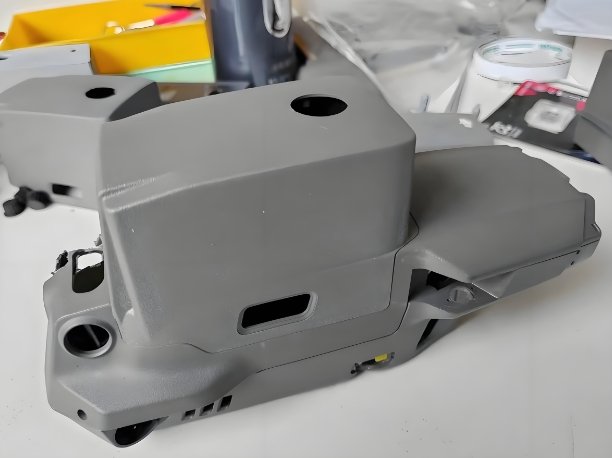
Digital twin technology is changing how we build things. For plastic product manufacturing, it’s a big step forward. In housing injection molding, digital twins are now helping companies save time, reduce errors, and make better plastic housings. This technology allows a mold maker to simulate, test, and improve mold designs before they are even built.
In this article, we’ll explore what digital twin technology is, how it works, and why it’s so useful in housing injection molding. We’ll also look at how a smart mold maker can use this tool to boost quality and performance in real-world mold projects.
What Is Digital Twin Technology?
A digital twin is a virtual copy of a real object. In housing injection molding, it’s a digital model of the mold, the molded part, and sometimes the whole injection system. This model is connected to real-world data and can be updated in real time.
For example, a mold maker can build a digital twin of a mold for a plastic device housing. Before cutting any steel, they test the mold virtually. They simulate the plastic flow, heat transfer, shrinkage, and part ejection. They can even simulate the machine that will run the mold. This helps catch problems early.
Why Digital Twins Matter in Housing Injection Molding
Plastic housings are used in many industries—electronics, medical, automotive, and home appliances. These housings must look good and fit perfectly. Small mistakes in the mold can lead to big problems, like warping, short shots, or weak parts.
In traditional methods, a mold maker may not find these problems until the first mold test. Fixing them costs time and money. But with a digital twin, the design is tested in a virtual world first. That means fewer surprises and better results.
Key Benefits of Digital Twin Tech in Mold Making
1. Faster Design and Testing
Designing a mold takes time. Testing it takes even more. A digital twin cuts this time. It allows a mold maker to test multiple designs quickly and choose the best one.
They can:
- Try different gate locations
- Test wall thickness
- Simulate warpage
- Analyze cooling times
All before the mold is built. This speeds up the whole housing injection molding process.
2. Better Quality Parts
Quality is everything in molded plastic housings. Poor quality leads to defects, customer returns, and lost business.
With a digital twin, the mold maker can fix issues early. They can check if the plastic flows smoothly. They can adjust the design to avoid sink marks or stress lines. That means the final part is better right from the start.
3. Lower Cost Over Time
Building a mold is not cheap. Changes after steel cutting cost even more. Each adjustment means time, labor, and material.
Digital twin tech helps get it right the first time. A mold maker using this tool avoids rework. This keeps the project on budget and lowers waste.
4. Smarter Maintenance and Monitoring
Some digital twins go beyond design. They connect to sensors on the real mold. This lets the mold maker track wear, temperature, and cycle count in real time.
The system can predict when to clean or repair the mold. This prevents breakdowns and extends the mold’s life.
How a Mold Maker Uses Digital Twins in Practice
A skilled mold maker doesn’t just build molds—they plan, simulate, and refine them. Here’s how they use digital twin tech step by step:
Step 1: Design the Plastic Housing
First, the CAD model of the housing part is built. This model includes all details—ribs, holes, bosses, and snaps.
Step 2: Build the Digital Twin
The mold maker creates a digital version of the mold using CAD and simulation tools. This includes:
- Core and cavity shapes
- Cooling lines
- Gating system
- Ejector system
Step 3: Simulate Molding Conditions
Using the digital twin, the mold maker runs simulations. They test how the plastic flows into the mold, how it cools, and how the part will shrink.
They adjust the design to fix any weak points or warping.
Step 4: Finalize and Build the Mold
Once the digital twin performs well, the mold is built. The real mold closely matches the tested digital version.
Step 5: Monitor Mold Performance
After production starts, the digital twin can continue to help. If the mold has sensors, data can feed back to the twin. The mold maker then knows if the mold needs service or if something is going wrong.
Applications in Different Industries
Digital twin tech works well in many areas of housing injection molding:
Electronics
For phone cases, laptop housings, and game consoles, digital twins ensure tight fit and clean surface finishes.
Medical
In medical equipment, parts must be perfect. A mold maker uses digital twins to avoid risk and meet safety rules.
Automotive
Car dashboards and control panels need exact fit and finish. Digital twins help design molds that can handle long cycles and tough parts.
Home Appliances
From air conditioner panels to washing machine control covers, digital twins help create molds that last longer and run better.
The Role of the Mold Maker
Even with smart tools, a human expert is still key. A mold maker uses experience to guide the process. They know when a design works or needs change. They can look at digital results and make the right call.
AI and digital twins are tools. The mold maker is the one who brings them to life.
The Future of Housing Injection Molding with Digital Twins
This technology is growing fast. In the next few years, we’ll see even more:
- Real-time digital twins connected to smart factories
- Automatic feedback loops from the mold to the design system
- AI-based tools that design molds on their own
For now, smart companies are already using digital twins to speed up housing injection molding. They work with mold makers who use the latest tools to stay ahead.
Conclusion
Digital twin technology is a big step forward in housing injection molding. It helps reduce mistakes, speed up design, and improve product quality. A skilled mold maker can use this tool to plan better molds and deliver top results.
Whether you’re making a phone case, medical cover, or automotive panel, digital twins make the job smoother. In today’s fast world, they give you an edge. And in the hands of an experienced mold maker, that edge becomes a real advantage.
If you’re planning your next mold project, ask your mold maker if they use digital twin technology. It could save you time, money, and stress—while delivering better plastic housing molds than ever before.