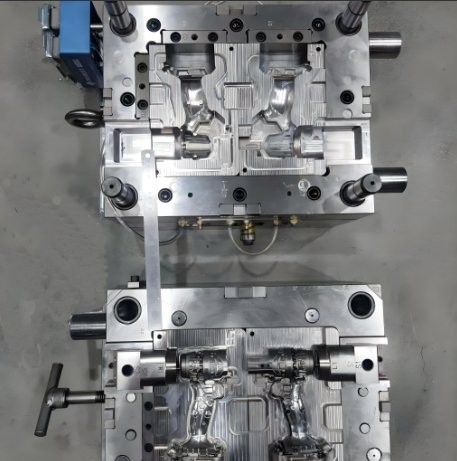
Plastic housings are everywhere—from home electronics to medical tools and industrial controllers. These parts must be strong, accurate, and visually clean. One method stands out for making such housings: housing Injection Molding. This technique offers speed, consistency, and cost savings, especially when done by a skilled Mold Maker.
If your product needs a high-quality plastic shell, finding the right Mold Maker is key. This article will explain how the injection mold maker works behind the scenes, how housing Injection Molding helps manufacturers, and why the right tooling partner makes all the difference.
What is Housing Injection Molding?
Housing Injection Molding is a plastic manufacturing process. Melted plastic is injected into a steel mold under high pressure. Once cooled, it forms a rigid part, often used as a casing or shell for an electronic or mechanical device.
These plastic housings protect sensitive components inside. They also give products a finished look. Typical uses include:
- Smart home devices
- Tablets, controllers, and remotes
- Lighting enclosures
- Car interior panels
- Power tools and battery packs
The result is a clean, durable plastic part that meets design and function needs. But to get this right, you need the experience of a top-tier Mold Maker.
The Mold Maker’s Role in the Process
A Mold Maker is the expert who designs and builds the steel tool (mold) used in the injection molding machine. This tool shapes the molten plastic into your final housing part.
The work of the Mold Maker includes:
- CAD design and simulation
- Mold base selection and sizing
- Machining the cavity and core
- Inserting cooling lines and ejector systems
- Testing mold performance
Everything starts with your 3D design. The Mold Maker reviews it and makes improvements to reduce cost and increase manufacturability. Next comes the creation of the mold tool. Precision is essential—any small error affects all future parts.
A great Mold Maker delivers a mold that lasts through thousands of cycles. It runs smoothly with little downtime. This reliability is the heart of quality housing Injection Molding.
Why Use Injection Molding for Housings?
There are many ways to make plastic parts, but few match the benefits of housing Injection Molding. Here’s why it’s ideal for plastic housings:
1. Strong and Clean Parts
Injection-molded housings are tough and often have detailed surfaces. Texture, logo, and clip features can all be molded in one shot.
2. Fast Cycle Times
Each molding cycle takes only seconds. This means high volumes in short time frames.
3. Low Per-Part Cost
Once the mold is built, each housing costs very little to make.
4. Material Versatility
Many plastics work well for housings, including ABS, polycarbonate, polypropylene, and nylon.
5. High Repeatability
The same part can be made again and again with exact size and quality.
How a Mold Maker Cuts Costs
Though the mold itself can be expensive, a skilled Mold Maker helps reduce the total project cost by optimizing the mold design. Here’s how:
1. Choosing the Right Steel
Tool steel like P20 is good for medium runs. H13 or S136 suits high volumes. A smart steel choice saves cost without sacrificing life.
2. Designing Efficient Cooling
Faster cooling means shorter cycles. That saves money in every production run.
3. Adding Ejector Features
Good ejection avoids part damage. A well-planned mold cuts scrap rates.
4. Using Standard Mold Bases
A Mold Maker can reduce cost by using standard-size bases with custom inserts.
5. Fewer Revisions
Good planning up front avoids costly changes later. A professional Mold Maker delivers right the first time.
These decisions can reduce cycle time by 20%, mold build time by 30%, and total project cost by 15%.
Mold Design for Plastic Housings
Designing molds for housings involves unique challenges. A great Mold Maker considers:
- Wall thickness: Uniform walls help flow and cooling
- Draft angles: These make parts easier to eject
- Screw bosses: Needed for assembly with PCBs or covers
- Snap fits: For tool-free assembly
- Cooling layout: Ensures parts don’t warp
In housing Injection Molding, looks matter too. Surface textures, paintability, or transparent areas must all be planned in the tool. A poor mold design affects part quality, waste, and user satisfaction.
Housings for Specific Applications
Plastic housings are used in nearly every industry. With housing Injection Molding, the same mold can serve many purposes.
1. Consumer Electronics
Smartphones, remotes, and routers all use tight-tolerance housings.
2. Medical Devices
Diagnostics and handheld tools need biocompatible housings made in clean-room conditions.
3. Automotive
Interior panels, lighting covers, and sensor boxes are often molded.
4. Home Appliances
From coffee makers to blenders, plastic housings give shape and safety.
A reliable Mold Maker ensures that each of these applications meets both technical and aesthetic requirements.
Working with a Mold Maker: The Process
Here’s a typical project workflow when you need plastic housings:
- Submit 3D Design
You provide the part file and specifications. - DFM Review by Mold Maker
The Mold Maker checks draft angles, parting lines, and gating. - Mold Quotation
You receive a quote for mold cost, part price, and timelines. - Tooling and Machining
The mold is made using CNC, EDM, and other precision tools. - T1 Sampling
First molded samples are produced and inspected. - Mold Refinement
Minor corrections may be done to ensure accuracy. - Production Run
Once approved, full-scale housing Injection Molding begins. - Packaging and Delivery
Finished housings are packed and shipped on schedule.
This full-cycle support ensures you’re never left guessing.
Why Choose a Chinese Mold Maker?
Many companies today trust Mold Makers from China for housing Injection Molding projects. Here’s why:
- Lower tool cost with high quality
- Fast turnaround times
- Full in-house service, from mold making to molding
- Export experience with global companies
- Skilled engineers with decades of expertise
Chinese Mold Makers often combine speed, affordability, and precision. With careful vetting, you can find partners who deliver world-class results.
Final Thoughts
If you need plastic housings that are strong, clean, and affordable, housing Injection Molding is the best method. And behind every perfect molded housing is a professional Mold Maker.
Their role is not just technical. They make your ideas real. They help cut costs, speed production, and improve quality. Choosing the right Mold Maker means fewer delays, better results, and a product you can be proud of.
So whether you’re designing a smart home sensor, a battery cover, or a handheld device case—don’t just look for a molding company. Look for a partner. One who knows what makes a great mold and how to turn it into great parts.
When you team up with a skilled Mold Maker, your housing Injection Molding project becomes faster, smoother, and more successful.