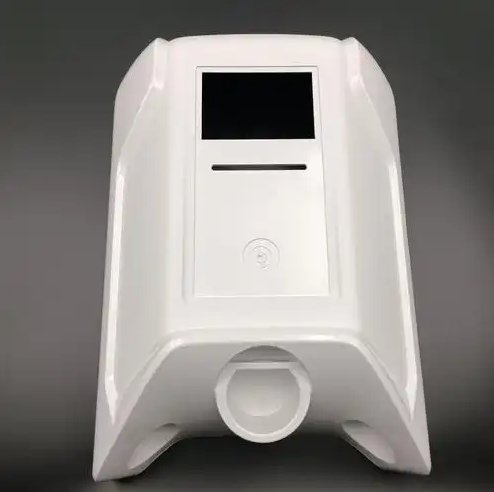
The world of electronics is changing fast. Devices are becoming smarter, smaller, and more energy-efficient. This shift is creating demand for new materials that support these innovations. One material group leading the way is conductive plastics. These plastics can carry electrical current, opening new possibilities in Electronic Injection Molding.
For every Mold Maker, understanding these materials is no longer optional. It is essential for staying competitive in today’s high-tech manufacturing landscape. In this article, we explore how the next generation of conductive plastics is shaping the future of Electronic Injection Molding, and what this means for mold design, production, and product performance.
What Are Conductive Plastics?
Conductive plastics are polymers that allow electricity to flow through them. Normally, plastics are insulators. But by adding carbon fibers, metal particles, or carbon nanotubes, their structure changes. These additives turn ordinary polymers into materials with electrical conductivity.
In Electronic Injection Molding, conductive plastics are used to replace metal parts. They are lighter, corrosion-resistant, and easier to mold into complex shapes. They also cut down on the number of assembly steps, which saves time and cost.
Why Conductive Plastics Matter for Electronics
Lightweight and Compact Design
One of the biggest advantages of conductive plastics is weight reduction. Many electronic devices—like laptops, sensors, and medical devices—must be small and portable. Replacing metal shielding and connectors with conductive plastics makes the product lighter and easier to manufacture.
In Electronic Injection Molding, this shift gives engineers more freedom in design. It also allows for parts to be integrated rather than assembled in multiple steps.
Lower Manufacturing Costs
Metal parts often require secondary machining, plating, or welding. These steps add to the cost and time of production. Conductive plastics eliminate many of these steps. They can be molded in a single cycle using a well-designed mold. This is where the Mold Maker plays a key role.
By designing molds that handle conductive plastic properties, the Mold Maker helps reduce cycle times and material waste. The result is faster, cheaper, and more efficient production.
EMI/RFI Shielding
Electromagnetic interference (EMI) and radio frequency interference (RFI) are serious issues in electronic design. Devices must be shielded from outside signals to prevent data errors or failure.
Conductive plastics offer EMI/RFI shielding directly from the material. This is especially useful in Electronic Injection Molding for casings, housings, and connectors. With proper mold design, these plastics can deliver seamless shielding and reduce the need for extra coatings or layers.
Innovations in Conductive Plastic Technology
Carbon Nanotube Fillers
New conductive plastics use carbon nanotubes (CNTs) to improve conductivity without compromising mechanical strength. CNTs offer a balance of electrical performance and durability.
In Electronic Injection Molding, this innovation allows for thinner walls and more delicate structures. The Mold Maker must consider flow rates, shear stress, and filler orientation to design an effective mold for CNT-based plastics.
Graphene-Enhanced Polymers
Graphene is another advanced filler being added to conductive plastics. It delivers even better conductivity and thermal performance. Devices that generate heat—like batteries or processors—can benefit from graphene-filled plastics.
The Mold Maker working with these materials needs to optimize gate placement and cooling to ensure part quality and performance.
Hybrid Conductive Compounds
Some compounds now combine metals and carbon-based fillers. These materials give consistent conductivity and better molding flow. This development expands applications in automotive electronics, medical tech, and smart devices.
In Electronic Injection Molding, these hybrid materials offer a middle ground between full-metal and traditional polymer parts. The Mold Maker must adapt to each compound’s behavior to achieve the best results.
Applications in the Electronics Industry
Consumer Devices
Conductive plastics are used in laptops, tablets, phones, and headphones. They offer lightweight shielding, grounding paths, and heat management. Their flexibility allows more ergonomic and compact designs.
Automotive Electronics
Cars use more electronics than ever. From ADAS to infotainment systems, all require shielding and durability. Conductive plastics molded with high precision ensure consistent protection without adding weight.
Medical Electronics
Wearable and portable medical devices need biocompatible, lightweight materials. Conductive plastics allow these devices to stay small, safe, and functional. Electronic Injection Molding delivers these parts at high speed and low cost.
Industrial and Networking Equipment
Connectors, housings, and switches in routers, servers, and industrial controls benefit from the conductivity and thermal properties of these plastics. They also reduce assembly steps, making them ideal for high-volume production.
Challenges in Molding Conductive Plastics
Flow Characteristics
Conductive fillers can affect how plastic flows. High filler content may lead to uneven flow, short shots, or warping. The Mold Maker must carefully analyze part geometry and gate location.
Tool Wear
Abrasive fillers like metal particles or carbon fibers can wear down mold surfaces. This means the Mold Maker must use hardened steels and coatings to protect the mold.
Surface Finish
Conductive plastics often produce rougher finishes due to fillers. Secondary polishing may be needed depending on the application. The Mold Maker can design molds to reduce these effects by adjusting cavity texture or venting.
The Future of Conductive Plastics in Injection Molding
The role of conductive plastics will only grow. As 5G, IoT, electric vehicles, and AI devices expand, the demand for compact, efficient electronics will increase. That means more projects using Electronic Injection Molding with high-performance materials.
Mold Maker teams that can design for conductive plastics will lead this wave. They’ll deliver innovative, cost-effective, and scalable solutions for industries everywhere.
We also expect to see:
- Wider use of recyclable conductive plastics
- Growth in cleanroom molding for medical and high-end electronics
- Smarter molding machines using AI to adapt to conductive compounds
- 3D-printed molds to speed up development with complex conductive parts
Conductive plastics are driving a revolution in Electronic Injection Molding. These materials replace metals while offering electrical performance, light weight, and faster production. For every Mold Maker, adapting to this trend is essential.
Success with conductive plastics depends on deep understanding of the material, careful mold design, and process control. As technology advances, so too must our approach to molding. The next generation of conductive plastics is here—and the future is being molded now.