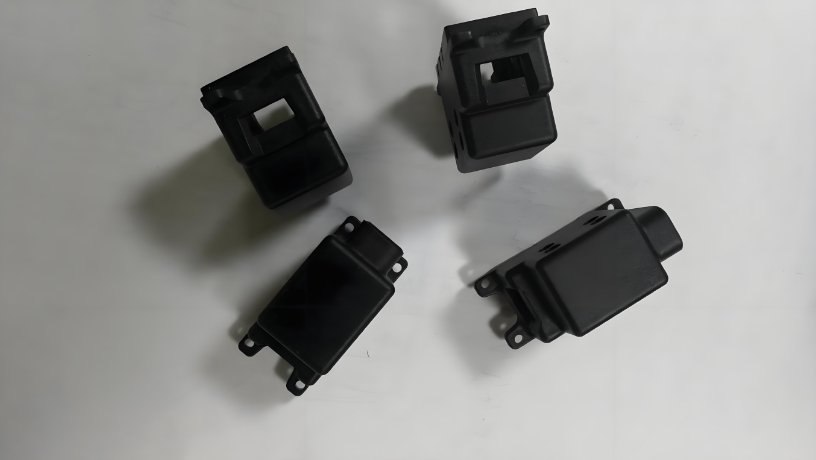
Augmented Reality (AR) is reshaping how we approach mold design in the field of Electronic Injection Molding. By overlaying digital information onto real-world environments, AR gives engineers and every Mold Maker a powerful new tool to visualize, refine, and improve molds before physical production begins.
This transformation is not just about futuristic visuals. It’s about better decision-making, faster development, and fewer errors. In the competitive world of electronics manufacturing, even small gains in time or accuracy can lead to big savings.
The Basics of AR in Manufacturing
AR combines virtual content with real-world settings. Unlike Virtual Reality (VR), which creates a fully digital space, AR blends digital models with the actual workspace. You can see 3D models of mold parts on your desk, overlay design details on real equipment, or even test assembly simulations in real-time using just a tablet or AR glasses.
In Electronic Injection Molding, where tiny design flaws can cause product failure, this technology is proving invaluable. It allows each Mold Maker to inspect mold designs from multiple angles and make quick changes without building a prototype.
AR in the Mold Design Phase
The first major benefit of AR comes during the early mold design stage. Here, AR helps teams visualize 3D CAD models in physical space. Designers and engineers can explore how molten plastic will flow, how cooling systems will behave, and whether the ejection mechanism is optimized—all before cutting any steel.
This allows for quicker collaboration between design teams and the Mold Maker. Instead of relying only on computer screens or paper drawings, AR allows life-size, real-time interaction with the proposed mold.
Mistakes that could lead to costly delays in Electronic Injection Molding are spotted early. A gate position may look fine on a 2D plan, but when viewed in AR, the flow imbalance becomes clear. Vent locations, parting lines, and lifter functions all become more intuitive to analyze.
Improving Collaboration Across Teams
Mold design isn’t done in isolation. It often involves product designers, engineers, toolmakers, and quality control specialists. With AR, all parties can view the same 3D model in real-time—even if they are in different locations.
This brings a new level of clarity and agreement during mold development. A Mold Maker can show a customer the actual fit of the mold in a virtual molding machine. The customer can suggest changes and see the effect immediately.
In Electronic Injection Molding, where tolerances are tight and demand is high, this shared understanding reduces miscommunication. The result is a mold that works right the first time.
AR for Training New Mold Makers
Training a new Mold Maker is a time-intensive process. It often takes years of experience to understand the nuances of mold structure, parting lines, ejector pins, and cooling channels. AR can speed up this learning process.
AR-based training modules allow apprentices to view interactive molds in 3D. They can disassemble components virtually and see how each part functions. They can test simulations to see how materials flow, where defects might appear, and how to adjust the design.
This gives new Mold Maker talent a hands-on learning experience, helping them grasp complex ideas much faster. In the field of Electronic Injection Molding, where precision is critical, faster learning translates into better performance and fewer errors.
Speeding Up Design Changes
Modifying a mold after fabrication is both expensive and time-consuming. AR helps reduce these costly mistakes by catching problems early. If a customer wants to change a connector position or add ventilation holes, AR can show how those changes affect the mold’s structure in real time.
The Mold Maker can adjust the virtual design, show the updated geometry using AR, and get feedback instantly. If changes are approved, final tooling can proceed with confidence.
This rapid revision loop is essential in Electronic Injection Molding, where product life cycles are short, and speed to market matters.
Predicting and Preventing Mold Failures
One of the most critical uses of AR is predicting how molds might fail during production. AR can simulate mold operation and show areas of high stress, heat build-up, or flow imbalances. These simulations help each Mold Maker optimize the tool’s strength, cooling, and material flow.
By highlighting weak zones or poor ejection paths, AR helps avoid real-world failures. These insights help mold designers improve part quality, reduce waste, and extend tool life.
In Electronic Injection Molding, where part reliability is non-negotiable, this predictive capability is a game-changer.
Supporting Maintenance and Mold Repairs
AR is not just helpful in design—it also supports ongoing mold maintenance. Using AR, technicians can overlay service manuals, repair guides, and mold breakdowns onto the actual mold in real space. This simplifies disassembly, part replacement, and reassembly.
A Mold Maker can wear AR glasses and receive step-by-step guidance on how to repair a core pin or clean a cooling line. This reduces downtime and ensures repairs are done correctly.
In high-volume Electronic Injection Molding lines, even one hour of downtime can mean lost revenue. AR speeds up maintenance and helps keep production running smoothly.
Cost and Accessibility
In the past, AR seemed expensive and complicated. Today, the technology is much more accessible. Many AR tools run on smartphones, tablets, or affordable headsets. The return on investment comes quickly through time savings, fewer design errors, and reduced rework costs.
More Mold Maker shops are adding AR to their toolkit. They use it not just for design, but also for customer presentations, mold testing, and process optimization.
For companies involved in Electronic Injection Molding, AR is quickly becoming a standard tool, not a luxury.
A New Era for the Modern Mold Maker
The rise of AR represents a shift in how molds are designed, tested, and built. It blends digital power with physical expertise. It allows the Mold Maker to visualize complex geometry with ease and adjust designs before they become expensive problems.
In Electronic Injection Molding, where every micrometer counts, AR gives designers and toolmakers a huge advantage. It promotes better communication, smarter decisions, and faster time to market.
Augmented Reality is more than just a tech trend. It’s a practical tool for improving mold design, especially in Electronic Injection Molding. It helps every Mold Maker work smarter, reduce errors, and deliver better tools, faster.
As electronics continue to shrink and evolve, the molds used to make them must become more precise and reliable. AR is a powerful way to meet these demands. It creates a direct link between imagination and execution, turning digital ideas into real-world success.
Would you like this article turned into a presentation or infographic for your team?