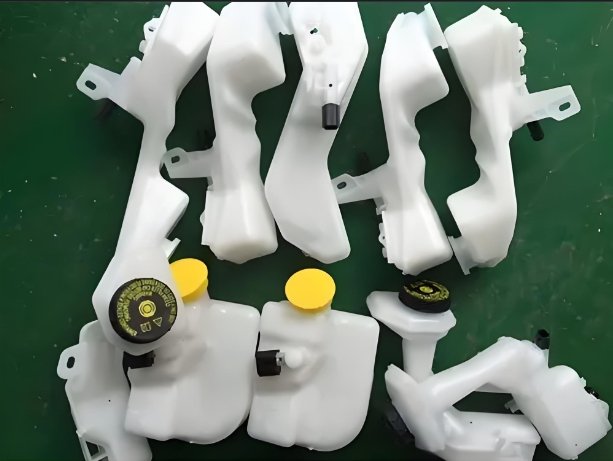
Plastic housings are essential in many products. From electronics and medical devices to home appliances and automotive parts, these housings protect inner components while giving products their final shape and look. Behind every plastic housing is a well-designed and precisely built injection mold. That’s where housing Injection Molding and a skilled Mold Maker come in.
At the core of successful housing Injection Molding lies excellent mold design and manufacturing. Without a good mold, the plastic part will fail—whether due to warping, poor fit, short shots, or inconsistent dimensions. This article explains how plastic housing molds are designed and built, and how a professional Mold Maker ensures every housing meets the highest standards.
What Is Housing Injection Molding?
Housing Injection Molding is the process of forming plastic enclosures by injecting molten plastic into a custom-built mold. These housings must be strong, dimensionally accurate, and often cosmetically appealing. This makes the mold quality crucial.
Plastic housings are used in:
- Remote controls
- Medical monitors
- Control panels
- Power tool cases
- Router shells
- Car sensor boxes
Each housing must protect internal parts and align perfectly with screws, snaps, or connectors. The better the mold, the better the finished part.
The Importance of Mold Design
Designing a mold for housing Injection Molding is a detailed process. A small mistake can lead to large production losses. The Mold Maker must consider many technical details:
1. Parting Line Position
This line is where the mold splits. A poor parting line may cause flash or visual issues.
2. Ejector Pin Layout
Ejector pins push the part out after molding. Their placement must avoid marks in key areas.
3. Cooling Channel Design
Proper cooling reduces cycle time and prevents warping.
4. Gate Type and Position
Gates are the entry point for molten plastic. Improper gates can leave visible marks or cause uneven filling.
5. Draft Angles
Slight angles make it easier to remove the part from the mold. No draft? The part may stick or be damaged.
An experienced Mold Maker handles all these challenges during mold design. The goal is to create a robust tool that produces accurate housings for years to come.
Software and Tools Used in Mold Design
Today’s Mold Makers use advanced software to improve design speed and accuracy. Some popular tools include:
- CAD Software: Used to build 3D mold models.
- CAE Simulation: Moldflow or similar tools check filling, cooling, and warping.
- CAM Programming: Creates toolpaths for CNC machines to cut steel blocks into mold parts.
Simulation tools are especially helpful in housing Injection Molding, where warpage or flow marks can ruin cosmetic parts. The software helps predict problems before steel is cut.
Materials Used for Plastic Housing Molds
A professional Mold Maker selects steel carefully based on part volume, material, and surface needs.
- P20 Steel: Good for medium runs. Easy to machine and polish.
- H13 Steel: Better for high-heat plastics or long production cycles.
- S136 Stainless Steel: Ideal for clear parts or medical-grade housings.
Choosing the right steel extends mold life and reduces maintenance. The Mold Maker also treats the steel to improve hardness, using processes like nitriding or heat treatment.
Manufacturing the Mold
Once design is done, the Mold Maker begins the build. This includes:
1. CNC Machining
Used to shape the cavity and core blocks to match the 3D model.
2. EDM (Electric Discharge Machining)
Great for deep, sharp features or complex textures.
3. Polishing and Texture
Done by hand or machine, depending on the housing’s cosmetic needs.
4. Assembly
All parts—base, slides, lifters, ejectors, cooling lines—are fitted together.
The build takes weeks of careful work. A good Mold Maker checks all parts and tests movement before sampling.
Mold Testing and Validation
Before production begins, the Mold Maker runs trial shots. This stage is called T1 or T0 sampling. The goals are:
- Confirm part dimensions
- Check surface finish
- Inspect for short shots, warping, sink marks
- Adjust gate size or cooling if needed
If problems appear, the Mold Maker fine-tunes the tool. This might involve adjusting steel, vents, or cooling lines. Once approved, the mold is ready for full housing Injection Molding.
Benefits of a High-Quality Mold
Investing in a well-made mold brings big returns:
1. Stable Mass Production
Parts come out the same every time, even after thousands of shots.
2. Faster Cycle Time
Good cooling and ejection reduce downtime.
3. Lower Scrap Rate
Precision molding means fewer rejected parts.
4. Cleaner Finish
No extra sanding or trimming needed for cosmetic housings.
A professional Mold Maker understands the long-term impact of mold quality. Cutting corners only leads to waste later.
Plastic Materials for Housing Injection Molding
Different housing uses require different plastics. Common choices include:
- ABS: Tough and good-looking, used in electronics.
- PC (Polycarbonate): Strong and clear, used in medical or lighting housings.
- PA (Nylon): Wear-resistant, used in tools or automotive.
- PP (Polypropylene): Lightweight and chemical-resistant.
The Mold Maker accounts for plastic shrinkage during design. They also help you choose a resin that matches your housing’s function and appearance.
Common Applications of Housing Injection Molding
Plastic housings are used in nearly every field:
1. Consumer Electronics
Tablet covers, remote cases, routers, and gaming controllers.
2. Medical Equipment
Device panels, handheld tools, pump housings.
3. Automotive Interiors
Sensor boxes, dashboard elements, and control knobs.
4. Industrial Controls
PLC covers, motor control panels, and switch housings.
A well-built mold serves each of these applications with precision and speed.
Why Choose a Chinese Mold Maker?
China leads the world in housing Injection Molding thanks to:
- Cost-effective tooling
- Skilled workforce
- Advanced machines and software
- Fast turnaround
- Full-service factories
Working with a reliable Mold Maker in China can cut lead times and save up to 40% on tooling costs—without sacrificing quality.
Housing Injection Molding plays a vital role in today’s plastic product design. To get strong, beautiful, and cost-effective housings, you need a well-designed and well-built mold.
The Mold Maker makes that happen. From choosing the right steel to final polishing, they focus on details that lead to success. A poor mold brings delays and defects. A great mold brings efficiency, accuracy, and satisfaction.
When your product needs a plastic enclosure, don’t gamble on mold quality. Partner with a skilled Mold Maker who understands the full process of housing Injection Molding. Your product’s look, function, and future all depend on that first tool.