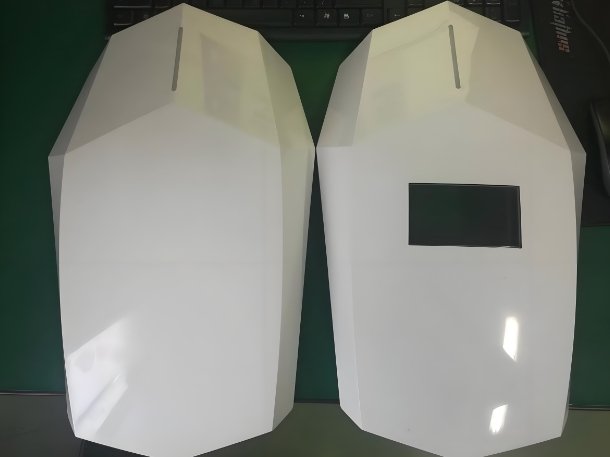
Environmental safety and product quality are top concerns in today’s electronics manufacturing world.
As electronic devices become more widespread, so do the rules that govern how they are made.
For those in Electronic Injection Molding, meeting strict environmental standards is no longer optional.
It is a requirement.
And it starts with the materials used and the people who shape them—the Mold Maker.
One of the most important regulations in this space is the RoHS directive.
This law, along with lead-free manufacturing practices, is changing the way plastic parts are made for electronic products.
In this article, we will explain what lead-free and RoHS-compliant Electronic Injection Molding means, why it matters, and how Mold Makers can support this essential shift in manufacturing.
What Is RoHS?
RoHS stands for Restriction of Hazardous Substances.
It is a European Union directive that limits the use of harmful materials in electrical and electronic equipment.
This includes substances like:
- Lead
- Mercury
- Cadmium
- Hexavalent chromium
- PBB and PBDE flame retardants
These materials are known to be harmful to both people and the environment.
RoHS forces manufacturers to find safer alternatives.
For Electronic Injection Molding, this means using materials and processes that avoid restricted substances.
The Mold Maker plays a critical role in supporting this.
Why Lead-Free Matters in Electronic Injection Molding
Lead has long been used in electronics for soldering and stabilization.
However, it poses serious health risks.
Lead can cause brain damage and organ failure when it accumulates in the body.
For workers and end users, this risk is unacceptable.
Going lead-free isn’t just about meeting regulations.
It’s about protecting lives.
When Electronic Injection Molding adopts lead-free materials, it creates safer products for homes, schools, hospitals, and industries.
A skilled Mold Maker helps ensure this process works smoothly.
They select compatible materials, adjust mold design for better flow, and avoid contamination during production.
How RoHS Compliance Affects Electronic Injection Molding
RoHS compliance goes beyond just avoiding lead.
It impacts the entire Electronic Injection Molding workflow.
From material selection to production processes, every step must be clean and compliant.
Molding compounds must be carefully chosen.
They must not only be free of banned substances, but also compatible with electronic functions like insulation and heat resistance.
This limits the range of materials available, requiring the Mold Maker to adapt.
For example, certain flame retardants once common in electronics are now banned.
This means the Mold Maker must design parts that meet safety codes using different materials.
Sometimes, this involves creating new mold features or testing new plastic blends.
The Role of the Mold Maker in Ensuring Compliance
A good Mold Maker is key to successful, RoHS-compliant Electronic Injection Molding.
Here’s how they help:
1. Material Knowledge
The Mold Maker understands which materials meet RoHS rules.
They help select plastics that are safe, stable, and easy to mold.
2. Contamination Control
Even trace amounts of lead or other banned substances can cause a product to fail RoHS testing.
A professional Mold Maker keeps molds, machines, and tools clean and dedicated to RoHS projects.
3. Design Adjustments
RoHS-compliant materials sometimes behave differently.
They may flow slower, shrink more, or require different mold temperatures.
The Mold Maker adjusts the mold to ensure smooth filling, tight tolerances, and reliable part performance.
4. Documentation and Testing
To meet global standards, documentation is critical.
A Mold Maker who understands compliance will support traceability and testing requirements, giving clients confidence.
Business Benefits of Going RoHS-Compliant
Complying with RoHS and going lead-free isn’t just about safety.
It’s also good business.
1. Access to Global Markets
Many countries now require RoHS compliance.
If your electronic parts don’t meet these standards, you can’t sell them in those markets.
Electronic Injection Molding companies that follow these rules can expand their reach.
2. Improved Brand Image
Customers care about the environment.
They want products that are safe and sustainable.
RoHS-compliant manufacturing shows you care too.
3. Reduced Legal Risk
Non-compliance can lead to product recalls, legal penalties, and brand damage.
Following RoHS rules with help from a trusted Mold Maker helps prevent these risks.
4. Innovation Opportunities
RoHS pushes manufacturers to explore new materials and technologies.
This drives innovation and improves product performance.
Examples in Practice
Many companies have already made the switch.
- A major electronics brand redesigned its computer power supply cases using RoHS-compliant polycarbonate.
Their Mold Maker helped adjust the cooling system and gate placement to suit the new material.
The parts passed testing with flying colors. - A medical device company replaced a lead-based plastic with a high-temp RoHS-safe alternative.
The Mold Maker redesigned the mold to allow better venting.
The result was a safer, compliant product ready for European and U.S. markets.
These examples show how important the Mold Maker is to every step of Electronic Injection Molding.
The Future of Safe Electronics
As technology advances, regulations will likely become stricter.
RoHS has already seen updates, and more are on the way.
This means manufacturers must stay ahead of the curve.
Electronic Injection Molding teams that invest in clean, safe processes will have a major advantage.
So will Mold Makers who understand how to support those goals.
Training, testing, and collaboration will be key.
Working with partners who care about compliance will become the industry standard.
Lead-free and RoHS-compliant Electronic Injection Molding is more than just a trend.
It is a responsibility.
It protects health, meets global regulations, and builds trust with customers.
A skilled Mold Maker plays a central role in this process.
From selecting safe materials to designing clean molds, they ensure every part meets the highest standards.
The future of electronics is green, safe, and precise.
And it all starts with smart Electronic Injection Molding—and the right Mold Maker.