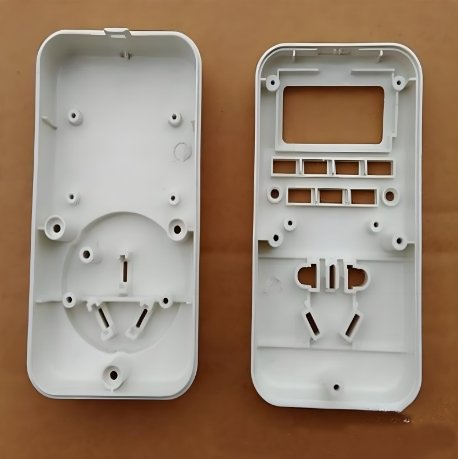
In the competitive world of housing injection molding, speed matters. From concept to final product, reducing lead time can be the difference between market success and missed opportunity. Whether launching a new electronic device or upgrading an appliance shell, customers demand fast turnaround without compromising quality.
One of the biggest time-consuming steps in this process is building the mold itself. Every mold maker knows that delays in mold fabrication directly impact production schedules. That’s why companies must follow best practices to reduce mold lead time while maintaining precision, durability, and part performance.
In this article, we share proven strategies used by experienced mold maker teams to speed up housing mold development. By the end, you’ll understand how to cut unnecessary delays and deliver products faster with confidence.
Why Lead Time Reduction Matters in Housing Injection Molding
Modern industries rely on fast product development cycles. Delays in tooling often mean lost revenue, missed sales windows, or falling behind competitors. This is especially true in housing injection molding, where custom plastic housings are needed for electronics, medical devices, and automotive parts.
Faster mold delivery helps you:
- Launch new products on time
- Respond quickly to market changes
- Lower total development costs
- Gain a competitive edge
- Satisfy customer expectations
For a professional mold maker, reducing lead time is not about cutting corners—it’s about working smarter, planning better, and using the right tools.
1. Start with Clear and Finalized Design Files
Time is often wasted when clients submit incomplete or changing CAD models. Every revision forces the mold maker to stop, rework, or even restart.
Best practice:
- Provide finalized 3D CAD files and 2D drawings before tool kickoff
- Confirm critical tolerances, material specs, and surface finishes
- Minimize late-stage design changes
- Use design freeze milestones
In housing injection molding, a strong start sets the pace for fast and smooth progress.
2. Use Mold Flow Analysis Early
Waiting until problems appear in sampling is costly and slow. Mold flow simulation tools allow the mold maker to predict how plastic will flow, cool, and shrink in the mold before cutting any steel.
Benefits of mold flow analysis:
- Spot weld lines, air traps, or filling issues
- Optimize gate and runner locations
- Reduce trial-and-error adjustments later
- Improve mold performance from the first shot
Early analysis can shave days or even weeks off the total lead time in housing injection molding projects.
3. Choose Standard Mold Bases and Components
Custom-built mold bases increase cost and lead time. Using standardized mold bases and off-the-shelf components helps reduce machining work and speeds up ordering.
Tips for using standard parts:
- Select mold bases from trusted suppliers
- Choose common ejector pins, guides, and bushings
- Avoid custom-designed mold frames unless necessary
Most professional mold maker teams rely on a set of standard designs they can configure quickly. This approach improves consistency and turnaround.
4. Design for Manufacturability (DFM)
DFM reviews bridge the gap between product design and mold building. By reviewing part geometry early, the mold maker and client can avoid features that are hard to tool or mold.
Key DFM checks include:
- Wall thickness uniformity
- Undercuts and side actions
- Draft angles
- Rib and boss proportions
- Gate and ejector placement
In housing injection molding, a smart part design leads to faster and easier mold construction.
5. Use Modular Mold Designs
A modular mold design separates the mold into changeable inserts or cavities. This allows updates or variations without rebuilding the entire tool.
Benefits:
- Speed up design and machining
- Allow interchangeable parts for multiple versions
- Reduce future tool modification time
- Enable parallel work across mold sections
A skilled mold maker can use modular designs to reduce delays not only during the first build, but also during future iterations.
6. Streamline CNC Machining and EDM Operations
CNC and EDM are core processes in mold fabrication. Delays often happen when scheduling is poor, machine paths are inefficient, or tooling isn’t available.
Best practices:
- Use high-speed CNC machining centers
- Automate toolpath generation using CAM software
- Reduce electrode count in EDM with improved part design
- Use in-house equipment to avoid third-party wait times
Many top mold maker shops operate lights-out machining with robotics to keep machines running 24/7—cutting days off the build time.
7. Leverage 3D Printing for Mold Inserts and Prototypes
3D printing is a valuable tool for making temporary inserts, prototype parts, and even soft molds.
Applications in housing molds:
- Print cavity inserts to test geometry before steel cutting
- Use printed cores for low-volume testing
- Speed up customer approvals with visual models
3D printing helps housing injection molding teams validate ideas before committing to expensive and time-consuming tooling.
8. Reduce Rework with Digital Quality Inspection
Mold accuracy impacts final part quality. Modern mold maker teams use CMM (coordinate measuring machines), laser scanning, or vision systems to verify dimensions during machining.
Advantages:
- Catch errors early in the process
- Maintain tighter tolerances
- Minimize mold adjustments after sampling
Fewer mistakes mean fewer corrections, faster mold approval, and shorter lead times.
9. Plan for Overlapping Work Phases
Instead of waiting for each step to finish before starting the next, overlapping work helps save time.
Example overlapping tasks:
- Design parting line while finalizing part model
- Order mold base while still refining cavities
- Machine inserts while mold frame is in production
This strategy requires coordination and experience, which is why it’s a strength of advanced mold maker teams.
10. Communicate Clearly and Frequently
One of the top reasons for delays in housing injection molding is poor communication. Misunderstandings between customer and mold maker often lead to rework or idle time.
Tips for better communication:
- Use detailed RFQs with exact specifications
- Review designs together before starting
- Set milestone meetings and approvals
- Use cloud-based project tracking tools
A fast project is a well-managed one. Clear expectations and steady updates reduce backtracking and confusion.
Conclusion: Speed with Quality in Mind
Reducing lead time in housing injection molding doesn’t mean rushing through the process. It means identifying delays, optimizing workflows, and collaborating with an experienced mold maker who understands how to get the job done right—and fast.
Summary checklist to reduce mold lead time:
- Finalize CAD before tool start
- Run early mold flow analysis
- Use standard mold components
- Apply DFM principles
- Use modular designs when possible
- Automate machining with advanced equipment
- 3D print for validation and soft tooling
- Monitor quality digitally to prevent rework
- Overlap work stages strategically
- Communicate proactively with all stakeholders
By following these best practices, you’ll not only cut days or weeks from your timeline—you’ll also gain better parts, happier customers, and smoother production runs in the world of housing injection molding.