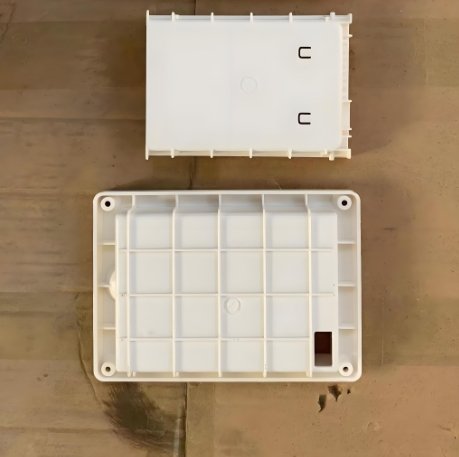
In the realm of plastic manufacturing, housing Injection Molding stands out as a pivotal process, especially when it comes to producing durable and precise plastic enclosures. Central to this process is the expertise of a seasoned Mold Maker, whose role is crucial in designing molds that meet exacting standards. This article delves into the intricacies of housing mold design, highlighting the importance of each design element and the value a proficient Mold Maker brings to the table.
Understanding Housing Injection Molding
Housing Injection Molding involves injecting molten plastic into a meticulously crafted mold to produce plastic housings used in various applications, from electronics to automotive components. The process demands precision, as the final product must meet specific dimensional and structural requirements. A well-designed mold ensures consistency, reduces defects, and enhances production efficiency.
The Role of the Mold Maker
A Mold Maker is not just a technician but an artisan who combines engineering knowledge with hands-on skills. Their responsibilities include:
- Designing the Mold: Using CAD software to create detailed mold designs that account for part geometry, material flow, and cooling requirements.
- Selecting Materials: Choosing appropriate materials for the mold based on the type of plastic used and the expected production volume.
- Machining and Assembly: Utilizing CNC machines and other tools to fabricate mold components, followed by precise assembly to ensure optimal performance.
- Testing and Validation: Conducting trial runs to identify and rectify any issues before full-scale production.
The Mold Maker’s expertise directly influences the quality and longevity of the mold, impacting the overall success of the housing Injection Molding process.
Key Design Considerations in Housing Molds
Designing a mold for plastic housings requires meticulous attention to several factors:
1. Part Geometry and Complexity
Complex geometries, such as undercuts or intricate internal features, necessitate advanced mold components like slides or lifters. The Mold Maker must anticipate these challenges and incorporate solutions into the design.
2. Material Flow and Cooling
Ensuring uniform material flow prevents defects like warping or sink marks. Strategically placed cooling channels aid in rapid and even cooling, enhancing cycle times and part quality.
3. Draft Angles and Ejection
Incorporating appropriate draft angles facilitates easy part ejection, reducing wear on the mold and minimizing the risk of part damage.
4. Surface Finish and Texture
The mold’s surface finish directly affects the appearance of the final product. Polishing or texturing the mold surfaces can achieve the desired aesthetic and functional properties.
Material Selection for Molds
Choosing the right material for the mold is vital:
- P20 Steel: Commonly used for moderate production volumes due to its machinability and durability.Formlabs
- H13 Steel: Suitable for high-volume production, offering excellent hardness and resistance to thermal fatigue.Formlabs+1Formlabs+1
- S136 Stainless Steel: Ideal for molds requiring high corrosion resistance and a superior surface finish.
The Mold Maker evaluates factors like production volume, plastic material, and desired surface finish to select the most appropriate mold material.
Innovations in Mold Design
Advancements in technology have introduced new tools and methods to enhance mold design:
- Simulation Software: Programs like Moldflow allow Mold Makers to simulate material flow, cooling, and warpage, enabling optimization before physical mold creation.
- 3D Printing: Rapid prototyping using 3D printing helps in evaluating design concepts and making quick adjustments, saving time and resources.
- Hot Runner Systems: These systems maintain the plastic in a molten state within the mold, reducing waste and improving cycle times.
Quality Assurance and Testing
Before commencing full-scale production, rigorous testing ensures the mold’s performance:
- Trial Runs: Initial production runs help identify potential issues, allowing for adjustments in the mold design or process parameters.
- Dimensional Analysis: Measuring the produced parts against specifications ensures accuracy and consistency.
- Durability Testing: Assessing the mold’s ability to withstand repeated cycles without degradation ensures long-term reliability.
The success of housing Injection Molding hinges on the precision and expertise embedded in the mold design. A proficient Mold Maker plays an indispensable role, ensuring that every aspect of the mold contributes to producing high-quality, consistent, and durable plastic housings. By understanding the complexities involved and leveraging modern technologies, manufacturers can achieve efficiency and excellence in their molding processes.