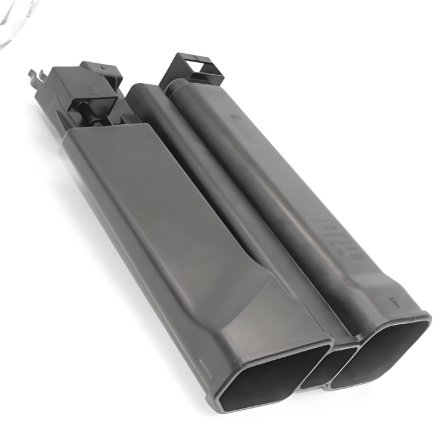
In housing injection molding, warping is one of the most frustrating problems. When a plastic part bends or twists out of shape, it causes serious issues in assembly, appearance, and product performance. For industries that depend on precise plastic housings—like electronics, automotive, and medical—this kind of defect can’t be ignored.
But what causes warping, and how can it be fixed? The answer lies in material behavior, process settings, and the design of the mold. An experienced mold maker understands these factors well and knows how to design and optimize tools to reduce warping.
This article explores the causes of warping in housing injection molding, and most importantly, the best ways to fix and prevent it.
What is Warping in Housing Injection Molding?
Warping means the molded plastic part bends, twists, or deforms from its intended shape. Instead of coming out straight and flat, the part may curve, bow, or ripple.
In housing injection molding, warping is especially troublesome because housings must fit tightly with other parts. If one side is even slightly bent, the product may not close properly, screws may not align, or electronic components may be exposed.
Why Warping Happens
Several factors can lead to warping in housing injection molding:
1. Uneven Cooling
Plastic shrinks as it cools. If one side of the part cools faster than the other, that side shrinks more, pulling the part out of shape.
2. Poor Mold Design
If the mold doesn’t allow even temperature control or has uneven wall thickness, parts will warp.
3. Improper Material Choice
Some plastics are more prone to warping than others. A skilled mold maker always considers material properties when designing a mold.
4. High Internal Stress
When plastic flows into the mold, it may stretch or bend. If that stress is frozen in place during cooling, it can later cause warping.
5. Incorrect Process Settings
Injection pressure, temperature, and cooling time all play a role. Wrong settings increase the chance of warping.
How to Fix Warping in Plastic Housings
1. Optimize Mold Temperature
Even mold temperature is key. If one side of the mold is hotter or colder than the other, the part won’t cool evenly.
An experienced mold maker will design the mold with proper cooling channels. These help the plastic cool at the same rate on all sides, reducing stress and shrinkage differences.
2. Adjust Wall Thickness
Thick walls cool slower than thin ones. If wall thickness varies too much, it causes uneven cooling and shrinkage.
Good housing design avoids extreme changes in wall thickness. If a thicker section is needed, the mold maker may add coring or ribs to balance the thickness while keeping strength.
3. Use Proper Gate Location
The gate is where the plastic enters the mold. Its location affects how plastic flows and fills the cavity.
Poor gate placement can create uneven flow and pressure, leading to stress and warping. A skilled mold maker knows how to place gates in locations that minimize stress and allow smooth flow.
4. Slow Down the Injection Speed
Injecting plastic too fast causes high pressure and turbulence, which builds internal stress. Slowing down the injection speed can allow smoother flow and reduce built-in tension.
It also gives the plastic more time to settle in the mold cavity. This improves stability during cooling.
5. Increase Cooling Time
Sometimes, warping happens because the part is removed too soon. If the plastic hasn’t fully solidified, it continues to shrink after ejection.
Extending the cooling time allows the part to set completely before being ejected. A reliable mold maker will calculate the best cycle time based on material type and part thickness.
6. Choose the Right Material
Different plastics shrink differently. For example, semi-crystalline materials like nylon shrink more than amorphous materials like ABS.
If warping is a concern, switch to a plastic that shrinks less or warps less easily. A mold maker familiar with housing parts will recommend materials with good dimensional stability.
7. Use Mold Flow Simulation
Before building the mold, many mold makers use simulation software to test how the plastic will flow and cool. These digital tools help detect potential warp zones early.
With this information, the mold maker can adjust the mold design or processing settings to prevent warping before production begins.
8. Add Ribs or Support Features
Long flat surfaces are more likely to warp. Adding ribs or slight curves can strengthen the part and help it hold its shape.
Ribs don’t have to be thick—they just need to support the plastic and reduce warping stress. A smart mold maker will design ribs that also match cosmetic requirements.
Fixing Warping After It Happens
Sometimes warping is only discovered after production starts. Here’s how to fix it fast:
- Tune process settings: Lower injection pressure, increase cooling time, or adjust mold temperature balance.
- Check mold cooling lines: Make sure they are not blocked or damaged.
- Dry the resin better: Moisture in plastic can cause uneven shrinkage.
- Try annealing: Gently heat the part to relax internal stresses and reshape it.
In all cases, consult the mold maker. They know the design and can offer exact guidance.
The Role of the Mold Maker
No one knows more about preventing warping than a seasoned mold maker. They bring years of experience to every mold and understand how material, flow, cooling, and ejection all work together.
When warping appears, they can:
- Analyze part geometry
- Adjust the mold or cooling system
- Suggest better materials
- Recommend improved process settings
Choosing the right mold maker can save you time, money, and wasted parts. They help ensure your housing injection molding project produces flat, strong, and perfectly shaped housings every time.
Real Example
One electronics company had a warped remote control housing. The bottom half of the shell would curve upward after cooling, causing gaps when screwed to the top half.
The mold maker discovered uneven cooling across the mold. One half had blocked water lines. After fixing the lines and adding a rib to the underside, the housing molded flat.
Now the customer runs 20,000 parts per month with no warp issues.
Conclusion
Warping is a major issue in housing injection molding, but it’s not impossible to solve. With proper mold design, good material choice, and smart process control, warping can be fixed and even prevented.
The most important step is choosing a qualified mold maker. Their knowledge ensures your plastic housings come out perfect—flat, straight, and ready to use.
For high-precision parts, trust a mold maker who understands how every detail affects warping. Your product’s quality depends on it.