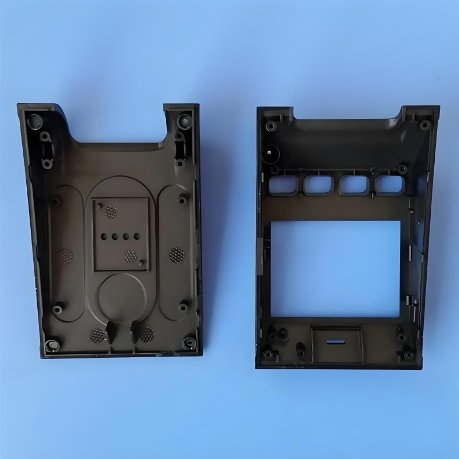
In the world of housing injection molding, fit is everything. When two molded parts come together, they must align perfectly. Whether it’s an electronics case, appliance shell, or industrial enclosure, precision matters. Poor fit leads to misalignment, loose joints, rattling parts, and customer complaints.
Achieving the perfect fit is both a science and an art. It starts with smart design, involves accurate tooling, and depends on expert process control. Every mold maker involved in housing injection molding understands that fit is not just a cosmetic issue—it directly affects functionality and quality.
In this article, we’ll explore how to improve fit in injection molded housings. We’ll cover the common causes of poor fit, design strategies, tooling considerations, and molding process improvements. With these insights, your next molded housing can meet the highest standards.
Why Fit Is So Important in Housing Injection Molding
When two or more parts of a plastic housing need to snap, slide, or press together, the dimensions must be exact. A poor fit can lead to:
- Gaps and seams
- Stress during assembly
- Part failure under pressure
- Leaks in weatherproof designs
- Noise from movement
Precision in housing injection molding ensures structural strength, aesthetic quality, and reliable function. That’s why a good mold maker focuses so heavily on dimensional accuracy.
What Causes Poor Fit?
Before we improve fit, we need to understand why parts don’t fit properly. Here are the main causes:
1. Shrinkage Variations
Every plastic material shrinks as it cools. If not accounted for properly, parts end up too large or too small. Shrinkage varies by:
- Material type
- Wall thickness
- Cooling time
- Mold temperature
Even small variations can throw off the fit in housing injection molding.
2. Poor Mold Tolerances
If the mold maker builds the tool with loose tolerances or machining errors, the final parts won’t match. Mold precision directly affects part accuracy.
3. Warping and Distortion
Uneven cooling or poor part design can cause warping. A part that curls or twists will never fit properly with another.
4. Tool Wear or Flash
Over time, molds wear down. Edges round off. Parting lines may develop flash. These subtle changes affect the final part dimensions.
5. Process Instability
Inconsistent machine settings, material batches, or cycle times all lead to variation in fit. Housing injection molding requires strict process control to maintain repeatability.
Design Tips for Better Fit
The best way to improve fit is to start at the design stage. Consider these strategies:
1. Use Proper Tolerances
Injection molding has natural variation. Don’t expect tight metal-like tolerances unless you plan for them. Follow general guidelines:
- ±0.1 mm for normal features
- ±0.05 mm for fine features (with close control)
- Increase tolerances for long or complex parts
Ask your mold maker to review tolerances before mold construction.
2. Design Self-Locating Features
Good fits rely on more than just matching edges. Use design features that align automatically, such as:
- Snap fits
- Tabs and slots
- Locating pins
- Interlocking ribs
These features improve repeatability and reduce assembly error in housing injection molding.
3. Avoid Thick-to-Thin Transitions
Thick areas cool slowly and shrink more. Uneven wall thickness causes warping and poor fit. Keep walls as uniform as possible.
Use ribs for strength instead of thick walls. Your mold maker can simulate shrinkage and help you avoid bad geometry.
4. Add Draft to Fitting Surfaces
Draft angles help parts release from the mold. Without draft, parts may drag and deform. Add 1–2° of draft to vertical surfaces, including those that must fit together.
Careful design with proper draft improves fit and protects part quality.
Mold Maker’s Role in Improving Fit
The mold maker plays a critical role in achieving tight fit. Their work includes:
1. Accurate Mold Machining
High-precision CNC equipment and skilled technicians ensure the mold dimensions match the design exactly. Even a 0.01 mm error can ruin a tight fit in housing injection molding.
2. Material Shrinkage Compensation
Experienced mold makers understand material shrinkage rates. They adjust the mold size accordingly, using real-world data and simulation tools.
3. Steel Type and Mold Stability
Mold steel should resist wear and hold tight tolerances over time. High-volume housing injection molding requires durable molds made with high-quality tool steel.
4. Polishing and Fit Adjustments
Final polishing ensures critical shutoffs and parting surfaces are smooth and tight. The mold maker can also hand-fit features like snap fits and press fits to improve assembly.
Molding Process Tips to Improve Fit
Even a perfect mold won’t produce accurate parts without careful process control. Here are key steps:
1. Optimize Packing Pressure
Packing pressure fills out the part completely. Insufficient pressure causes sink marks and short shots. Too much pressure causes stress and flash. Your mold maker will help you find the sweet spot.
2. Balance Cooling
Uneven cooling causes parts to warp. A good cooling system, with channels near thick zones, prevents distortion. Mold flow simulation helps optimize this.
3. Maintain Stable Machine Settings
Run each cycle with the same temperature, pressure, and speed. Keep material moisture and batch consistent. Variations increase dimensional differences.
4. Use Scientific Molding
Scientific molding techniques—like cavity pressure sensors, fill time studies, and gate freeze analysis—provide data for consistent results. This level of control improves fit significantly in housing injection molding.
Assembly Fixtures and Inspection
To ensure parts always fit during production, use assembly fixtures to test alignment. This allows early detection of fit issues.
Dimensional inspection tools like CMMs (Coordinate Measuring Machines) help check part size against tolerance. Work closely with your mold maker and quality team to validate fit during initial production runs.
Continuous Improvement
Even after production begins, always look for ways to improve fit:
- Use part data to refine mold design
- Adjust process windows for better control
- Rework molds when wear is detected
- Modify designs slightly for better alignment
Fit improvement is a team effort. The designer, mold maker, and process engineer must work together through every step of housing injection molding.
Conclusion
Perfect fit in plastic housings doesn’t happen by chance. It results from careful planning, expert toolmaking, and precise process control.
Key takeaways to improve fit in housing injection molding include:
- Design with tolerances and features that aid alignment
- Work with a skilled mold maker to build an accurate and durable mold
- Control shrinkage, cooling, and pressure during molding
- Inspect and adjust throughout production
With these strategies, your molded housings will assemble smoothly, stay aligned, and meet all your quality goals. Better fit leads to better products—and happier customers.