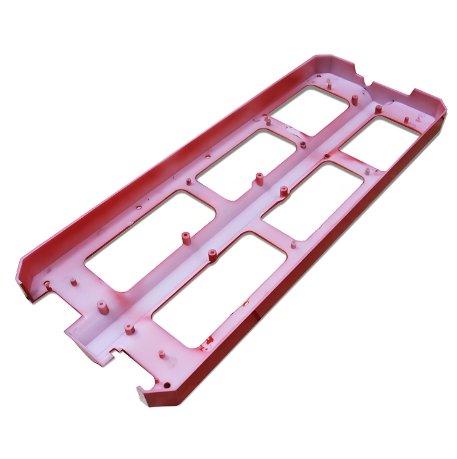
In today’s world, electronic products are used everywhere—from homes and hospitals to cars and outdoor equipment. Many of these products need protection from water, moisture, and dust. That’s where Waterproof Plastic Housings come in. These enclosures protect sensitive internal parts. One of the best ways to make them is through Housing Injection Molding. This process allows manufacturers to create tough, water-resistant housings that last a long time.
In this article, we will explore how Housing Injection Molding works for waterproof housings. We’ll also look at the role of the Mold Maker, materials used, design features, and key benefits. This guide will help you understand why plastic injection molding is a top choice for producing waterproof housings.
The Role of Housing Injection Molding
Housing Injection Molding is a method used to make strong and accurate plastic housings. In this process, melted plastic is injected into a metal mold. Once the plastic cools, it forms a solid part. This method is widely used to create waterproof housings because of its precision and repeatability.
Using Housing Injection Molding, manufacturers can control wall thickness, shape, and seal design. These features are important for creating a housing that keeps water out. Whether it’s for phones, medical tools, or outdoor cameras, Housing Injection Molding gives reliable results.
Importance of the Right Mold Maker
A skilled Mold Maker plays a huge role in the success of waterproof housings. They design and build the metal molds used in the injection process. The mold must be exact. If it’s off by even a little, the housing may not seal properly.
A professional Mold Maker understands the details of seal lines, venting, and pressure flow inside the mold. These skills are important when making waterproof products. A poor-quality mold can lead to leaks and product failure. That’s why working with an experienced Mold Maker is key to producing top-quality housings.
Materials for Waterproof Plastic Housings
The material used in Housing Injection Molding affects how well a product resists water. Not all plastics are the same. Some absorb water, while others repel it. Here are some materials commonly used:
- Polycarbonate (PC): Strong and transparent. Great for impact resistance and outdoor use.
- Acrylonitrile Butadiene Styrene (ABS): A popular choice for indoor housings. Offers strength and ease of molding.
- Polyamide (Nylon): Durable and resistant to chemicals, but can absorb water unless specially treated.
- Polypropylene (PP): Lightweight, water-resistant, and flexible.
- Thermoplastic Elastomers (TPE): Often used for gaskets or sealing rings to block water.
Your Mold Maker and material supplier can guide you in choosing the best material based on your waterproofing needs.
Design Features That Improve Waterproofing
When it comes to Housing Injection Molding, design matters a lot. You can’t just use any shape if you want your product to be waterproof. Special design features help keep water out:
- Built-in seals or gaskets: Soft plastic can be molded into the housing to seal it tightly.
- Snap fits or screws with O-rings: These provide strong closure between housing parts.
- Overmolding: This is when a second plastic layer is molded over the first to create waterproof seals.
- Lip and groove design: One part of the housing fits into the other, creating a tight seal.
A good Mold Maker knows how to design the mold to create these features. This saves time and avoids the need for extra parts.
Advantages of Injection Molding for Waterproof Housings
Using Housing Injection Molding offers several advantages for waterproof enclosures:
- High precision: Molds can be designed with great detail, making sure all seals fit perfectly.
- Repeatable quality: Once the mold is ready, each part comes out the same.
- Fast production: Multiple housings can be made in a short time.
- Cost-effective in large runs: Though mold creation can be expensive, the per-part cost drops for high-volume production.
- Custom solutions: A skilled Mold Maker can help you build custom waterproof housings that meet your exact needs.
These benefits make Housing Injection Molding ideal for industries like automotive, medical, telecom, and consumer electronics.
Common Applications
Waterproof plastic housings are used in many industries. Some common examples include:
- Outdoor security cameras
- Smartphones and tablets
- Wearable fitness devices
- Medical monitors and sensors
- GPS systems for vehicles
- Underwater equipment
- Smart home devices
All these products must be protected from water, and Housing Injection Molding provides a trusted method to make it happen.
Testing Waterproof Housings
After molding, housings must be tested to ensure they meet waterproofing standards. Common tests include:
- IP rating tests: Products are tested for dust and water resistance.
- Pressure tests: Check how much pressure the housing can handle without leaking.
- Submersion tests: Products are placed in water for a set time to check for leaks.
If the housing passes these tests, it proves the Mold Maker and the molding process did their job well.
Tips for Choosing the Right Mold Maker
Choosing the right Mold Maker is one of the most important steps. Here’s what to look for:
- Experience with waterproof parts
- CAD design and simulation tools
- Quality control processes
- Fast response time
- Prototyping and testing support
A professional Mold Maker not only builds the mold but also helps with design improvements. They make sure the housing will work before mass production starts.
Housing Injection Molding is a top choice for making waterproof plastic housings. From material selection to mold design and part testing, every step matters. A skilled Mold Maker ensures the mold is accurate and strong. They help build housings that can stand up to water, dust, and everyday wear.
Whether you’re making a medical sensor, a smart speaker, or an outdoor camera, Housing Injection Molding gives you the strength and precision needed for waterproof performance. With the right team and tools, your product will be ready for anything.