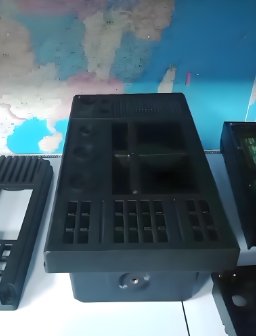
In today’s fast-moving world of product development, companies often face a big choice: 3D printing or housing injection molding? Both are used to make plastic housings for all kinds of devices—from electronics to appliances. But they work in very different ways.
If you’re designing a plastic housing, you want parts that are strong, good-looking, and affordable. You also want them made fast. Choosing the right process depends on your needs. In this article, we’ll compare 3D printing and housing injection molding. We’ll explain what each one does best and when to work with a skilled mold maker.
Let’s start by looking at how both processes work.
What Is Housing Injection Molding?
Housing injection molding is a process where melted plastic is injected into a steel mold. The plastic cools, hardens, and becomes the final part. The mold maker designs and builds the mold, which shapes the part and allows it to be made over and over again.
This method is perfect for mass production. Once the mold is ready, each part can be made in seconds. It’s fast, accurate, and great for making thousands—or even millions—of housings.
What Is 3D Printing?
3D printing builds parts layer by layer. It starts with a digital model. Then, a machine adds material, one layer at a time, until the part is complete. This process is also called additive manufacturing.
3D printing works well for small batches or test models. You don’t need a mold, and you can change the design easily. But it’s much slower than molding, and the part finish isn’t always smooth.
Cost Comparison
Housing injection molding has high upfront costs. A mold maker must design and build the mold, which takes time and money. But once the mold is done, each part costs very little to make. That’s why injection molding is the best choice for large production runs.
3D printing, on the other hand, has low setup costs. There’s no mold, so you save money at the start. But each part takes longer to make and uses more expensive material. As a result, 3D printing becomes expensive if you need many parts.
If you’re making:
- 10 to 50 parts → 3D printing is cheaper.
- 500 or more parts → Housing injection molding wins.
A smart mold maker will help you understand this break-even point for your project.
Speed to Market
When it comes to speed, both methods offer benefits.
With 3D printing, you can go from design to part in just a few hours. It’s perfect for testing ideas or making quick samples. You can print a part, test it, change it, and print again—all in a day.
Housing injection molding, however, takes longer to start. The mold must be designed, machined, and tested. This can take a few weeks. But once the mold is ready, thousands of parts can be made very quickly.
If your goal is to launch fast and test often, start with 3D printing. But when you’re ready to mass-produce, work with a mold maker and switch to molding.
Part Quality and Surface Finish
This is where housing injection molding really shines. The plastic parts come out smooth and clean, with a professional look. You can add fine details, logos, or textures directly into the mold. A good mold maker ensures every part looks perfect.
3D printed parts often have visible lines or rough textures. Some high-end printers can reduce this, but it still won’t match molded quality. Post-processing like sanding or painting adds time and cost.
For high-end consumer products, housing injection molding is the better choice for final parts.
Material Options
Both methods support a range of materials, but there are some differences.
Housing injection molding supports many types of plastics—ABS, PC, PP, and more. These are strong, durable, and can be customized with additives.
3D printing offers fewer plastic options, especially for high-volume production. While some printers use strong materials like nylon or polycarbonate, they may not match the performance of injection-molded plastics.
A skilled mold maker can help you choose the right material for strength, flexibility, or temperature resistance in your molded housings.
Design Flexibility
3D printing is great for design freedom. You can print complex shapes, hollow sections, or internal channels. You’re not limited by mold tools. That’s why designers love using 3D printing in early stages.
But once the design is final, housing injection molding takes over. It may require some changes to make the part moldable—like adding draft angles or changing wall thickness—but the result is strong, clean, and consistent.
A good mold maker helps optimize your design for molding without losing function or style.
Scaling Up: From Prototype to Production
Here’s a smart strategy: use both.
Start your project with 3D printing. Test your design. Make sure everything fits and works. Once the design is proven, switch to housing injection molding for full production.
This way, you save money during development and get the benefits of molding when it counts. A trusted mold maker can guide you through this transition. They’ll take your printed part and turn it into a mold-ready design.
Long-Term Cost and Time Savings
While 3D printing offers speed at the start, it becomes costly and slow as volume increases. Housing injection molding, though slower to begin, pays off in the long run.
Once the mold is made:
- Each part costs less
- Production time drops
- Quality stays high
Your mold maker is a key partner in this. They help you plan, budget, and get the most from your mold investment.
Environmental Impact
Both methods can be eco-friendly, but they have trade-offs.
3D printing creates less waste since it adds only what’s needed. But it uses more energy per part and often requires post-processing.
Housing injection molding may create some waste (like runners or sprues), but each cycle is highly efficient. Plus, many plastics used can be recycled or reused.
An experienced mold maker can design molds that reduce waste and energy use.
Final Thoughts: Which One Is Right for You?
Use this guide to help choose:
- Want a few samples fast? Try 3D printing.
- Need hundreds or thousands of plastic housings? Choose housing injection molding.
- Want top quality, strength, and appearance? Go with molding.
- Want to test many ideas quickly? Start with 3D printing.
The best plan often uses both. Start smart. End strong.
And remember, a trusted mold maker can help you every step of the way—from 3D prints to final production. They make sure your plastic housing is made right, on time, and at the best cost.
By working closely with a skilled mold maker, your housing injection molding project is more likely to succeed. It’s not just about tools and machines—it’s about smart planning and expert help.