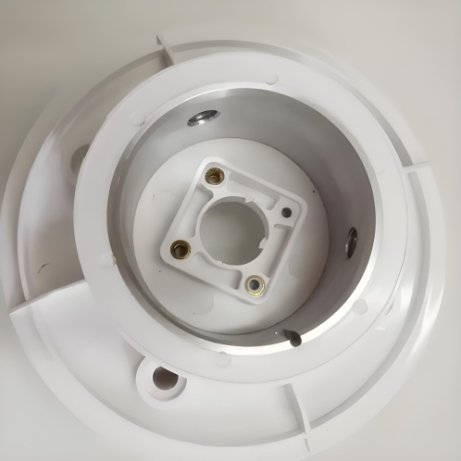
Housing injection molding plays a critical role in modern product development. From electronic device shells to protective casings, plastic housings are everywhere. However, cost remains a major concern, especially when developing a new product or scaling production.
This article explains how to reduce costs in your housing injection molding project without compromising quality. Whether you’re launching a startup product or working on a high-volume commercial item, these tips—straight from experienced mold makers—will help you save money.
Understanding the Cost Structure
Before you can lower costs, you must understand where the money goes in a housing injection molding project. Typically, you’re dealing with two major costs:
- Mold Tooling Cost – the price to design and fabricate the injection mold.
- Part Production Cost – the cost per unit once the mold is complete.
Each section involves different strategies. A good mold maker will work with you on both fronts, ensuring your project stays within budget.
Tip 1: Design for Manufacturability (DFM)
The biggest cost savings often begin at the design stage. When your part is easy to mold, production becomes faster and cheaper. That’s why mold makers use DFM practices.
Key DFM Tips:
- Maintain uniform wall thickness to avoid warping or sink marks.
- Add draft angles to all vertical surfaces for easy ejection.
- Avoid deep undercuts unless necessary. These add complexity to the mold.
- Use radii instead of sharp corners to extend mold life and improve plastic flow.
A seasoned mold maker can review your CAD model and suggest changes that maintain functionality while reducing tooling and cycle time costs.
Tip 2: Choose the Right Material
Plastic material selection can greatly affect your bottom line. While some housings require high-end materials like polycarbonate or flame-retardant ABS, others can use more affordable resins.
Suggestions:
- Use standard grades unless specialty properties are required.
- Ask your mold maker to recommend locally sourced resins to cut logistics costs.
- Consider recycled material if surface finish and strength aren’t critical.
Material costs make up a large portion of the per-unit cost in housing injection molding, so a small change here can bring big savings.
Tip 3: Select the Right Mold Type
Not every project needs a steel mold that lasts a million cycles. If you’re only making a few thousand parts, you can reduce tooling costs by choosing a mold that matches your production goals.
Mold Options:
- Prototype molds: Made from aluminum or soft steel, great for small runs.
- Bridge molds: Lower-cost steel molds for medium volumes.
- Production molds: Hardened steel, more expensive, but ideal for high volumes.
Talk to your mold maker about how many shots you need and match the mold type accordingly. This prevents over-investing in tooling that you won’t fully use.
Tip 4: Simplify the Mold Design
Every slider, lifter, and insert adds cost to your mold. While some features are necessary, others can be redesigned or removed.
Simplification Strategies:
- Redesign parts to remove undercuts.
- Consolidate multiple parts into a single molded piece.
- Eliminate non-functional design features that make the mold more complex.
Experienced mold makers know how to simplify a mold while preserving part performance. Early involvement helps avoid expensive rework later.
Tip 5: Use Multi-Cavity Molds for High Volume
If you’re planning to produce high quantities of plastic housings, using a multi-cavity mold is a smart way to reduce unit cost. This means you produce several parts per cycle instead of just one.
While the initial tooling cost increases, the cost per part drops significantly. Your mold maker can calculate the payback period and show how fast you’ll recover the investment.
Tip 6: Increase Order Volume
Production costs decrease as volume increases. Why? Because fixed costs like setup and machine time get spread across more units.
If you can store extra parts or plan future use, increasing your order size helps reduce per-part pricing. Ask your mold maker if bulk pricing is available and how it affects lead time.
Tip 7: Optimize Cycle Time
Cycle time refers to how long it takes to produce one shot of molded parts. Faster cycles equal lower labor and machine costs. Your mold maker can optimize the mold with:
- Efficient cooling channels
- High-speed injection setups
- Quick ejection mechanisms
Even shaving a few seconds off each cycle can add up to big savings over thousands of units.
Tip 8: Minimize Secondary Processes
Each post-molding step adds cost—whether it’s trimming, painting, ultrasonic welding, or labeling. By designing a self-finished part or integrating logos/text into the mold, you can eliminate many of these processes.
Ask your mold maker to include features like:
- Molded-in clips instead of separate fasteners
- Engraved logos instead of printed ones
- Built-in alignment features to simplify assembly
These simple decisions reduce production time and lower your overall budget.
Tip 9: Work with a Local or Regional Mold Maker
Shipping molds and materials internationally can increase both cost and risk. Depending on your location, a local mold maker may offer:
- Lower shipping fees
- Easier communication and faster updates
- Reduced customs and tax headaches
If offshore manufacturing is your plan, look for a mold maker in a country known for cost-effective but high-quality tooling—like China, Vietnam, or India.
Tip 10: Get Multiple Quotes but Compare Smartly
Always get 2–3 quotes, but make sure you’re comparing apples to apples. Look for differences in:
- Mold material (P20, H13, S136, etc.)
- Number of cavities
- DFM suggestions included or not
- Mold warranty or maintenance terms
- Shipping and logistics
A low quote may cut corners or lack services included by a premium mold maker. Look beyond price to ensure you receive a mold that performs long-term.
Conclusion
Cutting costs in housing injection molding doesn’t mean cutting corners. By working with an experienced mold maker, you can optimize every stage—from design to delivery. Focus on:
- Smart part design
- Suitable materials
- Efficient tooling choices
- Bulk production strategies
Every dollar saved during the mold project adds up, especially over time and volume. If you’re not sure where to start, ask your mold maker for a design review focused on cost reduction. They’ll be glad to help you make smart decisions.
A successful housing injection molding project balances quality, speed, and price. With the right mindset and the right mold maker, you can achieve all three.