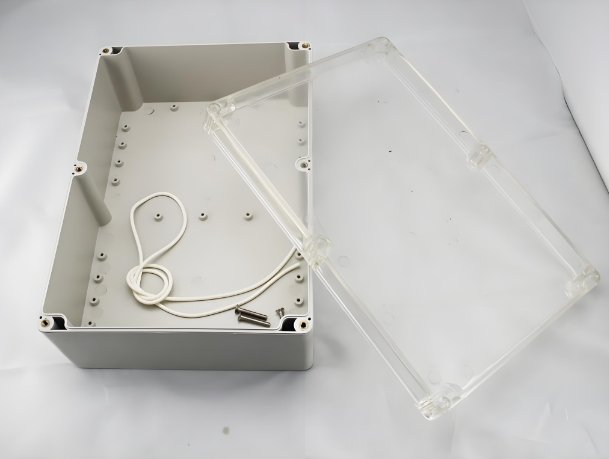
Cracking is one of the most frustrating problems in housing injection molding. It can delay production, increase scrap, and damage your brand reputation. Even worse, many manufacturers don’t understand why the cracks happen or how to stop them. In this article, we explore the root causes of mold cracking and how an experienced mold maker can help you solve them.
What Is Mold Cracking?
In housing injection molding, “mold cracking” often refers to two things:
- Cracking of the molded plastic housing
- Cracking or failure of the metal injection mold itself
Both are serious issues. Both affect cost, cycle time, and product quality. And both can be avoided when you follow the right steps with the help of a skilled mold maker.
Let’s break down each one and explore solutions.
Cracks in Molded Plastic Housings
Plastic housings are used in many industries—from electronics to automotive. But when these parts crack, it’s often due to issues that start before the first shot.
1. Poor Mold Design
Design flaws are a top reason for cracking. Thin walls, sharp corners, and uneven cooling can all create weak spots. If the mold doesn’t allow the material to flow evenly or cool properly, internal stress builds up in the housing.
A smart mold maker will:
- Avoid sharp corners by adding radii
- Maintain even wall thickness
- Design proper flow channels and gates
- Optimize venting and ejection paths
By doing so, they ensure smooth housing injection molding and reduce stress in the plastic.
2. Wrong Material Selection
Each plastic has its own behavior. Some are flexible, others are brittle. Using the wrong plastic for a structural housing may lead to cracking under pressure or heat.
A mold maker with experience in housing injection molding will guide you toward the right material. For instance:
- ABS is tough and impact-resistant
- PC is strong and clear, but needs careful cooling
- Nylon can warp if not dried properly
Choosing the right resin is critical. So is keeping it dry and at the correct temperature.
3. Poor Processing Conditions
Even with a good mold and good resin, the process still matters. Wrong settings during housing injection molding can cause cracks. These include:
- Injection speed that is too fast
- Holding pressure that is too high
- Cooling time that is too short
- Poor mold temperature control
All of these introduce stress into the part. That stress may not show right away. But over time—or under pressure—the housing will crack.
An expert mold maker will help define the best process window. They will test and validate the settings before mass production.
4. Improper Ejection
When the part is pushed out of the mold, it should come out clean and stress-free. But if the ejector pins are in the wrong spots or there is drag, the part may flex. That flexing can cause small cracks—especially in thin areas or corners.
A professional mold maker ensures the ejection system is balanced and properly placed. They may also recommend surface treatments or coatings to help release the part smoothly.
Cracks in the Metal Mold
Cracking in the steel mold itself is even more serious. Mold repair or rebuilds are costly and can halt production for weeks.
Here’s why it happens.
1. Low-Quality Steel
A mold must handle high pressure, heat, and repeated use. If it’s made from poor-quality steel, it may not last. In housing injection molding, the mold must also withstand thermal cycling and clamping force.
Top mold makers use high-grade steel like P20, H13, or S136. They match the steel grade to the resin type and expected cycle count.
2. Bad Heat Treatment
Steel needs to be heat treated to the right hardness. Too soft—and it wears out. Too hard—and it becomes brittle. Improper heat treatment can lead to tiny cracks, especially near sharp edges or thin cores.
A skilled mold maker follows precise heat treatment specs. They also test the hardness and structure before final assembly.
3. Poor Mold Design
Just like with plastic parts, poor mold design can lead to stress. Thin inserts, sharp transitions, or unsupported areas may flex during molding. That movement leads to fatigue and cracking.
Good mold design balances strength, cooling, and precision. It avoids unnecessary complexity and reduces areas of high stress.
4. Improper Maintenance
Even the best mold needs regular care. If cooling lines get clogged or surfaces wear out, the mold may overheat or lose balance. That causes expansion, stress, and—eventually—cracks.
A good mold maker builds molds with maintenance in mind. They make it easy to clean, polish, and replace parts. They also train your team on how to keep the mold in top shape.
How to Prevent Mold Cracking
Cracking is not a mystery. It’s a sign that something went wrong. The good news? You can stop it before it starts by working with the right mold maker.
Here are key prevention tips:
- Work with experienced designers
Make sure they understand the full requirements of your housing. - Select proper materials
Match the resin to the product environment—heat, impact, chemicals, etc. - Use simulation tools
Mold flow analysis helps predict weak spots and fix them early. - Test process parameters
Don’t guess. Use real data to set temperature, pressure, and timing. - Design for durability
In both the mold and the part, add strength where it matters most. - Plan for maintenance
Include easy-access points, cleaning procedures, and monitoring sensors.
Conclusion
Cracking in housing injection molding is not just a nuisance. It signals deeper problems that could cost you thousands of dollars and your customers’ trust. Whether it’s the molded housing or the mold itself, cracking usually comes from poor planning, bad materials, or weak process control.
That’s why working with a reliable mold maker is essential. A true expert doesn’t just build a mold. They understand your product, simulate performance, test materials, and fine-tune the entire molding system.
So the next time your plastic housing cracks, don’t just blame the material. Look deeper. With the right team, the right tools, and the right mindset, you can solve the problem for good—and build a product that lasts.