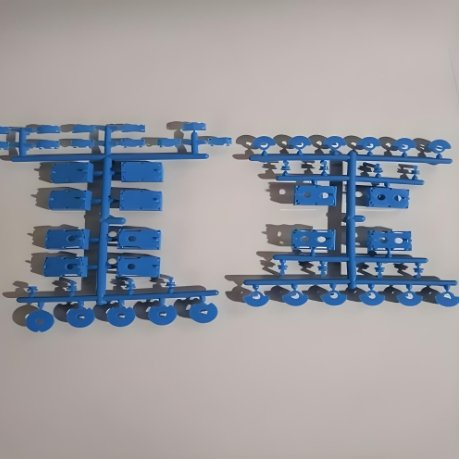
Gate placement is important.
It can make or break the final product.
In Electronic Injection Molding, the gate controls the flow.
It decides where plastic enters the mold.
A good Mold Maker knows this well.
They choose gate positions carefully.
This ensures strong, clean, and accurate parts.
What Is a Gate in Molding?
A gate is a small opening.
It connects the runner to the mold cavity.
Plastic flows through this gate.
Then it fills the part shape.
Once the plastic cools, the gate is trimmed off.
In Electronic Injection Molding, gates are small.
But their placement is a big deal.
It affects flow, strength, and appearance.
Why Gate Placement Matters
The gate is the start point.
It guides how plastic flows inside.
Bad placement causes problems.
Parts may warp.
They may have voids or sink marks.
Or they may be weak.
The Mold Maker must plan carefully.
Each part needs its own gate solution.
This is even more important in electronics.
These parts need tight tolerance.
And a smooth finish.
Common Gate Types Used
There are many gate types.
Each works for different parts.
The Mold Maker picks the best one.
1. Edge Gate
Placed at the side.
Easy to make.
Good for flat parts.
2. Submarine Gate
Hidden under the part.
Good for clean finishes.
Auto-trims during ejection.
3. Pin Gate
Used in hot runner molds.
Very small and precise.
Perfect for Electronic Injection Molding.
4. Fan Gate
Wide gate for large flow.
Used to avoid flow marks.
Each type has pros and cons.
The Mold Maker looks at shape, size, and function.
Gate Placement and Flow Behavior
Plastic flow is key.
It must reach every corner.
It must fill the part evenly.
Bad flow leaves short shots.
It can also trap air.
Or cause weld lines.
The gate should go where flow starts clean.
It should help plastic reach all areas fast.
The Mold Maker simulates flow paths.
They use software to test placement.
Then they choose the best spot.
Avoiding Defects Through Gate Design
Smart gate placement avoids many defects.
Here are common issues and solutions:
1. Warping
Happens when cooling is uneven.
Gate should be placed in thick areas.
This helps even shrinkage.
2. Weld Lines
These are weak spots.
They form where two flow fronts meet.
Gate placement should avoid this.
The Mold Maker adjusts design if needed.
3. Air Traps
Air gets stuck in corners.
Poor gate position causes this.
Air vents help, but gate location matters more.
4. Sink Marks
These appear in thick areas.
Gate should be placed close by.
It ensures good packing pressure.
Importance in Electronic Injection Molding
Electronic parts are small.
They often have tight spaces.
They must be clean and precise.
No flow marks.
No stress spots.
Gate placement affects this.
The Mold Maker must be extra careful.
They often use hot runner systems.
They also use micro gates.
These help maintain part quality.
Working with a Skilled Mold Maker
The Mold Maker does more than build tools.
They study part design.
They look for flow problems.
They test multiple gate positions.
They also run simulations.
They choose the best type and spot.
The Mold Maker may suggest changes.
Maybe the wall is too thin.
Or maybe the gate needs to move.
They work with designers closely.
Their goal is to reduce problems.
And make high-quality parts.
Fast, clean, and strong.
Multiple Gates or Single Gate?
Some parts need more than one gate.
Others need only one.
Use One Gate When:
- The part is small
- Flow path is short
- Surface must be perfect
Use Multiple Gates When:
- The part is big
- Flow needs to be balanced
- Warping is a risk
The Mold Maker tests both.
They pick the best layout.
Balanced flow is key.
Gates must fill the part evenly.
If not, one side cools faster.
This causes defects.
Gate Placement and Cycle Time
Gate position also affects speed.
If flow is fast and smooth, cycle time drops.
If flow is slow or uneven, time increases.
The Mold Maker knows this.
They aim for short cycles.
Without hurting quality.
Less cycle time means lower cost.
It also means faster production.
This is important in Electronic Injection Molding.
Markets move fast.
Production must too.
Cooling and Gate Location
Cooling is important.
Parts shrink as they cool.
Gate placement affects how this happens.
If cooling is uneven, the part warps.
If gate is too far from thick areas, packing fails.
This leads to voids or sink marks.
The Mold Maker places the gate where packing is strongest.
They also design cooling channels around the gate.
This balances heat.
And improves quality.
Gate Removal and Part Finish
After molding, gates are removed.
Some parts need a clean finish.
This is true in electronics.
Sharp marks are not allowed.
They may damage circuits.
So the Mold Maker uses hidden gates.
Like submarine or pin gates.
These leave very small marks.
Some even auto-trim.
This saves time and cost.
And keeps parts clean.
Future of Gate Placement
Technology is improving.
Software now predicts flow better.
AI helps choose gate positions.
3D printing makes test molds fast.
The Mold Maker uses these tools.
They can now test ideas faster.
And make better molds.
In Electronic Injection Molding, this is big.
It helps meet tighter specs.
And keeps quality high.
Gate placement is not simple.
It affects part flow, strength, and appearance.
In Electronic Injection Molding, it’s even more critical.
Parts must be small, clean, and strong.
A skilled Mold Maker ensures this.
They study the part.
They simulate the flow.
They choose the best gate type.
And the best location.
Then they build a mold that works.
With the right gate, defects go down.
Cycle times go down.
Part quality goes up.
If you want better parts, trust your Mold Maker.
They know how to place the gate right.
And that makes all the difference.