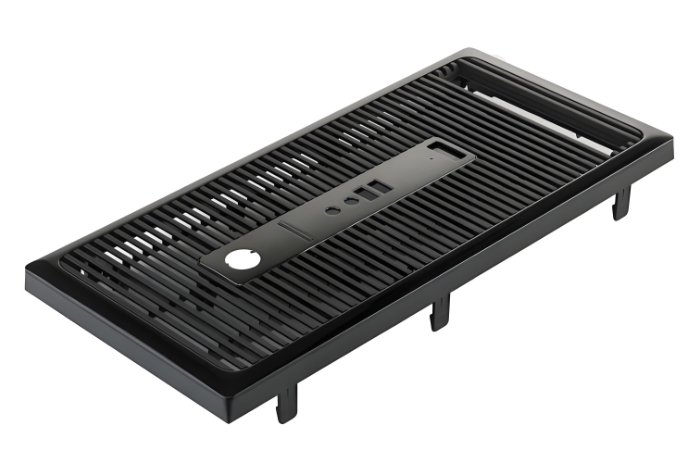
Recycling is no longer a choice.
It is a must.
Electronics create plastic waste.
A lot of it.
But there is hope.
Electronic Injection Molding offers smart solutions.
And the Mold Maker plays a key role.
They help reduce waste.
They support recycling.
They make green production possible.
Let’s see how it works.
Why Recycling Matters in Electronics
Plastic is everywhere in electronics.
In buttons.
In cases.
In connectors.
In clips and covers.
But plastic is not forever.
It takes years to break down.
Most plastic ends up in landfills.
This must stop.
Electronic Injection Molding must go green.
And recycling helps.
It saves plastic.
It saves money.
It protects the planet.
How Recycling Works in Electronic Injection Molding
Recycling in molding means two things:
- Using recycled plastic.
- Reusing scrap material.
Recycled plastic comes from old products.
Bottles.
Broken parts.
Production waste.
This plastic is cleaned.
Shredded.
Melted.
And made into pellets.
These pellets go into injection machines.
They form new parts.
Clean.
Strong.
Reliable.
A skilled Mold Maker designs molds to handle these materials.
That’s how it works.
Role of the Mold Maker in Recycling
The Mold Maker does more than build molds.
They help control waste.
They improve flow.
They adjust the mold to suit recycled plastic.
Why does that matter?
Because recycled plastic acts differently.
It may have more moisture.
It may shrink more.
It may warp.
The Mold Maker knows this.
They plan for it.
They change gate sizes.
They fix cooling channels.
They prevent flash and burn marks.
Their work makes recycling work.
Benefits of Using Recycled Plastic
Recycled plastic has many upsides.
Let’s look at them.
Lower Costs
Virgin plastic costs more.
Recycled plastic is cheaper.
This saves money.
Less Waste
Less scrap.
Less landfill.
More reuse.
Lower Carbon
Less oil.
Less energy.
Greener results.
Better Image
Brands look better when they go green.
Customers notice.
And buy more.
What Materials Are Recyclable?
Not all plastics recycle well.
Some lose strength.
Others discolor.
But many work fine.
Here are common types in Electronic Injection Molding:
- ABS
- PC
- PP
- HIPS
- Nylon
Each has different traits.
The Mold Maker knows how to work with them.
They test flow rates.
They check mold shrinkage.
They prevent errors.
Regrind: Reusing In-House Scrap
Factories make scrap.
Short shots.
Flash.
Start-up waste.
This waste can be reground.
It’s crushed.
Mixed with virgin resin.
And reused.
This is called regrind.
But it must be done right.
Too much regrind weakens the part.
The Mold Maker helps balance it.
They design molds that reduce scrap.
They help test blends.
That saves money.
And keeps quality high.
Challenges in Using Recycled Plastic
Recycling is not easy.
There are risks.
- Weaker material
- Poor surface finish
- Warping
- Burn marks
- Moisture content
The Mold Maker solves these problems.
They adjust the design.
They change flow paths.
They fine-tune venting.
They also suggest pre-drying the resin.
That removes moisture.
And keeps the part strong.
Mold Design for Recycling Success
Recycling needs the right mold.
Not just any mold will do.
The Mold Maker uses smart design:
- Smooth flow channels
- Balanced gates
- Controlled cooling
- Proper venting
They know recycled plastic flows slow.
They avoid sharp corners.
They prevent stress points.
Good design equals good parts.
Even with recycled material.
Machine Setup and Process Controls
Mold alone is not enough.
The machine matters too.
To mold recycled plastic, set up is key.
Use right barrel temps.
Right injection speeds.
Right cooling times.
The Mold Maker helps the techs.
They guide the settings.
They tune the cycle.
This keeps things stable.
And quality high.
Examples of Recycled Parts in Electronics
Many electronic parts now use recycled plastic.
Some examples:
- Battery cases
- TV back covers
- Remote control housings
- Laptop bodies
- Power tool handles
These look and work like new.
But they are greener.
And cheaper.
Thanks to Electronic Injection Molding.
And a great Mold Maker.
Certifications for Recycled Parts
Many clients ask for proof.
They want certified recycled content.
Some useful labels are:
- UL 746D
- ISO 14021
- GRS (Global Recycled Standard)
The Mold Maker helps meet these standards.
They keep records.
They test the results.
They provide data.
This builds trust.
And meets green goals.
Future of Recycling in Molding
Recycling will grow.
More laws will demand it.
More brands will require it.
The molding industry must keep up.
So must the Mold Maker.
They will need:
- New materials knowledge
- Better design tools
- AI to predict flow and warpage
- Smarter mold tech
They must lead.
And adapt fast.
Recycling is the future.
Electronic Injection Molding must go green.
The Mold Maker is key to that journey.
With smart molds.
Good materials.
And clear planning.
We can reduce waste.
Save money.
And protect the earth.
Every molded part matters.
So let’s mold it right.
Let’s mold it green.