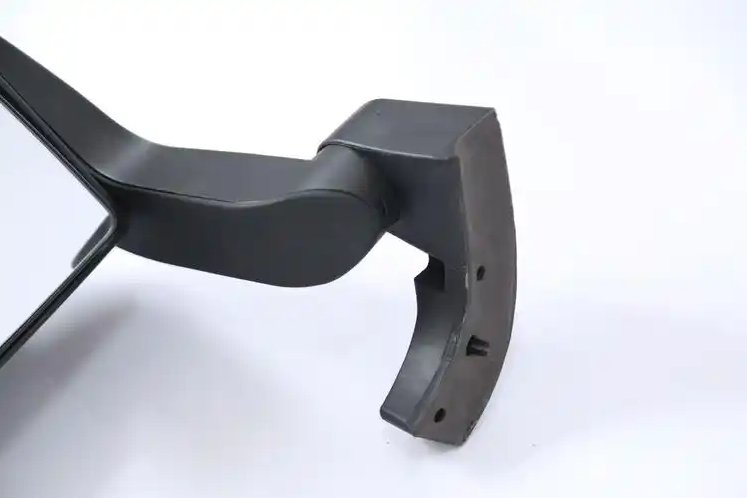
In industries where durability is critical, plastic housings must withstand force, impact, vibration, and environmental stress. This is especially true in automotive, industrial, and outdoor electronics. These housings can’t afford to crack, deform, or fail. To meet these demands, many manufacturers rely on Housing Injection Molding. This process produces tough, long-lasting enclosures designed to perform under pressure.
A key factor in the success of these parts lies in the work of the Mold Maker. Without a precisely built mold, even the strongest materials can’t reach their full potential. In this article, we’ll explore how Housing Injection Molding supports high-strength applications, why mold design is critical, and which materials and features work best.
What Is Housing Injection Molding?
Housing Injection Molding is a process where melted plastic is injected into a metal mold at high pressure. Once cooled, the plastic solidifies into the desired shape. This technique is ideal for creating plastic enclosures, especially where consistency and strength matter most.
The advantage of Housing Injection Molding lies in its precision. It allows for accurate wall thickness, support ribs, screw bosses, and snap fits—all of which improve strength and reliability. For high-strength uses, it ensures tight tolerances and repeatable results, even in large production runs.
Why a Skilled Mold Maker Matters
A reliable Mold Maker is essential in the production of strong housings. The mold is the foundation of the entire process. A poorly made mold results in weak spots, poor material flow, or even part failure. This can lead to expensive rework or delays.
A qualified Mold Maker understands how to build a durable, high-precision mold that supports complex housing shapes and thick-walled areas. They ensure balanced filling, proper venting, and strong shut-offs. This prevents internal stress and ensures a longer mold life. Choosing an experienced Mold Maker also means faster development and fewer problems in production.
Applications that Need High-Strength Housings
Many industries rely on Housing Injection Molding to produce strong plastic enclosures. Some common examples include:
- Automotive electronics: Control modules, sensor housings, fuse boxes
- Power tools: Battery housings, motor covers, gear enclosures
- Telecommunication: Signal units and rugged modems for outdoor use
- Industrial control systems: PLC housings, remote terminals, safety enclosures
- Medical equipment: Diagnostic tools and hospital-use monitors
In each case, the housing must resist impact, heat, and sometimes chemicals. With help from a skilled Mold Maker, these challenges can be overcome.
Key Design Features for Strength
Design plays a major role in how durable a plastic housing will be. Housing Injection Molding allows for a wide range of design options. Here are some features that add to part strength:
- Wall thickness control: Thicker walls can handle more impact, but must be even to avoid warping.
- Ribs and gussets: These support the walls without increasing material use.
- Bosses and inserts: Add screw or mounting points with extra support.
- Overmolding: Adds a second material for shock resistance or sealing.
- Textured surfaces: Help reduce wear and improve grip.
All of these must be carefully considered during mold design. The Mold Maker must understand the part’s environment and design the mold to deliver strong features that don’t compromise appearance or function.
Best Materials for High-Strength Housings
The choice of plastic resin has a big impact on performance. Not all plastics are equally strong. For Housing Injection Molding, some materials are better suited for strength and durability:
- Polycarbonate (PC): Known for impact resistance and high clarity. Used in outdoor or high-heat settings.
- ABS (Acrylonitrile Butadiene Styrene): Tough, good surface finish, and easy to mold.
- Glass-Filled Nylon: Very strong and heat resistant. Ideal for automotive and industrial use.
- PBT (Polybutylene Terephthalate): Good electrical properties and chemical resistance.
- Polypropylene (PP): Flexible and fatigue-resistant, often used in moving parts.
The Mold Maker must also consider how the material flows inside the mold. Some resins flow better than others. Strong materials like glass-filled plastics need higher pressure and careful temperature control.
How the Injection Process Supports Strength
The Housing Injection Molding process itself adds to part strength. Unlike 3D printing or thermoforming, injection molding applies high pressure, which helps pack the material tightly. This reduces voids, sink marks, and weak spots.
Cooling is also important. Uneven cooling can lead to stress or warping. A skilled Mold Maker uses proper cooling channel design to ensure the part cools evenly. The result is a solid, high-quality housing that meets demanding standards.
Quality Control and Testing
For high-strength housings, quality control is critical. Manufacturers often run tests to verify performance, including:
- Drop tests: To check how the housing holds up when dropped from different heights.
- Thermal cycling: To simulate changing temperatures over time.
- UV resistance: For outdoor enclosures that face sunlight.
- Chemical exposure: To test resistance to oils, fuels, or cleaning agents.
- Tensile and impact tests: To measure force resistance.
All these steps help confirm that the Housing Injection Molding process and the mold created by the Mold Maker deliver parts that meet real-world needs.
Benefits of Housing Injection Molding for Strength
There are many reasons manufacturers choose this method for strong housings:
- Durability: With the right materials and mold design, parts last longer.
- Repeatability: Every part is nearly identical.
- Scalability: Ideal for both small batches and mass production.
- Cost-effective: While mold creation is an upfront investment, part costs are low.
- Customization: Easily add logos, holes, mounting points, or texture.
The collaboration between a skilled Mold Maker and a product designer makes all this possible.
Choosing the Right Mold Maker for the Job
Don’t overlook this step. The Mold Maker you choose can make or break your project. Look for someone who:
- Has experience with strong or thick-walled housings
- Understands material properties and flow behavior
- Uses advanced tools like CAD, CAM, and simulation
- Offers prototype testing and support
- Maintains quality standards throughout the project
Your Mold Maker isn’t just a supplier. They’re a partner in developing a reliable, high-performance plastic housing.
Housing Injection Molding is a trusted method for producing strong, durable plastic housings for demanding applications. With precise molds, strong materials, and thoughtful design, manufacturers can produce parts that handle extreme use and harsh environments.
A reliable Mold Maker brings the skills, tools, and experience needed to ensure the mold delivers strength and quality from the first part to the last. Together, this powerful combination creates high-strength housings that protect valuable equipment and ensure long product life.