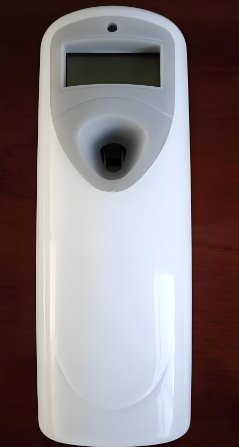
In today’s market, plastic housings must be durable, precise, and long-lasting. Whether the product is a consumer gadget or an industrial device, the housing must protect internal parts while maintaining structural strength. In housing injection molding, part strength is a key factor that determines product reliability. A weak housing can lead to cracks, failures, and even safety risks.
As a skilled mold maker knows, the strength of a molded part depends on several factors. It’s not just about the plastic material. Mold design, processing parameters, wall thickness, and internal features all play a role. This article explains how to improve the strength of your molded plastic housings using practical methods from real-world experience.
By the end, you’ll understand how top housing injection molding professionals work with design engineers and the mold maker to produce strong, high-quality housings.
Why Part Strength Matters in Housing Injection Molding
Plastic housings serve more than just cosmetic functions. In electronics, medical, and industrial applications, housings must:
- Protect sensitive internal components
- Resist pressure, impact, and vibration
- Maintain shape under heat and load
- Provide structural support for other parts
If a housing cracks or deforms, it can damage the product or cause a total failure. That’s why achieving good mechanical strength is critical in housing injection molding.
1. Choose the Right Plastic Material
Material selection is the foundation of strong molded parts. Not all plastics have the same strength properties. A professional mold maker often works with the design team to choose the right resin for each application.
Recommended materials for strong housings:
- Polycarbonate (PC): High impact resistance, good dimensional stability
- Nylon (PA): Excellent toughness, wear resistance
- ABS: Good balance of strength, stiffness, and cost
- Glass-filled polymers (e.g., GF-Nylon): Higher strength and stiffness
In housing injection molding, avoid materials that shrink unevenly or become brittle over time.
2. Optimize Wall Thickness
Wall thickness has a major effect on strength. Thin walls can lead to warping or cracking. However, thick walls can cause sink marks or long cooling times.
Best practices:
- Maintain uniform wall thickness throughout the part
- Avoid sharp thickness transitions
- Use ribs or gussets instead of thick walls for added strength
- Aim for 2–3 mm walls in most housing designs
Every mold maker understands the balance between strength and manufacturability. That’s why they help adjust wall dimensions for strength and proper mold filling.
3. Add Structural Ribs and Supports
Ribs are one of the best ways to increase the structural integrity of plastic housings without increasing weight.
Design tips for ribs:
- Rib thickness: 50–70% of the wall thickness
- Rib height: No more than 3 times the wall thickness
- Add draft angles to prevent sticking in the mold
- Space ribs evenly to avoid stress concentration
When working with an experienced mold maker, these features are carefully included in the mold design to ensure strong, reliable parts.
4. Improve Corner Radii and Transitions
Sharp corners can act as stress concentrators, leading to cracks during use. Rounded corners distribute stress more evenly and improve flow during molding.
Best practices:
- Use internal radii of at least 0.5–1 mm
- Avoid sharp transitions in geometry
- Use fillets at the base of ribs and bosses
These small changes have a big impact on part durability in housing injection molding.
5. Pay Attention to Bosses and Inserts
Bosses are raised cylindrical features used for screws or alignment. If not properly designed, they can become weak points.
Tips for stronger bosses:
- Support bosses with ribs
- Avoid placing bosses too close to part edges
- Use the correct boss-to-wall ratio
- Add metal inserts only where needed, with overmolding if possible
A skilled mold maker always considers reinforcement in boss areas to avoid stress cracking or stripping.
6. Use Fiber or Glass Fillers for Extra Strength
Glass-filled materials can improve part strength by up to 60%. These materials resist deformation and add stiffness.
Important points:
- Glass fibers should align with flow for optimal strength
- Use fillers that match thermal and chemical needs
- Be aware that glass-filled materials increase mold wear
In housing injection molding, the choice to use fillers must be coordinated with both the design team and the mold maker for best results.
7. Control the Cooling Process
Uneven cooling can cause internal stresses that weaken the housing. A proper cooling system within the mold helps eliminate this problem.
Tips for strong parts:
- Use consistent mold temperatures
- Avoid sudden changes in wall thickness
- Use mold flow analysis to optimize cooling channels
- Keep cycle times consistent to reduce shrinkage variation
Cooling is not only about speed. A mold maker carefully designs cooling lines to improve part quality and strength.
8. Set the Right Processing Parameters
Injection pressure, temperature, and speed all affect how well the material flows and bonds within the mold. Incorrect settings lead to weak weld lines, voids, or incomplete filling.
Key settings:
- Proper melt temperature (depends on resin type)
- Balanced injection speed and pressure
- Sufficient packing time to avoid sink marks
- Proper venting to remove trapped air
With help from the mold maker, these settings can be dialed in to improve strength in every housing injection molding cycle.
9. Avoid Weld Lines in Critical Areas
Weld lines are weak spots where two melt fronts meet. These areas have poor bonding and often fail under stress.
How to reduce weld lines:
- Relocate gates to avoid welds in load-bearing areas
- Use flow simulation to detect problem zones
- Increase injection speed or mold temperature to improve bonding
- Add ribs or thicker walls to reinforce weld line areas
Your mold maker can adjust runner and gate design to eliminate weld lines or move them to non-critical areas.
10. Design with Assembly in Mind
Housings often include snap fits, hinges, or locking features. These need extra strength to perform properly over time.
Tips:
- Use generous radii at snap joints
- Avoid over-flexing snap arms
- Use living hinges only with suitable materials (e.g., PP)
- Include stress relief features to extend part life
In housing injection molding, part strength isn’t just about the material—it’s also about how the parts are used.
Conclusion
Improving part strength in molded housings is not just a one-step fix. It requires collaboration between designers, process engineers, and the mold maker. By combining smart design, proper material selection, precise mold building, and controlled processing, you can achieve strong, reliable plastic housings.
Checklist for stronger housings:
- Choose high-performance resins
- Keep wall thickness uniform
- Add ribs and supports strategically
- Use smooth transitions and generous radii
- Avoid weld lines in key areas
- Design with assembly in mind
- Work closely with your mold maker from the start
In the world of housing injection molding, strength begins with smart decisions—and ends with excellent execution.