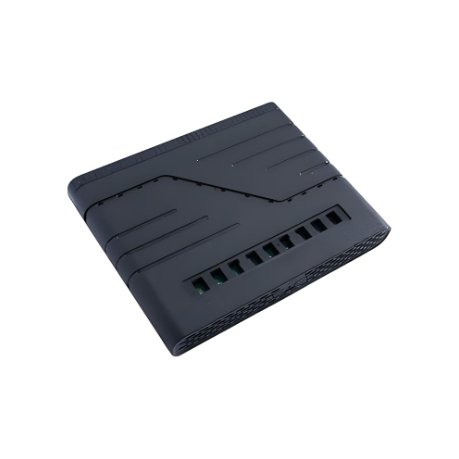
Plastic housings are everywhere. From electronics and home appliances to medical and industrial tools, they protect internal parts, enhance product appearance, and provide structural support. But how are these housings made quickly, accurately, and at a low cost?
The answer is Housing Injection Molding.
This process is the preferred method for producing high-quality plastic housings in large volumes. It offers unbeatable speed, precision, and flexibility. Behind this process stands the expertise of every skilled Mold Maker, who plays a vital role in delivering top-notch results.
In this article, we explain why so many industries choose Housing Injection Molding and how a good Mold Maker ensures success every time.
The Basics of Housing Injection Molding
Housing Injection Molding is a manufacturing process used to create complex plastic enclosures. It involves injecting molten plastic into a custom-made mold, then cooling it to form the desired shape.
Once cooled, the part is ejected and ready for use. This process can repeat thousands of times with consistent quality, making it perfect for mass production.
To succeed, every project needs a precise mold—designed, built, and maintained by a professional Mold Maker.
Why Use Housing Injection Molding?
Let’s explore the major reasons why manufacturers pick Housing Injection Molding over other methods.
1. Exceptional Precision
Plastic housings often need tight tolerances. Components must fit perfectly, whether it’s a phone casing or a control box. Housing Injection Molding delivers unmatched accuracy. A properly built mold can repeat dimensions down to fractions of a millimeter.
That level of precision depends heavily on a skilled Mold Maker, who creates molds that stay accurate over thousands of cycles.
2. High Efficiency and Speed
Once the mold is made, each cycle of Housing Injection Molding can take just 30 to 60 seconds. Thousands of housings can be produced daily, which keeps supply chains moving.
Other methods like 3D printing or CNC machining are slower and costlier for large volumes. That’s why many companies turn to Housing Injection Molding when speed matters.
3. Cost Savings in Mass Production
While the mold may cost more upfront, the per-part cost drops dramatically in mass production. This is especially true when working with an experienced Mold Maker who builds a long-lasting mold.
Compared to other production methods, Housing Injection Molding offers the best value over time.
4. Superior Strength and Durability
Plastic housings must protect. They endure drops, pressure, and harsh environments. Housing Injection Molding allows for strong materials like ABS, polycarbonate, and nylon—each selected to match the housing’s end-use.
A smart Mold Maker helps optimize wall thickness, ribbing, and structural support during mold design to boost strength without wasting material.
5. Complex Geometry and Fine Details
Housing Injection Molding supports intricate designs. From snap fits and ventilation slots to logos and curved edges, nearly anything can be molded into the housing.
This is only possible with a mold that has been carefully crafted. The Mold Maker ensures every detail appears clearly, from smooth surfaces to fine text.
6. Wide Range of Material Choices
Depending on the application, manufacturers can choose from many plastic types:
- ABS – strong, rigid, good surface finish
- Polycarbonate (PC) – clear, impact-resistant
- Nylon (PA) – tough, wear-resistant
- PP (Polypropylene) – flexible, chemical-resistant
- PC+ABS blend – combines strength and moldability
The Mold Maker can guide material selection by checking the shrink rate, temperature needs, and mold design requirements.
7. Custom Textures and Surface Finishes
Whether matte, glossy, or textured, Housing Injection Molding offers custom surface finishes. These finishes are built into the mold surface itself—no need for extra steps.
The finish quality depends directly on the mold surface. That’s why a highly skilled Mold Maker uses fine polishing, laser etching, or sandblasting techniques to deliver a perfect result.
Key Role of the Mold Maker
While the machine injects the plastic, it’s the Mold Maker who ensures success. The Mold Maker designs and builds the steel mold that shapes every part. Their job includes:
- Designing core/cavity layout
- Choosing the right steel for durability
- Creating vents, gates, and cooling lines
- Polishing and fitting the mold with precision
- Testing for flash, short shots, or warping
Without a good mold, there is no good part. That’s why working with a trusted Mold Maker is critical for every Housing Injection Molding project.
Design Freedom for Engineers
Housing Injection Molding gives product engineers more freedom. Need snap locks? Hidden screws? Rounded corners? Reinforced posts? It’s all possible.
The Mold Maker can turn these ideas into a tool that makes every detail right, every time.
Applications Across Industries
Because of its benefits, Housing Injection Molding is used in many fields:
- Electronics – phone cases, battery covers, remote controls
- Medical – device housings, handheld scanner cases
- Automotive – interior panels, switch housings
- Home Appliances – blender bodies, vacuum housings
- Industrial – control box enclosures, power tool shells
In all these cases, the molded housing protects internal parts while offering an attractive look and feel.
Environmental Advantages
Modern Housing Injection Molding also supports sustainability:
- Less waste due to precise material use
- Recyclable materials like PP or ABS
- Energy-efficient machines
- Reusable steel molds from trusted Mold Makers
This makes it a smarter and greener choice for companies concerned about their environmental footprint.
When it comes to plastic enclosures, Housing Injection Molding stands above the rest. It combines precision, speed, strength, and beauty into one efficient process. Whether you’re producing 10,000 phone cases or 1 million control boxes, this method offers unbeatable value.
But remember: everything depends on the mold. That’s why choosing an expert Mold Maker is just as important as choosing the right plastic. With their help, your product will look better, last longer, and get to market faster.
If you need to make quality plastic housings, Housing Injection Molding is the smart way to go—and a skilled Mold Maker is your best partner for success.