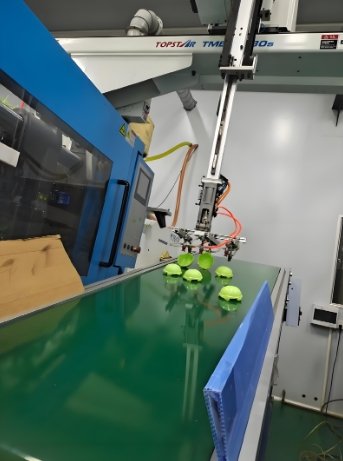
High-end audio equipment is no longer just about sound. Today, premium design, durable construction, and functional beauty matter just as much as clear audio. Whether it’s headphones, speakers, amplifiers, or control units, consumers want devices that look sharp and feel premium in their hands.
This is where Electronic Injection Molding and a skilled Mold Maker become key. These technologies and crafts not only shape the outer form but also protect the sensitive inner components and enhance the user experience.
In this article, we’ll explore how Electronic Injection Molding is shaping the future of high-end audio—and why every great design starts with a great Mold Maker.
What is Electronic Injection Molding?
Electronic Injection Molding is a process used to form plastic components for electronic devices. It involves heating plastic pellets and injecting them into a mold where they cool and harden into a precise shape.
In high-end audio gear, this process is used for:
- Speaker housings
- Headphone shells
- Volume knobs and buttons
- Amplifier cases
- Audio jack surrounds
- Internal brackets and supports
Because audio equipment must be both functional and attractive, Electronic Injection Molding helps deliver tight tolerances, stylish surfaces, and sturdy forms.
The Importance of a Skilled Mold Maker
Behind every perfect molded part is a talented Mold Maker. The Mold Maker designs and builds the steel molds that shape the plastic. They ensure that every detail—curves, holes, textures, finishes—is transferred exactly onto the plastic part.
In high-end audio products, precision matters a lot. Even a small shift in mold alignment or texture can affect how parts fit together, how sound travels, or how the product feels to the touch.
That’s why the partnership between Electronic Injection Molding experts and a great Mold Maker is essential.
Sound Quality Starts With Smart Housing Design
One of the biggest challenges in audio equipment is managing vibrations and resonance. The housing must:
- Support internal components
- Prevent vibration distortion
- Direct sound properly
- Stay rigid under load
Through Electronic Injection Molding, engineers can design enclosures that meet these acoustic demands while still looking sleek.
The Mold Maker then ensures the mold is built to bring this acoustic-focused design to life. This may include shaping inner sound channels, adding air vents, or thickening certain areas to prevent buzz.
Advanced Materials for High-End Audio
Today’s audio manufacturers often use special plastic blends to improve sound or durability. These include:
- Glass-filled polycarbonate: Offers added strength and vibration control
- ABS-PC blends: For sleek looks and toughness
- Conductive plastics: To reduce static interference
- Soft-touch elastomers: For a luxury hand-feel
Electronic Injection Molding handles these materials well, but each one needs its own mold setup. The Mold Maker must match the mold’s cooling, flow paths, and venting to the specific resin used.
Finishing Touches: Style and Brand Identity
High-end customers care about looks. Whether it’s matte black for stealthy speakers or metallic accents on studio headphones, surface finish plays a major role.
Electronic Injection Molding allows for different textures, gloss levels, and even patterns. The Mold Maker handles this by treating the mold’s surface. That can include:
- Polishing for high-gloss
- Etching for matte or grained surfaces
- In-mold textures for leather-like or brushed finishes
For audio brands, this level of detail builds identity. The molded part becomes not just a shell but part of the brand’s voice.
Protecting Electronics from Damage
High-end audio gear includes delicate circuits and drivers. The enclosure must protect them from:
- Dust
- Moisture
- Drops and impact
- Temperature changes
Using Electronic Injection Molding, manufacturers create snug, sealed enclosures with minimal gaps or weak points. In some cases, overmolding is used to combine two materials—such as a hard shell with a soft rubber seal.
Again, the Mold Maker makes this possible by designing the mold to allow for perfect seals and double-shot injection molding where needed.
Cost-Effective Small Batch Production
Many high-end audio companies produce in smaller batches compared to mass-market brands. They often focus on boutique runs or custom models.
Electronic Injection Molding is perfect for this when combined with quick-turn tooling or aluminum molds. A skilled Mold Maker can build such molds faster and more affordably, allowing companies to move from prototype to product quickly.
This flexibility allows audio startups and niche brands to innovate without massive upfront costs.
The Move Toward Sustainability
Consumers today also want eco-friendly products. With Electronic Injection Molding, manufacturers can use:
- Recycled plastics
- Biodegradable materials
- Energy-efficient molding machines
A Mold Maker who understands sustainability can reduce waste in the mold design and optimize cycle times to lower energy use.
Customization and Personalization
Some high-end audio makers offer personalized products—custom colors, names engraved, or unique designs.
Through Electronic Injection Molding and the right Mold Maker, this is now possible. Using interchangeable mold inserts or modular tooling, different looks can be made from the same base mold.
This lowers cost while offering the premium feel customers want.
The Future of Audio Equipment Molding
As audio devices become smarter and more connected, new challenges will arise. Devices will need more sensors, wireless modules, and interfaces. Molds will need to support:
- Complex internal channels
- Transparent parts for lights
- Better shielding against electronic noise
Electronic Injection Molding is evolving fast to meet these needs. Likewise, Mold Makers are embracing new tech like:
- CNC machining for precision
- Laser engraving for ultra-fine textures
- Simulation software to perfect mold flow
Together, they are pushing audio design into a new era.
High-end audio is about more than sound. It’s about touch, style, and the emotional experience of quality. Electronic Injection Molding brings this to life—creating beautiful, durable, and functional housings for everything from home speakers to studio gear.
Behind every great molded part stands a talented Mold Maker, ensuring perfection down to the finest detail.
As demand grows for better design, tighter tolerances, and sustainable practices, both Electronic Injection Molding and Mold Maker expertise will remain essential to building the future of high-end audio equipment.