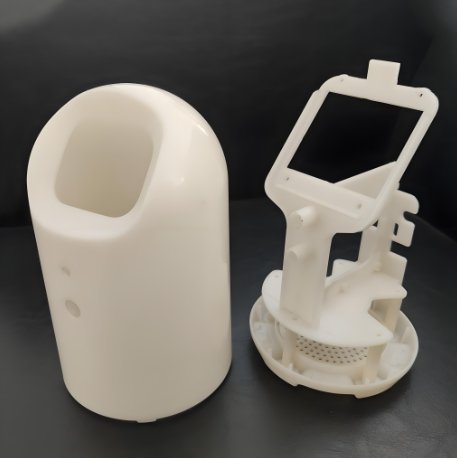
Today, the plastics industry faces two major challenges. One is the growing demand for complex electronic parts. The other is the urgent need for sustainable manufacturing. In response, smart manufacturing is changing the way we approach Electronic Injection Molding. This shift not only boosts productivity but also helps reduce waste and lower carbon emissions. Every experienced Mold Maker plays an important role in making this transformation possible.
In this article, we will explore how smart manufacturing supports green production in Electronic Injection Molding. We will also show how the Mold Maker helps make the process smarter and cleaner.
What Is Smart Manufacturing?
Smart manufacturing uses advanced technologies to optimize factory operations. It includes sensors, artificial intelligence, machine learning, cloud computing, and real-time data analytics. These tools give manufacturers more control, visibility, and flexibility.
In the context of Electronic Injection Molding, smart systems allow companies to monitor mold performance, machine energy use, and material waste. With these insights, they can improve efficiency and reduce environmental impact.
The Link Between Smart Manufacturing and Sustainability
Smart manufacturing supports sustainability in many ways. First, it helps reduce energy consumption. Machines can adjust power use automatically based on production needs. This prevents energy waste.
Second, smart systems track material use in real time. If too much plastic is being used, the system can alert the team. This reduces scrap and improves part quality. It also saves money.
Third, predictive maintenance helps machines stay in top condition. When machines are well maintained, they produce fewer defective parts. This leads to less rework and less waste.
Every one of these benefits helps make Electronic Injection Molding more sustainable. The Mold Maker supports these goals by designing efficient, high-quality tools that work well with smart systems.
The Role of the Mold Maker in Smart, Green Molding
A smart system is only as good as the mold it runs. That’s why the Mold Maker is critical to smart manufacturing. The Mold Maker designs and builds precision tools that allow machines to produce parts quickly and with minimal waste.
Here’s how the Mold Maker contributes to smart, green Electronic Injection Molding:
1. Efficient Mold Design
Smart factories use high-speed data collection to study how plastic flows inside the mold. A skilled Mold Maker can use this data to redesign gates, runners, and cooling channels. These changes help reduce cycle times and energy use.
2. Material Optimization
The Mold Maker works closely with engineers to choose eco-friendly plastics. This includes biodegradable, recycled, or lightweight materials. Molds must be adjusted to handle these materials without causing defects. Smart systems then track how well they perform in production.
3. Digital Mold Monitoring
Many molds now include built-in sensors. These sensors track pressure, temperature, and filling speed. A good Mold Maker ensures that these features are part of the tool design. Smart data from the mold helps factories respond quickly to problems, saving time and material.
4. Compatibility with Automation
Smart factories often include robotic part removal, trimming, and packaging. Molds must support this. The Mold Maker ensures the part can be ejected easily and that robotic arms have access. This boosts efficiency and lowers labor costs.
Real-Time Data: Reducing Waste at Every Step
Data is the heart of smart manufacturing. For Electronic Injection Molding, it means better decisions and less waste. Machines collect thousands of data points every second. These include mold temperature, injection pressure, cooling time, and part weight.
If something goes wrong, the system knows immediately. It can stop the machine, alert the operator, or adjust settings. This prevents long runs of defective parts. It also reduces rework and material waste.
When the Mold Maker builds a mold that works smoothly with sensors and software, the factory gains speed and quality. That’s the smart way to do green manufacturing.
Predictive Maintenance: Less Downtime, More Efficiency
Old systems break down without warning. Smart systems predict failures before they happen. Sensors in machines and molds track vibration, temperature, and cycle counts. When something starts to go wrong, maintenance teams get alerts.
This is good for sustainability. A broken machine can waste hours of production. Worse, it may create defective parts. Predictive maintenance keeps equipment running at peak performance. That means lower energy use, fewer rejects, and better part quality.
Again, the Mold Maker supports this by designing durable tools. They also choose strong materials and easy-to-maintain features, which match the smart system’s goals.
Energy Monitoring: Smarter Use of Power
Electronic Injection Molding machines use a lot of electricity. Smart manufacturing helps manage this. Energy meters track how much power each machine uses. If a machine is using more than normal, the system flags it.
This lets teams fix problems fast. For example, if a mold’s cooling system is clogged, the machine may overheat and waste energy. The smart system finds the issue, and the Mold Maker can help adjust the tool to fix it.
By reducing energy waste, smart manufacturing lowers the carbon footprint of each molded part.
Examples of Smart Green Molding in Practice
Let’s look at a few real examples:
- A mobile phone company uses smart molding to make cases from recycled ABS. The system adjusts injection pressure for every shot. Their Mold Maker designed a special gate to avoid air traps. They now produce 10,000 cases per day with near-zero defects.
- A lighting manufacturer uses sensors in the mold to track cavity pressure. When the pressure drops, it means a part may be short. The machine stops and alerts the team. Their Mold Maker helped add these sensors into the core steel. They cut waste by 40%.
- A medical device firm switched to bioplastics. The materials required different cooling rates. The Mold Maker added baffles to control flow. The smart system adjusted coolant flow automatically. The result: faster cycles and green production.
These examples show how smart systems and skilled Mold Makers work together.
Looking to the Future
Smart manufacturing is growing fast. In the next few years, more Electronic Injection Molding companies will adopt it. Governments and customers are demanding cleaner, greener products. Smart systems help companies meet these demands without sacrificing quality.
The Mold Maker will remain a key part of this future. As tools become more advanced, their skill in mold design, material science, and sensor integration will be in even higher demand.
Smart manufacturing is reshaping Electronic Injection Molding. It reduces energy, lowers waste, and improves product quality. These changes help protect the planet while saving money.
Behind every smart factory is a smart mold. And behind every smart mold is a skilled Mold Maker.
By working together, we can create a cleaner future—one injection-molded part at a time.