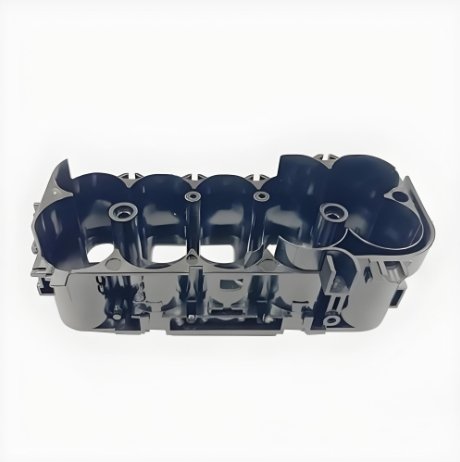
Today, electronic devices are everywhere. We carry smartphones, smartwatches, earbuds, and fitness trackers with us all the time. Many of these devices must survive rain, sweat, spills, and even total submersion. Because of this, waterproofing has become a major goal for manufacturers.
One of the best ways to improve waterproofing is by using Electronic Injection Molding. This process, combined with the skills of a great Mold Maker, helps create tight, protective shells around delicate electronic parts. Let’s explore how this works and why it is so important.
Why Waterproofing Matters in Electronics
Water is one of the biggest enemies of electronics. A single drop can short-circuit a delicate board, corrode a metal contact, or cause major failures. Waterproofing protects devices and extends their life.
Without good protection, even high-end electronics can fail after minor exposure to moisture. That’s why smart companies now rely on Electronic Injection Molding and experienced Mold Maker teams to build strong, water-resistant enclosures.
Waterproof electronics are important for:
- Outdoor devices like GPS trackers
- Medical electronics like health monitors
- Consumer gadgets like phones and earbuds
- Industrial tools exposed to harsh conditions
Good waterproofing adds safety, reliability, and customer satisfaction.
How Electronic Injection Molding Helps Waterproofing
Electronic Injection Molding is a manufacturing process where molten plastic is injected into a mold cavity. Once cooled, it forms a solid, detailed part. In waterproof electronics, this molded part acts as a strong shield around sensitive internal parts.
Here’s how Electronic Injection Molding boosts waterproofing:
1. Seamless Designs
Traditional products are made from separate parts snapped or screwed together. Gaps between parts are weak points where water can sneak in.
Electronic Injection Molding allows making seamless housings that have no gaps. A talented Mold Maker designs molds that produce parts with complex shapes and perfect fits, locking out water completely.
2. Integrated Gaskets
In some cases, soft, flexible materials are molded directly onto hard shells to create built-in gaskets. This two-shot molding technique gives an extra waterproof seal without needing separate O-rings or adhesives.
A skilled Mold Maker ensures perfect bonding between hard and soft materials to guarantee leak-proof performance.
3. Tight Tolerances
Waterproof devices need tight fits. Even a tiny gap can cause leaks. Electronic Injection Molding can produce parts with extremely tight tolerances, ensuring perfect closures every time.
Precision from the Mold Maker is critical here. The mold must be designed and built with incredible care to keep every edge sharp and every surface smooth.
4. Overmolding Sensitive Parts
Sometimes, Electronic Injection Molding is used to completely cover sensitive components with protective plastic layers. This method is called overmolding. It creates a complete barrier that blocks out moisture, dust, and dirt.
Overmolding is ideal for connectors, sensors, and small assemblies that need full protection.
The Role of the Mold Maker in Waterproofing
When it comes to waterproofing, the Mold Maker has one of the most important jobs. Good waterproofing depends on good mold design and excellent craftsmanship.
A Mold Maker must:
- Design molds that avoid weak spots and gaps
- Choose the right materials for strength and sealing
- Create complex parting lines that still keep a tight seal
- Plan vents and gates to avoid air bubbles or weld lines
- Test and refine the molds to ensure perfect parts
Without careful work at every step, waterproofing will fail. That’s why companies that value reliability trust only the best Mold Maker teams for their Electronic Injection Molding projects.
Materials for Waterproof Electronic Injection Molding
Choosing the right materials is also important for waterproofing success. Some plastics and rubbers resist water better than others.
Common choices include:
- Polycarbonate (PC)
- Acrylonitrile Butadiene Styrene (ABS)
- Thermoplastic Polyurethane (TPU)
- Liquid Silicone Rubber (LSR)
- Nylon (PA)
These materials are tough, resist chemicals, and can survive a wide range of temperatures. A good Mold Maker knows how to handle each material correctly to maximize waterproofing.
Testing for Waterproofing
Building waterproof devices isn’t enough. Companies must also test them to make sure they work as expected. Common waterproofing tests include:
- IP Rating Tests (Ingress Protection, like IP67 or IP68)
- Water Submersion Tests
- Spray and Splash Tests
- Humidity Chamber Tests
- Pressure Water Jet Tests
Devices that pass these tests earn trusted ratings. Consumers know they can depend on these products even in wet conditions.
Without high-quality Electronic Injection Molding and skilled Mold Maker work, passing these tests would be almost impossible.
Future Trends in Waterproofing with Electronic Injection Molding
Waterproofing will only become more important as electronics become more wearable, portable, and embedded in daily life.
Some future trends include:
- Smaller, more complex designs: Waterproofing must happen in even tighter spaces.
- New, advanced materials: Plastics and elastomers will keep improving.
- More eco-friendly materials: Bioplastics that still resist water are on the rise.
- Smarter molds: Molds will include sensors to track temperature, pressure, and cycle times automatically.
Mold Makers who stay ahead of these trends will be key players in the next generation of Electronic Injection Molding.
Waterproofing is no longer an optional feature—it’s a must-have for modern electronics. From smartwatches to medical monitors, devices must survive moisture, splashes, and even full submersion.
Thanks to Electronic Injection Molding and the skills of a great Mold Maker, manufacturers can create strong, beautiful, and waterproof parts. Seamless designs, integrated seals, and tight tolerances are all possible with the right molding techniques.
As technology keeps advancing, the demand for waterproof electronic devices will grow. Companies that invest in excellent Electronic Injection Molding and top-quality Mold Maker services will lead the way, delivering products that customers can trust, no matter the conditions.