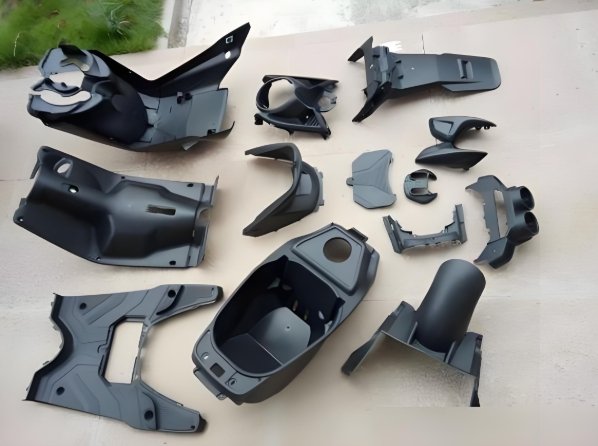
In Electronic Injection Molding, molds endure a lot of stress. The pressure, temperature, and constant use can lead to mold wear. Over time, this affects part quality and production efficiency. Fortunately, a skilled Mold Maker can help reduce mold wear. This ensures longer mold life and better parts. Let’s explore how to manage mold wear effectively.
What Is Mold Wear?
Mold wear refers to the gradual degradation of a mold due to repeated use. In Electronic Injection Molding, molds are exposed to extreme heat, pressure, and friction. These factors cause the mold to degrade over time. Wear leads to defects, reduced part quality, and increased downtime.
Why Is Mold Wear a Problem in Electronic Injection Molding?
In Electronic Injection Molding, precision is essential. Small defects or damage in the mold can lead to product failures. Inconsistent parts can cause issues in electronic components, leading to poor performance. Mold wear results in increased repair costs, downtime, and production delays.
The Main Causes of Mold Wear
Mold wear occurs due to several factors:
1. Heat Stress
Molds are exposed to high temperatures during the injection process. Constant heating and cooling cycles can cause thermal expansion and contraction. Over time, this leads to cracks and surface wear.
2. Friction
Friction occurs as the molten plastic flows through the mold. Over time, this can cause the mold surface to wear down. High-pressure injection also increases friction and accelerates wear.
3. Corrosion
Certain plastics and additives can react with the mold material. This leads to corrosion, especially in areas where plastic accumulates. Corrosion weakens the mold and can lead to failures.
4. Impact and Pressure
High-pressure injection can cause impacts on the mold cavity. This leads to material fatigue and deformation. Over time, this reduces the mold’s ability to produce consistent parts.
How to Reduce Mold Wear in Electronic Injection Molding
1. Use the Right Mold Material
The material used to make the mold plays a key role in wear resistance. A skilled Mold Maker will select the best material based on the type of plastic used and the part design. High-strength alloys and hardened steels can resist wear better than softer metals.
Stainless steel, for example, offers excellent corrosion resistance. Tool steel is durable and can withstand high pressures. Using the right material for the mold ensures it lasts longer and performs better.
2. Optimize Cooling Systems
Cooling systems are critical in Electronic Injection Molding. Efficient cooling helps reduce the stress that leads to thermal expansion and contraction. A Mold Maker can design optimized cooling channels that maintain uniform temperature throughout the mold. This reduces thermal cycling, minimizing mold wear.
Proper cooling also helps in maintaining part quality. When cooling is uneven, parts can warp, which stresses the mold.
3. Control Injection Pressure
High injection pressure can increase friction and wear. A Mold Maker will design the mold to handle the required pressure without causing unnecessary stress. Using lower injection pressure when possible can reduce friction and extend mold life.
Monitoring and controlling the injection pressure during the molding process also helps. Too much pressure can deform the mold cavity, leading to wear.
4. Use Mold Coatings
Applying special coatings to the mold surface can significantly reduce wear. Coatings such as chrome plating or nitride coatings can improve hardness and resistance to friction and corrosion. These coatings form a protective layer that prevents the mold from wearing out quickly.
A Mold Maker can recommend the right coating based on the type of plastic and production volume. Coatings protect the mold from damage and improve part consistency.
5. Regular Maintenance and Inspections
Regular maintenance helps identify issues before they lead to major problems. A Mold Maker will inspect the mold for signs of wear and tear, such as cracks, scratches, or rust. Small issues can be fixed early, preventing more serious damage down the line.
Periodic cleaning of the mold also helps. Removing residue and contaminants prevents build-up, which can cause corrosion and wear. This maintenance ensures that the mold operates efficiently and consistently.
6. Reduce Cycle Times
Longer cycle times increase wear. Each cycle adds stress to the mold. By reducing cycle time, you reduce the number of times the mold is subjected to heat and pressure. This extends its lifespan.
A Mold Maker can optimize the mold design to reduce cycle time without compromising part quality. Efficient cooling, optimized injection speeds, and good mold design all contribute to shorter cycles.
7. Use High-Quality Materials
Using high-quality plastic materials can reduce the wear on the mold. Some plastics are more abrasive than others. When a Mold Maker selects materials for molding, they take into account the abrasion factor of the plastic. Choosing the right material ensures the mold wears more slowly.
In Electronic Injection Molding, materials such as liquid silicone rubber (LSR) can be used for softer components, reducing wear compared to more abrasive materials.
8. Design Molds with Wear-Resistant Features
Certain design features can help prevent excessive wear. For example, adding venting to the mold design can reduce the pressure on the mold. Flow channels can also be designed to minimize friction. A good mold design takes wear into account and minimizes the stress on high-contact areas.
9. Monitor Temperature and Humidity
Temperature and humidity control is vital for maintaining mold integrity. Fluctuating conditions can cause mold deformation and wear. A Mold Maker will ensure that the mold is used within the optimal temperature and humidity range to avoid unnecessary damage.
Reducing mold wear is crucial for maintaining the quality and efficiency of Electronic Injection Molding. A Mold Maker can design molds that resist wear by selecting the right materials, optimizing cooling, controlling pressure, and applying coatings. Regular maintenance and inspections also play a key role in extending mold life.
By focusing on these strategies, manufacturers can reduce mold wear, cut costs, and improve part quality. In Electronic Injection Molding, minimizing mold wear leads to longer-lasting molds and more consistent, reliable parts. Investing in proper mold care today ensures a smoother production process tomorrow.