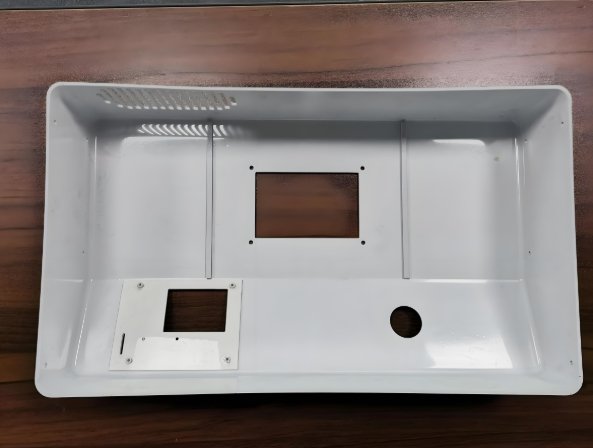
The world of housing injection molding is moving fast. New technologies, eco-friendly materials, and advanced automation are changing how plastic housings are designed and produced. As industries like electronics, automotive, and medical devices grow, the demand for smarter, faster, and more sustainable molding solutions continues to rise.
At the center of this change is the mold maker. A skilled mold maker does more than cut steel. They bring ideas to life, make production efficient, and use the latest tools to help companies keep up with new trends.
Let’s explore what the future holds for housing injection molding and why partnering with an expert mold maker will be more important than ever.
Smarter Mold Design with AI and Simulation
In the future, mold design won’t rely on trial and error. AI tools and simulation software will help mold makers design better molds in less time. These programs can:
- Predict material flow
- Avoid defects before cutting steel
- Choose the best gate and cooling system
- Suggest changes to improve cycle time
With this technology, mold makers can deliver high-quality molds that work well from the start. That saves both time and money during production.
This new way of working also means tighter collaboration between product designers and mold makers, helping ideas move faster from sketch to real part.
Digital Twins and Virtual Testing
One of the biggest future trends in housing injection molding is the use of digital twins. A digital twin is a full 3D model that copies the real mold and simulates how it works.
Before the mold is built, the digital twin tests:
- How the plastic will fill the mold
- Cooling patterns
- Part ejection and shrinkage
This virtual testing helps mold makers and engineers fix problems early. It cuts down on trial runs, mold changes, and delays.
As digital twin technology improves, it will become a normal step in the housing injection molding process.
Smart Factories and Full Automation
Smart factories are changing how injection molding works. Machines now use sensors and robots to handle many tasks automatically. This includes:
- Loading and unloading parts
- Quality checks with cameras
- Real-time data tracking
- Automatic shutdowns if issues occur
Housing injection molding will be more automated, with fewer people needed to run the machines. Instead, workers will focus on monitoring systems and solving complex problems.
A forward-thinking mold maker will design molds that work smoothly with automation. This includes features like:
- Easy part ejection for robots
- Mold sensors for better monitoring
- Durable parts that reduce downtime
Eco-Friendly Materials and Processes
Sustainability is a key part of the future. Many companies are now looking for greener ways to make plastic housings. This includes:
- Using recycled plastics
- Biodegradable resins
- Reducing material waste
- Lowering energy use during molding
To do this, mold makers must rethink how molds are built. A mold for eco-resins might need different cooling or gating systems. Also, the mold may need special coatings to resist wear from recycled plastics.
The mold maker plays a big role in helping companies meet their green goals without losing product quality.
Modular Mold Systems
To reduce costs and speed up production, many companies will turn to modular mold systems. These molds use standard base parts but allow for quick swaps of cavity inserts to make different housings.
Benefits include:
- Faster changeovers
- Less storage space
- Lower tooling costs
This approach fits well with small-batch housing injection molding and custom housing needs.
A smart mold maker can help design these modular systems to fit the client’s production plans and part designs.
Greater Role for the Mold Maker
As the industry evolves, the role of the mold maker is also changing. They are no longer just tool builders. In the future, mold makers will act as technical partners, helping companies:
- Choose the right plastic and mold type
- Design parts for easy molding
- Plan for automation and quality control
- Maintain and upgrade molds over time
This deeper relationship helps reduce risk and improve product success.
Industry 4.0 in Injection Molding
Industry 4.0 connects machines, data, and people through the internet. In housing injection molding, this means:
- Machines that talk to each other
- Live monitoring of mold wear and performance
- Alerts when parts need replacement
- Better scheduling of maintenance
These smart systems reduce downtime and improve product quality.
To use Industry 4.0 tools well, your mold maker must design molds that include the right sensors, materials, and connectivity features.
Customization and On-Demand Production
As consumer products become more personal, the need for custom plastic housings is growing. In the future, housing injection molding will support more on-demand and small-batch runs.
This means:
- Quicker mold changes
- Modular or 3D-printed mold inserts
- Flexible automation systems
Mold makers who offer fast turnaround and custom mold design will stand out in this space. They must be ready to work with unique designs and deliver results quickly.
Global Collaboration, Local Manufacturing
Many companies now work with teams across the world. Still, there is a rising demand for local mold production due to faster shipping, better communication, and tighter quality control.
In the future, successful mold makers will offer both global support and local services. They will:
- Provide fast prototype molds
- Work in multiple languages and standards
- Help companies produce housings close to their final markets
Final Thoughts
The future of housing injection molding is full of exciting changes. Smarter machines, cleaner materials, and advanced design tools are transforming how we make plastic housings.
But none of this works without skilled mold makers who understand both new technology and traditional tooling. They will be the link between ideas and real-world production, helping companies succeed in a fast-moving market.
If you want to stay ahead, partner with a future-ready mold maker. They will help you use automation, eco-materials, and smart tools to make plastic housings faster, cleaner, and more cost-effective.
As the world keeps changing, housing injection molding will remain a key process. And with the right mold maker by your side, your business will be ready for whatever comes next.