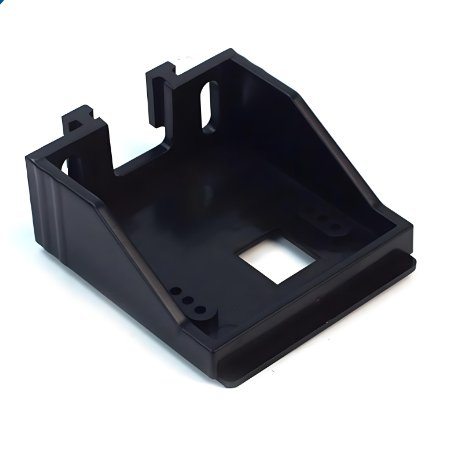
In today’s manufacturing world, housing injection molding is a key process for producing strong, lightweight, and precise plastic enclosures. Whether you’re creating cases for electronics, tools, or consumer products, having the right mold maker is crucial. Your success depends not just on the mold itself, but on how well you and your mold maker work together throughout the project.
This guide will walk you through everything you need to know about working with a mold maker on a housing injection molding project—from concept to completion.
Why the Right Mold Maker Matters
Choosing the right mold maker is like choosing a business partner. A skilled mold maker brings more than just tools. They bring years of experience in material selection, mold design, and manufacturing efficiency. For housing injection molding, where appearance, strength, and accuracy are critical, expertise matters.
A reliable mold maker can help you:
- Reduce product defects
- Speed up production
- Cut long-term costs
- Improve overall quality
Working with a less experienced or low-cost mold maker may lead to delays, rework, or even total mold failure.
Step 1: Share a Clear Project Scope
Start by giving your mold maker complete and clear project details. Include the following:
- 3D CAD files of the housing design
- Product usage and expected environment
- Target volume (low or high production)
- Material requirements
- Surface finish or color preferences
- Budget and lead time goals
The more information your mold maker has upfront, the better they can serve your housing injection molding needs. This saves time and avoids confusion later.
Step 2: Review and Improve the Design Together
Many mold makers offer Design for Manufacturability (DFM) services. This is when they analyze your part design to ensure it can be molded efficiently and with high quality.
During this stage, your mold maker may suggest changes like:
- Adding draft angles for easier part ejection
- Modifying wall thickness to avoid warping
- Removing undercuts to simplify tooling
- Adding ribs or gussets for structural support
These design changes help reduce cost, increase mold life, and ensure smoother housing injection molding.
Step 3: Select the Right Materials
Material selection is one of the most important choices in housing injection molding. It affects durability, appearance, and moldability.
Work with your mold maker to choose the right resin for your needs:
- ABS or PC for high-impact strength
- PP or PE for chemical resistance
- Nylon for wear resistance
- Flame-retardant grades for electronic housings
The mold maker can also help you balance material cost with performance, especially if you’re trying to meet a tight budget.
Step 4: Choose the Best Mold Type for Your Project
Mold types vary based on project needs. Your mold maker will help select the right one.
- Prototype molds: For low volumes and design testing. Made from aluminum.
- Steel molds: For medium to high volume production. More durable and precise.
- Multi-cavity molds: For high-volume production to reduce per-part cost.
- Family molds: For molding different parts in one cycle, often used in housings with multiple components.
The right choice depends on your goals, part complexity, and timeline. A trustworthy mold maker will guide you through the pros and cons.
Step 5: Monitor the Mold Build Process
Once the mold design is finalized, the mold maker begins machining and assembly. This usually takes 3–8 weeks depending on complexity.
Good mold makers will send regular updates, photos, and videos during the build. If you’re working with a mold maker overseas, ask for detailed timelines and clear communication milestones.
You should also receive mold trials (T0, T1, etc.) to check the quality of the first molded parts. This is a critical moment in the housing injection molding process. Make sure to inspect:
- Dimensions and tolerances
- Fit and assembly
- Surface finish
- Material performance
Any changes should be discussed and approved before finalizing the mold.
Step 6: Plan for Mass Production
After mold approval, the mold maker prepares for production. This is when housing injection molding shifts from development to output.
During this phase:
- Confirm resin availability
- Approve packing and shipping methods
- Set up quality checks for each batch
- Discuss ongoing maintenance of the mold
A good mold maker ensures consistent production and supports you even after delivery.
Step 7: Understand Maintenance and Mold Life
Molds require care. Your mold maker should give you a clear maintenance plan and mold life estimate.
For example:
- A P20 steel mold may last 100,000 to 500,000 cycles
- A hardened steel mold (H13, S136) can last 1 million+ cycles
Ask about:
- Cleaning frequency
- Mold storage conditions
- Wear part replacement (springs, ejector pins)
- Warranty terms
This ensures your housing injection molding project stays reliable long-term.
Tips for a Smooth Relationship
- Communicate often: Don’t disappear between stages. Stay involved.
- Be open to suggestions: A seasoned mold maker has seen many designs. Take their advice seriously.
- Set realistic timelines: Rushing the process can lead to errors.
- Get everything in writing: Scope, changes, prices, and timelines should be clearly documented.
When trust and transparency are present, the housing injection molding project runs much smoother.
Choosing the Right Mold Maker
Not all mold makers are the same. Here’s what to look for:
- Experience with housing injection molding
- Strong portfolio and customer reviews
- In-house tooling capabilities
- Clear pricing structure
- Willingness to support design and production
Sometimes, a slightly higher initial price from a qualified mold maker results in lower long-term costs and better quality.
Final Thoughts
Working with a mold maker for your housing injection molding project is a journey. It’s not just about making a mold—it’s about building a working relationship that ensures long-term success.
From material selection and mold building to final production, every decision counts. A good mold maker brings technical skill, practical knowledge, and real commitment to your product’s success.
If you’re planning a plastic housing project, start early, communicate clearly, and choose your mold maker wisely. With the right team, you’ll get strong, precise, and affordable plastic housings—ready to meet market demand.