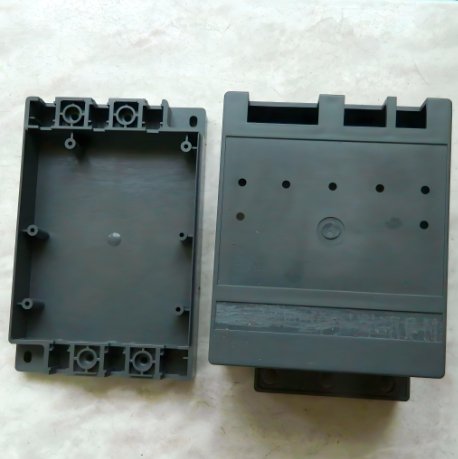
Today, reducing carbon emissions is more important than ever.
Industries are under pressure to become greener.
Electronic Injection Molding is no exception.
This process produces millions of plastic components for electronic devices.
But it also consumes energy and generates waste.
To reduce the carbon footprint, manufacturers need smart solutions.
One key player is the Mold Maker.
Their design choices and technical knowledge can dramatically lower environmental impact.
Let’s explore how Electronic Injection Molding is becoming cleaner and how a skilled Mold Maker helps achieve that goal.
Understanding the Carbon Footprint
Every step in Electronic Injection Molding uses energy.
Raw material production, mold creation, machine operation, and even transportation all add to the carbon footprint.
Electricity consumption is high, especially during long production runs.
Plastic waste, whether from rejects or excess material, adds to environmental harm.
But there’s good news.
Each of these problems can be reduced with proper planning, technology, and a strong partnership with an experienced Mold Maker.
The Role of the Mold Maker in Sustainability
A Mold Maker is more than a tool builder.
They are problem-solvers and efficiency experts.
Their job is to make molds that produce perfect parts, as quickly and cleanly as possible.
How does this reduce the carbon footprint?
Here’s how:
- Faster cycle times mean less machine energy is used per part.
- Reduced scrap rates cut plastic waste and energy loss.
- Smart cooling systems lower the power needed for temperature control.
- Better gate design minimizes material use.
Every choice the Mold Maker makes affects sustainability.
That’s why early collaboration is critical.
Using Energy-Efficient Machines
Modern molding machines are much more energy-efficient.
They use servo motors, smart controllers, and hybrid systems to reduce power use.
Pairing these machines with well-designed molds leads to excellent results.
An expert Mold Maker knows how to design molds that match the machine’s capabilities.
This helps achieve high-quality parts using less energy.
Optimizing Cycle Times
Cycle time is the total time it takes to mold one part.
Longer cycles waste energy.
Shorter cycles save it.
A good Mold Maker focuses on mold cooling, part ejection, and material flow.
These areas are key to speeding up production.
For example, efficient cooling channels remove heat quickly.
This lets the plastic harden faster, shortening the cycle.
In turn, this reduces electricity use and CO₂ emissions.
Material Selection and Waste Reduction
The type of plastic used in Electronic Injection Molding matters.
Some materials require high heat, which consumes more energy.
Others can be processed at lower temperatures, saving energy and reducing emissions.
The Mold Maker helps match the best material to each part.
They also design for minimal waste.
This includes:
- Proper gate sizing to reduce runner waste
- Balanced flow paths to prevent short shots
- Features that allow for easy demolding
Less waste means less regrinding, less reprocessing, and lower energy use overall.
Recycled Materials for a Lower Footprint
Using recycled plastic is a powerful way to lower carbon emissions.
It takes less energy to produce than virgin plastic.
It also helps reduce landfill waste.
However, recycled plastic behaves differently during molding.
The Mold Maker must adapt the mold design to handle these changes.
This might mean adding special vents, flow aids, or adjusting wall thickness.
When done right, recycled materials work just as well as new ones—while lowering the carbon footprint.
Temperature Control for Energy Savings
Temperature control is critical in Electronic Injection Molding.
Machines must heat plastic and keep molds at steady temperatures.
This uses a lot of energy.
Smart temperature management reduces energy waste.
A skilled Mold Maker helps by designing molds with optimized cooling systems.
These include:
- Water lines placed close to the part
- Baffles and bubblers to improve flow
- Insulated mold plates to retain heat
The result is faster cycles and lower energy use.
Lightweighting and Design Efficiency
Making parts lighter reduces the amount of plastic used.
It also shortens cycle time and cuts energy use.
But this must be done carefully.
The parts still need to meet strength and function requirements.
Here, the Mold Maker works closely with designers.
They suggest structural ribs, thinner walls, and smarter geometry.
These changes reduce weight without lowering quality.
In Electronic Injection Molding, this is especially useful for battery cases, connectors, and covers.
Automation and Process Control
Automated systems improve repeatability and reduce human error.
They also make it easier to monitor energy usage.
When molds are designed with automation in mind, the whole process becomes smoother.
The Mold Maker includes features like:
- Self-aligning guides
- Mold sensors
- Ejection systems that work with robots
These features help the factory run with less downtime and lower waste.
Transport and Logistics
Carbon footprint doesn’t stop at the factory.
It also includes transporting raw materials and finished parts.
Mold design can help here too.
For example:
- Nesting parts to save space
- Designing stackable products
- Creating multi-cavity molds for fewer shipments
By working with the Mold Maker early, companies can reduce their overall footprint from end to end.
Real-World Examples
Some top electronics companies are already using these strategies.
- A smartphone manufacturer switched to recycled PC for internal parts.
The Mold Maker redesigned the mold to handle the new flow behavior.
Emissions dropped by 30%. - An electronics brand added optimized cooling lines to molds.
This cut cycle time by 15% and saved thousands in electricity. - A home electronics supplier introduced lightweight speaker casings.
The Mold Maker used flow simulation to perfect the design.
Material usage and emissions both dropped.
Sustainability in Electronic Injection Molding is not only possible.
It’s essential.
By working closely with a skilled Mold Maker, manufacturers can lower energy use, reduce waste, and improve product design.
Together, they can shrink the carbon footprint of electronics—one part at a time.
The journey to sustainability begins with smart decisions.
It begins with design.
And it begins with the Mold Maker.
Would you like to turn this article into a white paper or infographic to share with customers or partners?